This is an example of a composite project of extruded fish feed factory, shrimp feed factory, fermented raw material, and fermented feed factory. It includes the production of 2 t/h shrimp feed and 16 t/h fish feed. The project took 8 months from design to installation.
All the aquatic feed processing equipment and fermented feed processing equipment of this project are designed and produced by Richi Machinery, the fermentation equipment is purchased by us for the customer, and the environmental protection equipment is purchased locally by the customer.
The customer of this 18 t/h shrimp feed and fish feed factory project was originally a compound feed and fermented feed processor. Since the company’s profitability is good and it is very optimistic about the future prospects of extruded feed, shrimp feed, and fermented feed, it expanded the aquatic feed mill and built a new fermented feed production line.
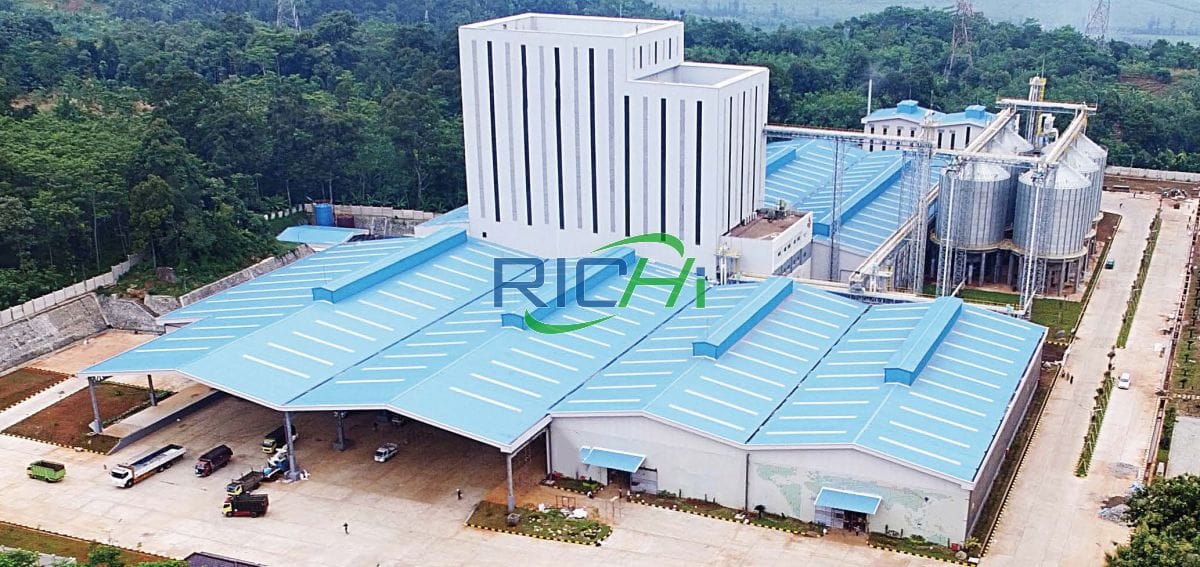
Construction content and scale
The total investment of the expansion project is 7 million US dollars (including civil works), and the total area of the project is 33367.96m². The new project relies on the existing workshops in the existing factory area and builds a 5-storey aquatic workshop with a total construction area of 3674.35m².
The project will build 1 extruded fish food production line, 1 shrimp feed production line, 1 fermented raw material production line and 1 fermented feed production line, with a production capacity of 70,000 tons, supporting environmental protection projects, etc.
After the 18 t/h shrimp feed and fish feed factory project is completed, the annual output of the whole plant will be 135,000 tons production capacity for aquatic feeds, livestock and poultry feed and feed additives.
Project composition
(1) Aquatic product workshop
Covers an area of about 517.9m², 1 extruded fish feed pellet production line and 1 shrimp feed production line, the main equipment includes cylinder initial cleaning screen, wide micro pulverizer, ultrafine pulverizer, aquatic product puffing machine, vacuum spraying machine, impeller cooler, packing scale;
(2) Fermentation raw material workshop
Covers an area of about 1227.93m², 1 production line for fermentation raw materials, the main equipment includes bucket elevator, stirring mixer, fermentation tank, counter-flow cooler, automatic packaging platform;

(3) Fermentation raw material workshop
Covering an area of about 150m², it has a fermented feed production line, and the main equipment includes a strain batching and metering system, a bacterial liquid adding system, a granular material batching and mixing system, and a packaging and metering system.
Auxiliary engineering
(1) Raw material storage area
- The raw materials of the extruded fish feed and shrimp feed production line are located in the northeast of the new aquatic product workshop;
- Fermented raw materials and raw materials for the fermented feed production line are located in the northeast of the first-phase raw material workshop.
(2) Finished product storage area
- The finished products of the 18 t/h shrimp feed and fish feed factory are located in the second-phase finished product warehouse;
- The finished product of the fermentation raw material production line is located in the fermentation raw material workshop;
- The finished product of the fermented feed production line is located in the raw material workshop of the first phase.
