Background of the 500kg/h fish food processing line
The project client was originally engaged in small-scale poultry feed processing and sales, and sales of agricultural and sideline products. With the intensification of competition in the poultry feed processing industry, the small feed line operated by the customer is no longer profitable.
Therefore, based on the current prospect of aquatic feed, the customer focuses on aquaculture, builds a new small aquaculture farm, and invests in a new small fish feed production line, including two product types of floating fish feed and sinking fish feed, for use in his own fish pond, and the original poultry feed equipment was dismantled at the same time.
Since the customer already has a feed workshop, the project took only two weeks from design to installation and was put into operation in January 2016.
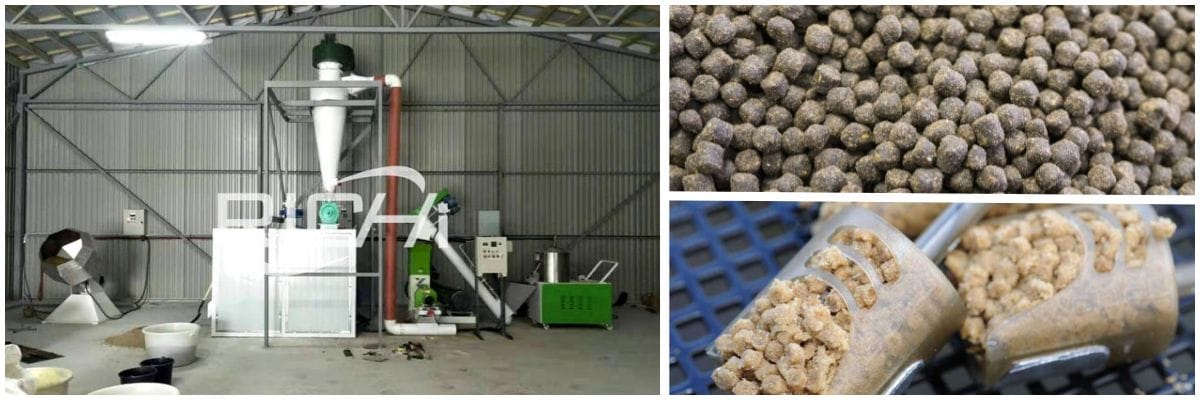
Since it is the first time to enter the aquatic feed processing industry, the customer’s initial investment is not large, only 500kg/h. However, it is worth mentioning that the customer did not let us design this small production line into a simple equipment configuration, and reserved the possibility of expansion.
Because in terms of feed processing, the customer has good raw material channels, especially the prospect of aquatic feed processing is very optimistic, so if the business situation is good, the customer plans to expand production in the future, and also plans to register a brand to carry out feed processing and sales business, supply surrounding aquaculture needs.
However, because it is the first time to enter the aquatic feed processing industry, the initial investment of the customer is not large, only 500kg/h. It is worth mentioning that the customer did not let us design this small production line into a simple equipment configuration, and reserved the possibility of expansion.
- 500KG/H fish food processing line design provided by RICHI for customers: using pelleting process and extruding process respectively to produce ordinary sinking fish feed and grass carp extruded feed;
- Total cost of the project: USD 100,000 (including equipment, workshop lease, civil engineering, etc.).