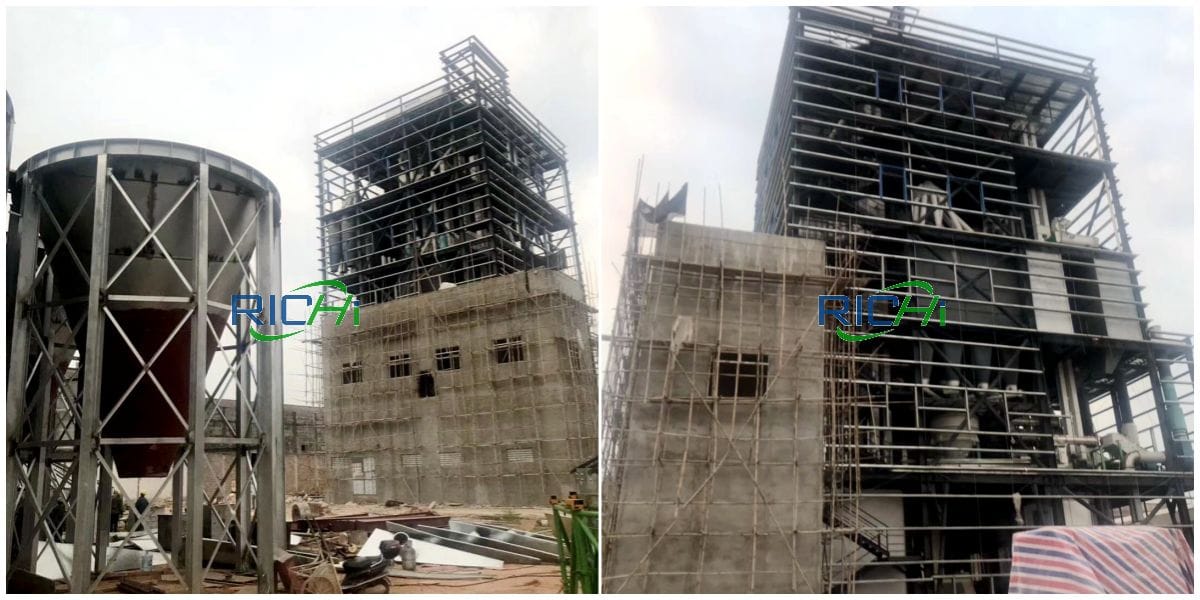
(3) Boiler room
Located in the north of the production workshop, there is one 15t/h biomass-fired steam boiler, one 8t/h biomass-fired pellet boiler, and an 8t/h biomass-fired pellet boiler for standby.
(4) Complex building
It is used for the office and life of project employees, and is located on the southeast side of the production workshop.
Production scale and product plan
Type | Before the expansion | This expansion | After the expansion |
---|---|---|---|
Shrimp Feed | 3200 | 10,000 | 13,200 |
Extruded Fish Feed | 40000n | 40000 | 80,000 |
Fermentation Ingredients | – | 13000 | 13000 |
Fermented Feed | – | 7000 | 7000 |
Chicken And Duck Feed | 10000 | – | 10000 |
Expanded Livestock And Poultry Feed | 1800 | – | 1800 |
Pig Feed | 18000 | – | 18000 |
Concentrated Feed | 6000 | – | 6000 |
Premix | 6000 | – | 6000 |
Working system
- Number of employees: The 18 t/h shrimp feed and fish feed factory project will increase 30 employees, all of whom will have board and lodging in the factory.
- Working system: Two shifts a day, 8 hours per shift, specific working hours 7:30-12:00, 13:00-16:30, 16:30-23:30, 300 days a year.
Annual consumption of raw materials
Name | Annual consumption (t/a) |
---|---|
Soybean Meal | 55728 |
Corn | 28350 |
Flour | 20520 |
Chicken powder | 810 |
Fishmeal | 540 |
Squid Cream | 432 |
Other additives (mainly salt, lime powder, flavors, amino acids, vitamins, etc.) | 8386 |
Grease | 3510 |
Bran | 10360 |
Rice Bran | 7560 |
Miscellaneous meal | 910 |
Strain | 92 |
Pellet Compound Feed Finished Product (Shrimp Feed) | 4000 (20KG/bag) |
Pellet compound feed finished product (pig feed) | 2000 (40KG/bag) |
Pellet Compound Feed Finished Products (Fish Feed) | 1000 (25KG/bag) |
18 t/h shrimp and fish feed factory process flow
Here will just show you the production process of puffed floating fish feed plant and shrimp feed production line
The biological feed of this project is made of soybean meal, corn DDGS, flour, chicken powder, etc. as the main raw materials, combined with trace ingredients such as vitamins, amino acids, and minerals, to make granular feed.
The project adopts the process of crushing first and then batching. The raw and auxiliary materials that need to be crushed (soybean meal, corn DDGS, rice bran) are respectively crushed by a grinder, and then enter the batching bin, and mixed with other raw and auxiliary materials that do not need to be crushed (fish meal, flour, etc.) .
The feed product is produced after mixing and extruding granulation process. The production process of the extruded fish feed production line and the shrimp feed production line is basically the same, except that the feed of the extruded fish feed line needs to be extruded and sprayed with grease, but the ratio of raw and auxiliary materials is different.
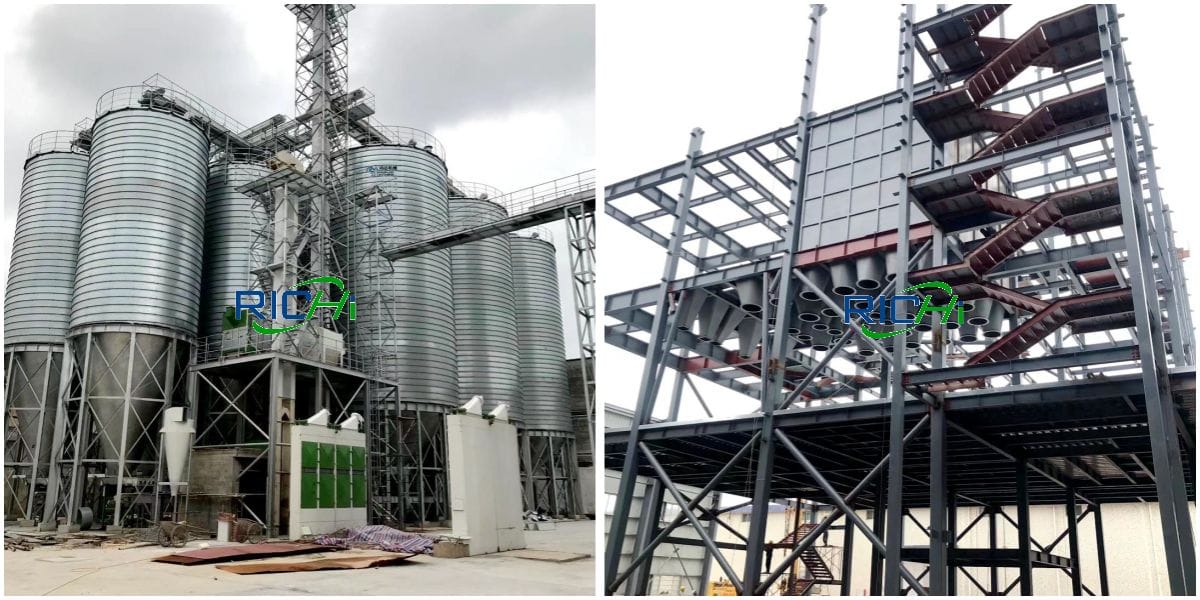
Its main process is briefly described as follows:
(1) Raw material receiving, cleaning and crushing section
The main raw materials required for production are transported into the 18 t/h shrimp and fish feed factory area by car, weighed and inspected by the truck scale, and then transported to the raw material workshop and raw material silo for storage through the receiving equipment.
After the auxiliary materials required for production are weighed and inspected by the truck scale, they are directly sent to the raw material workshop for storage.
Raw materials that need to be crushed enter the production workshop through the conveying equipment, and then enter the bin to be crushed after being cleaned to remove impurities and permanent magnet cylinders to remove ferrous impurities.
After the raw materials in the crushing bin are crushed to the required particle size by the pulverizer, they are distributed to the raw material bin for storage through the conveying equipment.
The raw materials that do not need to be crushed enter the production workshop through the conveying equipment, and after the impurities are removed by the primary cleaning screen and the ferrous impurities are removed by the permanent magnet cylinder, they are sent to different raw material bins by the distributor for storage.