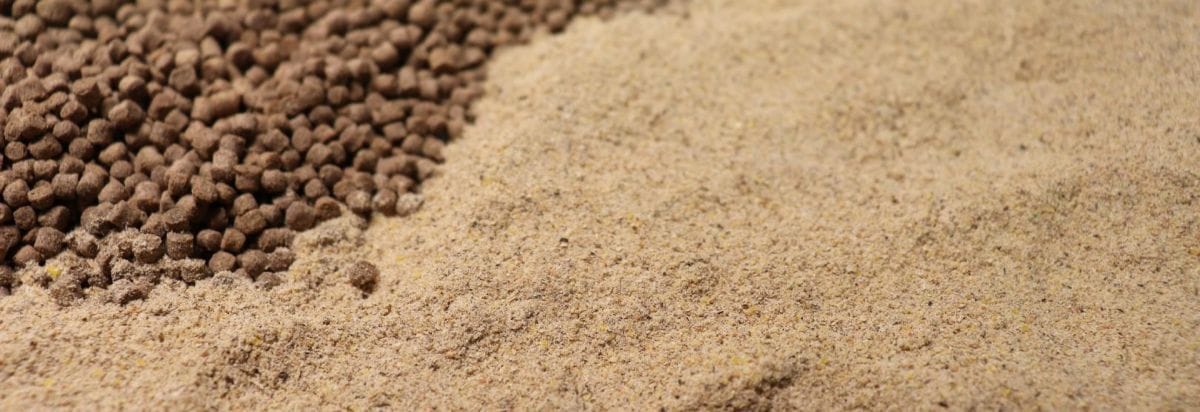
Tips:
If you also want to invest in a new fish feed pellet production line with the same output, you can consider the budget, local market conditions, raw materials and formula, etc. For the initial investment, you can invest in a very simple feed production line. The field has long-term development, and it is also possible to invest in production lines and equipment with greater output.
We can customize according to the actual needs of customers. Regardless of the size of your output, regardless of the budget, as long as it is within our technical scope, Richi Machinery will definitely provide you with satisfactory project design, equipment quality and after-sales service. (Hot products: sinking fish feed machine)
Construction content and scale
The workshop leased by the customer covers an area of about 2500m², with an annual output of 1000 tons of mixed fish feed and 200 tons of grass carp extruded compound feed. The project employs 10 people, working 300 days a year, 8 hours a day, without providing board and lodging.
Product | Production (t/a) |
---|---|
Mixed feed for mixed fish species | 1000 |
Grass carp extruded compound feed | 200 |
Main construction content
The 500kg/h fish food processing line project is mainly composed of main body engineering, storage and transportation engineering, auxiliary engineering, public engineering, environmental protection engineering, etc.
- Production workshop: 771.9m²
- Raw material warehouse: 829.56m², storing all raw materials
- Finished product warehouse: 771.9m², storing products
- Office area: 500㎡
- Boiler room: 300m²
- Power supply project: the annual power consumption is 105 degrees, provided by the power supply system of the park
- Water supply project: tap water pipe network
- Steam supply project: 2t/h steam boiler, gas consumption 98,000 m³/a
Main raw and auxiliary materials
All raw materials for this 500kg/h fish food processing line project are stored in the raw material warehouse in the form of bags.
Name | Annual consumption (t/a) | Storage (t) |
---|---|---|
Soybean Meal | 204.2 | 10 |
Rape meal | 171 | 8 |
Cotton meal | 151 | 7 |
Rice Bran | 153 | 8 |
Wheat middlings | 53 | 2.5 |
Bran | 22 | 1 |
Corn | 70 | 3.5 |
Flour | 49 | 2.5 |
Calcium carbonate | 11 | 0.5 |
Soybean oil | 6 | 0.3 |
Vitamins | 26 | 1.3 |
Premix | 24 | 1.2 |
Fishmeal | 12 | 0.6 |
Shrimp powder | 24 | 1.2 |
Main equipment for 500 kg/h fish food processing line
(1) Sinking fish mixed feed production equipment
Device name | Specification model | QTY |
---|---|---|
Bucket elevator | TDTG36/23 | 1 |
Automatic batching system | TH-PLG | 1 |
Batching warehouse | 6m³ | 1 |
Automatic batching scale | PCW2000 | 1 |
Twin Shaft Paddle Mixer | SSHJ2 | 1 |
Fish feed pellet making machine | SZLH420 | 1 |
Automatic packing scale | DCS-50 | 1 |
Pulse dust collector | TBLM12*1M | 2 |
(2) Extruded grass carp food processing line
Device name | Specification model | QTY |
---|---|---|
Bucket elevator | TDTG36/23 | 1 |
Batching warehouse | 6m³ | 1 |
Automatic batching scale | PCW2000 | 1 |
Preliminary cleaning of pellets | SC63Y | 1 |
Horizontal mixer | WHHJ112 | 1 |
Superfine Pulverizer | SWF-130 | 1 |
Batching scale | 1000KG | 1 |
Fish feed extruder | EXT200S | 1 |
Shaker | SFJ80*140 | 1 |
Counterflow cooler | 6.4m³ | 1 |
Pulse dust collector | TBLM9*1.2 | 2 |
Boiler | 2T/h | 1 |
Reverse osmosis pure water equipment | 2t/h | 1 |
Production process of 500 kg/h fish food processing line
(1) Production process design of mixed feed for mixed fish species:
The feed is made of corn, rapeseed meal, green cake and many other raw and auxiliary materials, combined with vitamins, premix, calcium carbonate, rice bran and other ingredients to make granular feed. This project adopts the process of crushing first and then batching. (Related solution: 6t/h fish feed mill plant)
The crushing (corn, rapeseed meal, green cake, etc.) that needs to be crushed (corn, rapeseed meal, green cake, etc.) will be crushed through a feed grinder, and then enter the batching bin. And other raw and auxiliary materials that do not need to be crushed (soybean meal, vitamins, premix, Calcium carbonate, rice bran, etc.) are transferred to the feed mixer for batch mixing or continuous mixing.
After the pelleting process, sinking fish feed products are produced. Its main process is briefly described as follows:
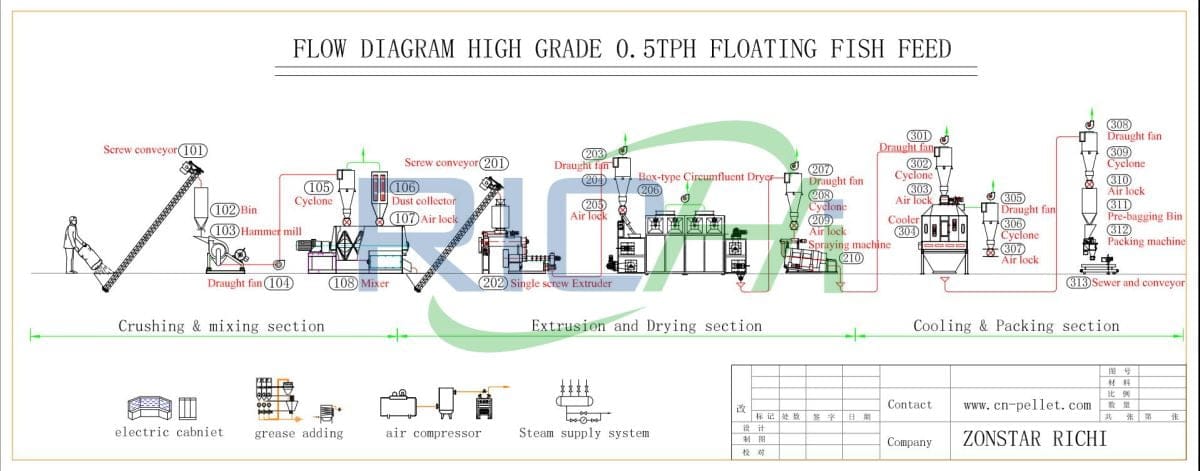
① Raw material receiving, cleaning and crushing section
- After the main raw materials required for production are transported into the factory area by car, they are weighed and inspected by the truck scale, and then they are cleaned by receiving equipment, magnetically separated, and then transported to the bulk warehouse for storage. The raw materials of the project are all in bags, and the unpacking and feeding place is set up separately.
- The auxiliary raw materials required for production are weighed and inspected by the truck scale, and then sent directly to the auxiliary material warehouse for storage.