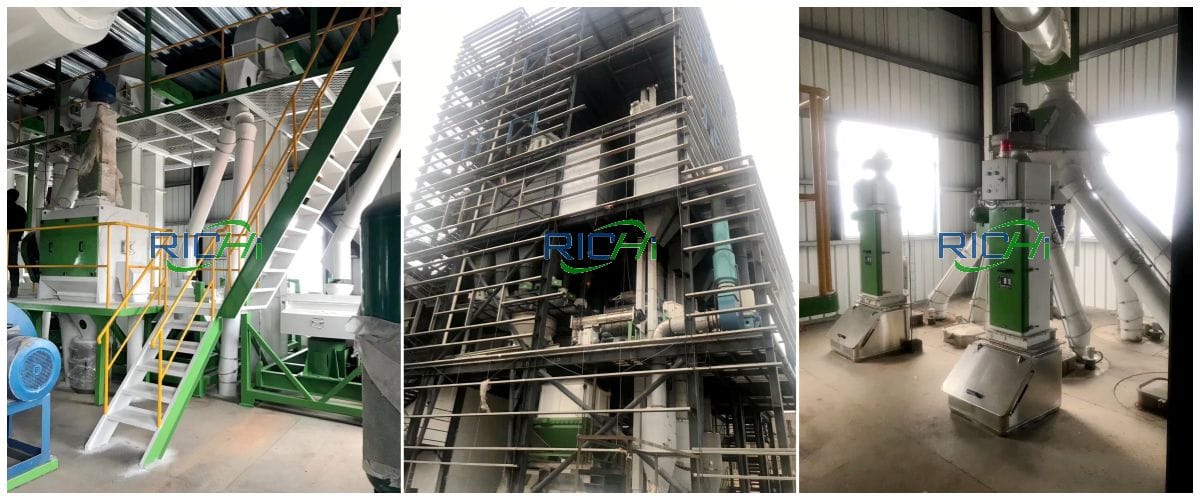
(2) Ingredients and mixing section
According to the requirements of the formula, various raw materials participating in the batching are sequentially entered into the mixer through the batching scale controlled by the computer.
The batching process uses two batching scales, one large and one small, to ensure the accuracy of batching and shorten the batching time. Some raw materials such as additives and vitamins with less dosage are manually weighed and put into the mixer manually.
Various raw materials are mixed in the feed mixer, and the mixed powder enters the puffing section for making extruded feed, and enters the pelleting section for making feed that does not need to be extruded.
(3) Granulation and screening
The 18 t/h shrimp and fish feed factory project uses thermal granulation to granulate. The granulation process uses steam modulation. The project uses a 15t/h biomass boiler to provide the steam required for granulation.
The material from the mixing section is tempered through the conditioner, then indirectly heated to 85C with high-temperature steam for gelatinization, and then enters the shrimp feed pellet machine for granulation. The finished feed enters the impeller cooler for draft cooling.
Cooling is a physical process that reduces the moisture inside and outside the feed to the qualified moisture range. The cooled pellet feed enters the plane rotary grading sieve through the elevator, and the fine pellets or powder enter the granulation process again, and the coarse pellets enter the granulation process after being crushed.
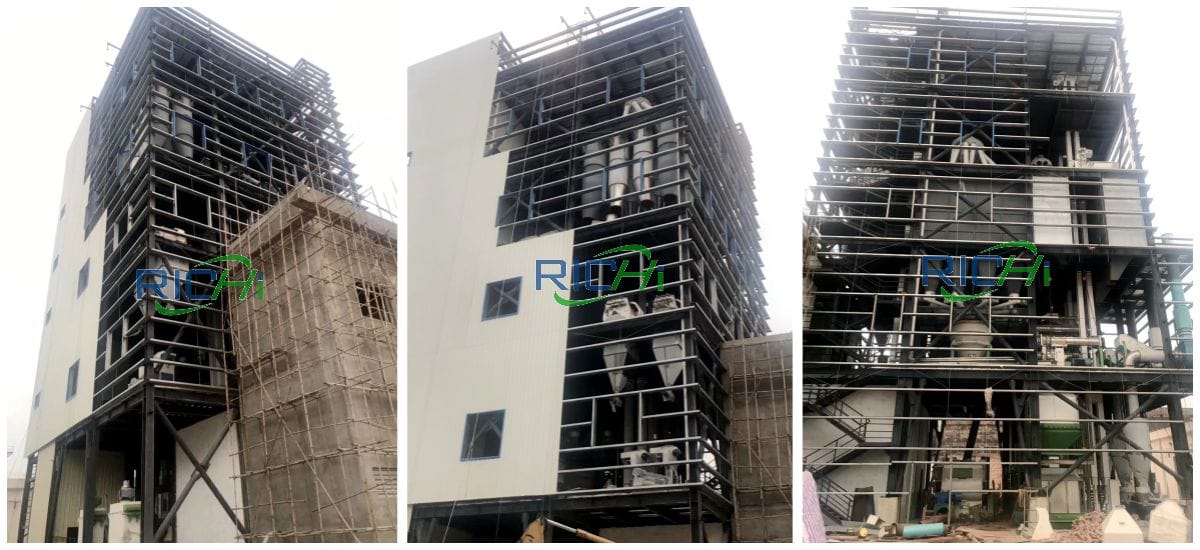
(4) Extrusion & drying & spraying
The prepared, mixed and finely powdered materials first enter the puffing bin to be processed. When working, the feeder evenly and continuously feeds the material in the puffing bin into the dual-shaft differential speed conditioner for conditioning.
When the material enters the conditioner, it adds uniform, continuous and metered steam, water and other liquid additions. This is a critical link in the 18 t/h shrimp and fish feed factory.
After a certain conditioning time in the conditioner, the material enters the feeding section of the extrusion assembly to start the extrusion operation. The material is input from the feeding section, and the main function of the feeding section is to transport the material to the kneading area.
In the kneading section, the material undergoes strong stirring, mixing, shearing, etc., and the material is gradually matured or melted; entering the final aging section, the pressure and temperature are further increased, the material is further matured, and the starch is further processed.
Gelatinization, fat and protein denaturation, tissue homogenization and formation of non-crystalline texture, and the final material is extruded and cut into shape through the discharge assembly.
The extruded pellet enters the fish feed dryer through the air transportation system, and the steam-heated air is used as the drying medium. And the cross flow drying method is adopted to make the material and hot air realize moisture and heat exchange in the aqua feed dryer, so as to remove excess moisture in the material and make it to achieve the desired moisture requirements of the finished product.
Finally, through the spraying machine, the surface of the pellet feed is sprayed with liquids such as oil, vitamins, antioxidants, amino acids, etc.
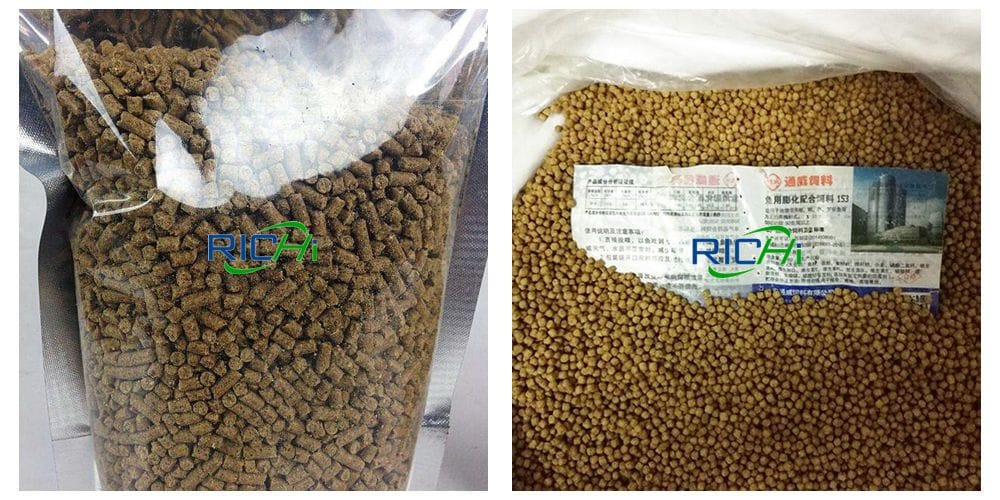
(5) Measuring and packaging of finished products
Finished product packaging is the last process of 18 t/h shrimp and fish feed factory . There is a packing scale installed under the finished product warehouse, and the packing scale automatically quantitatively packs according to the amount set by the debugging, and then the bag mouth is sewed by the bag sewing machine to complete the production process.
Main equipment for 18 t/h shrimp and fish feed factory
(1) Raw material receiving system
Feeding port and fence, pulse dust collector TBLF24, self-cleaning bucket elevator TDTG40/23, cylinder primary cleaning screen SCY80, scraper conveyor TGSS25, rotary distributor 250-4, permanent magnetic cylinder TCXT25, rotary distributor 250-8, feeding port and fence, powder cleaning screen, permanent magnet cylinder TCXT25, rotary distributor 250-8, etc.;
(2) Primary coarse crushing system
Crushing bin 12 cubic meters per piece, buffer bucket, feeder, wide-type fine pulverizer, pulse dust collector, fan, silencer, settling chamber, material sealing auger TLSS32, self-cleaning bucket elevator TDTG40/23, fan, Pulse dust collector TBLF6, rotary distributor 250-10, etc.;
(3) Sub-batching system
Batching bin 12 cubic meters/piece, batching scale 1500KG/P, pulse dust removal Device, fan, feeding port, double-shaft paddle mixer 2000KG/P, mixing buffer bucket, scraper conveyor TGSS32, self-cleaning bucket elevator TDTG50/28, permanent magnet cylinder TCXT30, etc.;
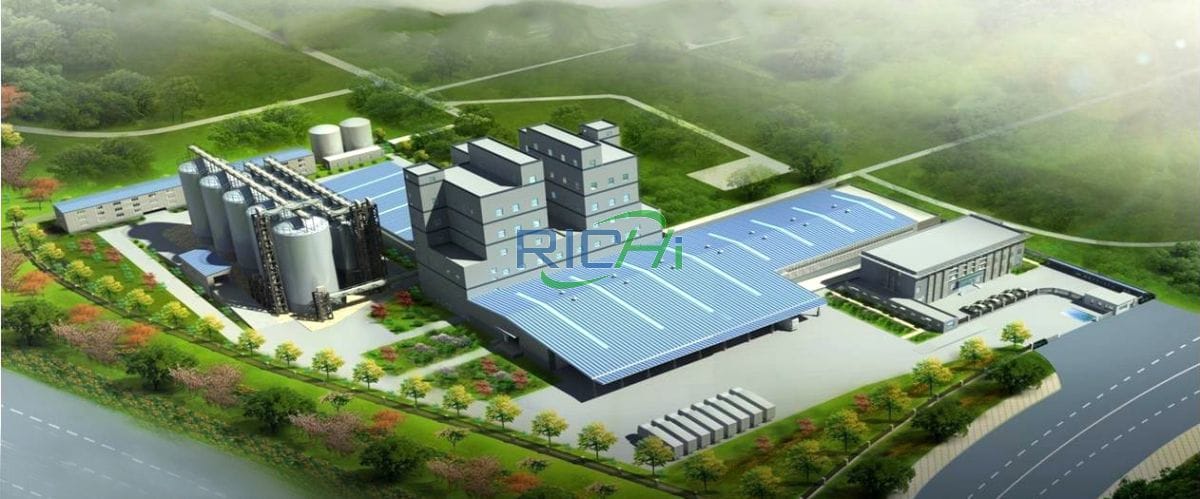
(4) Coarse crushing system
Crushing bin 5 cubic meters/piece, buffer bucket, feeder, wide-type fine pulverizer, pulse dust collector, permanent magnet cylinder TCXT30, pulse dust collector, fan, permanent magnet Barrel TCXT30, etc.