- The raw materials that need to be crushed enter the production workshop through the conveying equipment, and enter the bin to be crushed after the initial cleaning to remove impurities and the permanent magnetic bucket to remove iron impurities. After the raw materials in the crushing bin are crushed to a qualified particle size by the fish feed pulverizer, they are distributed to the batching bin by the conveying equipment for storage.
- The raw materials that do not need to be crushed enter the 500kg/h fish food processing line workshop through the conveying equipment. After the impurities are removed by the initial cleaning screen and the iron impurities are removed by the magnetic separator, the impurities are mixed into the domestic waste for treatment, and sent to different batching bins by the distributor for storage.
②Batching and mixing section
According to the requirements of the formula, various raw materials participating in the batching are sequentially entered into the mixer through the batching scale controlled by the computer.
The batching process uses two batching scales, one large and one small, to ensure the accuracy of batching and shorten the batching time. Some raw materials such as premixes and vitamins with less dosage are manually weighed and then put into the fish feed mixer manually.
All kinds of raw materials are mixed in the mixer, and the mixing cycle is 2 minutes; the finished powder after mixing can be granulated according to the needs, and can also be directly packed into the finished product warehouse for storage or loaded into the bulk finished product warehouse with a bulk truck for delivery. (Related solution: 5t/h aqua feed plant)
③ Granulation section
Raw materials that need to be granulated are conditioned by a conditioner, so that the temperature of the material reaches 80-85°C, and the moisture reaches about 15%, and then granulated materials of different particle sizes are made by a fish pellet machine.

After cooling and crushing, the unqualified materials are re-granulated after being screened by a grading sieve, and the qualified granule products are packed into the finished product warehouse for storage or loaded into the bulk finished product warehouse with bulk trucks for delivery. The heat of the granulation section comes from the steam boiler, and the fuel is natural gas.
The 2t/h steam boiler of this project is fueled by natural gas, with an annual consumption of 98,000 m³/a, 300 days of work per year, and a working time of 8h/d.
(2) Process design of grass carp extruded compound feed
In the extrusion and puffing process of 500kg/h fish food processing line, the environment where the material is in the puffing cavity is high humidity, high heat, and high pressure. Under this condition, the material is actually going through a cooking process.
The wet and soft granules after puffing (moisture content 25%~28%) are pneumatically conveyed into the horizontal dryer, and the hot air heated by the steam heat exchanger makes the material in a state of a state on the entire screen surface when it penetrates the material. The semi-suspension state can not only effectively guarantee the dehydration and drying effect, but also minimize the damage to the material. The moisture of the dried particles is about 8~12%.
In order to meet the energy demand of fish and reduce the loss of heat-sensitive substances during processing, oil is sprayed outside between drying and cooling in this process. The optimum working temperature of the external spraying process is around 80°C, so the sprayed particles need to be further cooled down to the ambient temperature after extrusion.