(5) Superfine pulverization system
Superfine crushing bin 12 cubic meters per piece, air cannon arch breaking device, superfine pulverizer SWFL150B, anti-rotation unloader, pulse dust collector, high-pressure fan, silencer, high square screen, conveying auger TLSS20, etc.;
(6) Secondary ingredient mixing system
Secondary batching bin 12m³/piece, batching scale 1000KG/P, feeding port, double-shaft paddle mixer 1000KG/P, mixing buffer bucket, scraper conveyor TGSS25, permanent magnet cylinder TCXT25, buffer bucket 4m3/piece, square screen SFSC110*170, conveying auger TLSS20, etc.;
(7) Fish feed extruding and drying system
15m³ to be extruded warehouse, dual-axis differential speed conditioner, conditioner, aquatic extruder, drying machine, air network system, muffler, fan, cyclone dust collector 1800, plane rotary grading screen, unqualified silo, etc.;
(8) Extruded fish feed spraying and cooling system
Cooler 28X28, wind network system, muffler, fan 4-72-8C, cyclone dust collector 50-Φ1800, warehouse to be sprayed, vacuum spraying machine, vacuum spraying machine refueling system, self-cleaning bucket elevator TDTG50/28, etc.;
(9) Expanded fish feed packaging system
Finished product warehouse, finished product drawer screen 180, buffer bucket, packing scale PSC50, belt sewing bag conveyor, fan, pulse dust collector, etc.;
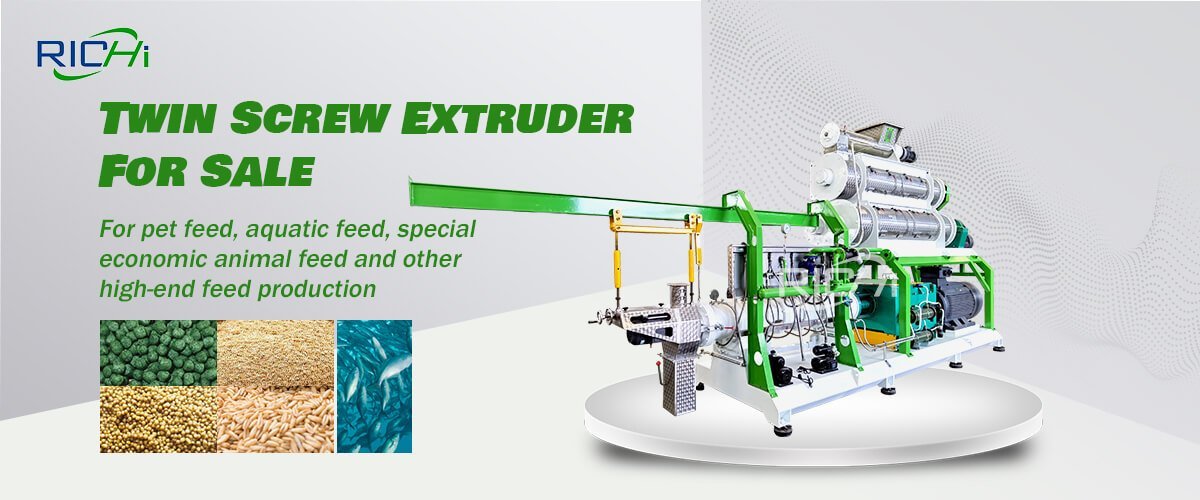
(10) Shrimp pellet cooling system
Granulation bin, frequency conversion stainless steel feeder WLL250, dual-axis differential speed conditioner, quality preserver, conditioner, shrimp feed pellet machine, flap type post-curer SWDB19×19, wind network system, cyclone dust collector 50-1500, pellet cooler, etc.;
(11) shrimp feed Pellets packaging section
Finished product warehouse, drawer screen, pulse dust collector TBLY18, fan, buffer warehouse, packing scale PSC50, belt sewing bag conveyor, etc.;
(12) Shrimp Feed crumbling and packing system
Permanent magnet cylinder TCXT20, crumbler (for shrimp feed) PCS22*160, crusher (for shrimp feed) PCS22*160, double box high side Sieve FSFG2*100, finished product warehouse, square sieve FSFG1*100, pulse dust collector, fan, buffer bucket 2 cubic meters, automatic packing scale, belt sewing bag conveyor, etc.;
(13) Powder recovery section
Powder return bin 3 cubic meters, conveying auger TLSS20, return machine material feeding port, self-cleaning bucket elevator TDTG40/23, scraper conveyor TGSS20, garbage dump type 20, etc.;
(14) Auxiliary section
Fish melt adding liquid storage tank machine weighing device, fish melting slurry weighing device, fish oil adding liquid storage tank machine weighing device, soybean oil adding liquid storage tank machine weighing device, water adding liquid storage tank machine weighing device, scale water adding system, air compressor SA-75A, air tank filter, ATC three-stage filter, air dryer, etc.;
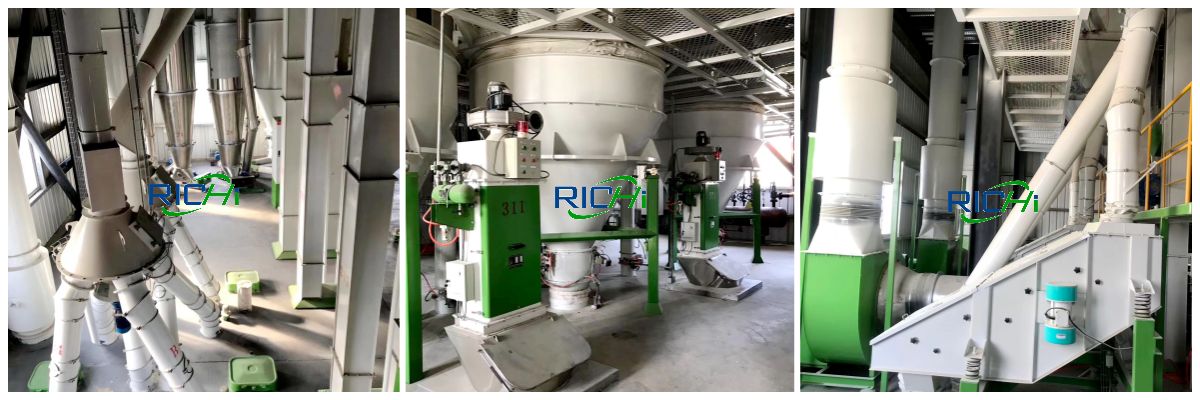
(15) Fermentation raw material production line
Feeding port 1.2×1.5, dust removal system (pulse bag filter) TBMCa.12, bucket elevator DTG36/23, smaterial level device (rotary resistance), raw material warehouse 6m³& 4m³, batching screw conveyor TLSS 20 /TLSS 12, stirring mixer SLHJ3.0, strain storage tank CG5.0, fermentation tank 20·3.5·2.5m, forklift, tube bundle dryer GZG600, counterflow cooler SKLN21X21, spray tower, finished product warehouse 6m³/bin, automatic packing flat 50P-1, sewing machine BL.7, etc.;
(16) Fermented feed production line
Bacteria batching and metering system 5.5KW, bacteria solution adding system 8.8KW, granular material batching and mixing system 22.7KW, packaging metering system, electrical control system.
General layout
The 18 t/h shrimp and fish feed factory workshop is adjacent to the west side of the existing aquatic product workshop, which is convenient to rely on the existing aquatic product workshop odor treatment facilities and the raw material storage area and finished product storage area of the existing aquatic product line.
Each production workshop arranges the aqua feed processing equipment that is closely related to each other in production according to the function of use.
The production links in the workshop are closely connected, which is conducive to energy saving and consumption reduction, and the loss of construction materials is conducive to clean production and can meet the 18 t/h shrimp and fish feed factory production process requirements.
The production equipment is arranged on the side of the factory building away from the surrounding enterprises and sensitive points, which is conducive to reducing the noise at the factory boundary and reducing the impact on the external acoustic environment.
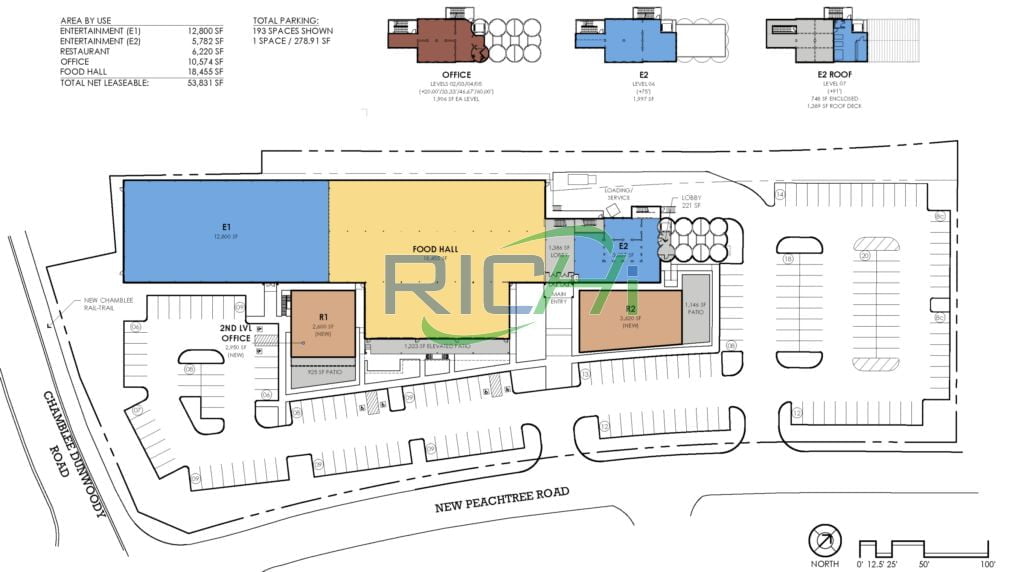
The connection between equipment layout and technological process is basically reasonable, and the building structure is basically perfect, which can meet the requirements of production technology. All processes in the production workshop are arranged reasonably, and sufficient space is reserved to ensure the smooth transportation of various materials.
Public facilities
After the expansion and operation of this 18 t/h shrimp and fish feed factory project, the main energy consumed will be water, electricity and boiler steam. Water, electricity, and boiler steam all rely on the company’s existing public and auxiliary projects.
① Power supply: provided by the local power supply bureau. The company’s existing power supply facilities can guarantee the electricity demand for project construction and commissioning, and there will be no power outages.
②Water supply: The water for the expansion aqua feed mill project is supplied by the local tap water pipe network, mainly domestic water, and the total water consumption of the project is about 1080 m3/a.
③Drainage: The drainage of the plant area adopts the separate system of rainwater and sewage. The discharged wastewater is mainly domestic sewage, which is used for irrigation of the surrounding dry land after being treated by septic tanks; rainwater enters the rainwater pipes set up on the secondary road through the rainwater drainage ditch set up in the factory.
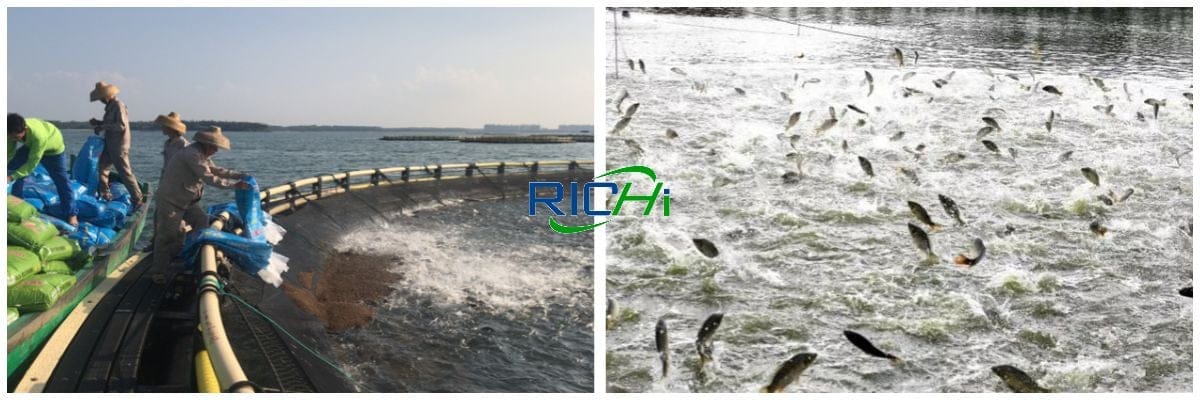
④ Boiler steam: The boiler steam required for the expansion project is provided by the existing 15t/h biomass-fired steam boiler in the plant area.
According to the daily operation of the owner, the gas supply capacity of the existing boilers in the plant area can meet the boiler steam supply of the whole plant after the expansion project is put into operation. gas requirements.
(After the 18 t/h shrimp and fish feed factory project is implemented, the maximum daily steam volume is 187.4t, the maximum hourly steam consumption is 11.7t. And the gas supply capacity of the existing 15t/h biomass-fired steam boiler in the plant area can meet the boiler steam supply requirements of the whole plant after the expansion.)