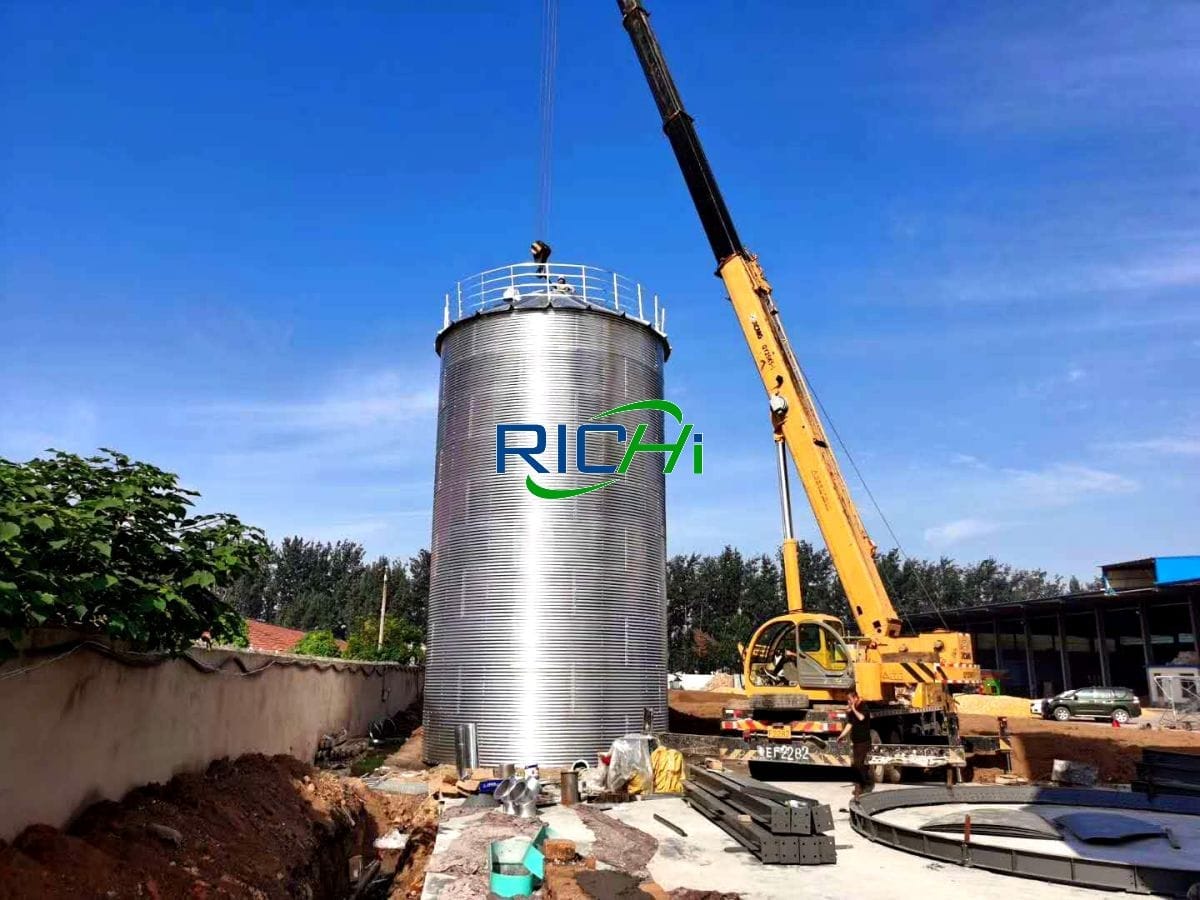
The basic principle of extruded feed processing: the material enters the extruder machine for fish feed, and the screw and spiral drive the material to form an axial flow. At the same time, due to the mechanical friction between the screw and the material, the material and the barrel, and the inside of the material, the material is strongly squeezed, stirred, and sheared, and as a result, the material is further physicalized and homogenized.
As the pressure gradually increases, the temperature rises accordingly. Under the conditions of high temperature, high pressure, and high shear, the physical properties of the material change, from powder to paste, starch gelatinization, protein denaturation, and fiber degradation.
Thinning, pathogenic bacteria are killed, hygiene indicators are improved, and toxic components are inactivated. When the pasty material is ejected from the die hole, under the strong pressure difference, the material is puffed, dehydrated, and cooled. The puffed product has a loose, porous, crisp structure, and has good palatability and flavor. (Related product: floating fish feed machine)
Public works
- Water supply: This 500kg/h fish food processing line project is supplied by tap water, the annual working time is 300d, the water consumption is 50L/d per person, the project labor quota is 10 people, no board and lodging is provided, the domestic water consumption is 150t/a, the pollution production coefficient is 80%, and the living Sewage discharge is 120t/a.
- Boiler: 2t/h steam boiler, the annual steam volume is 1380t (4.6t/d), and the supplementary water consumption is 3.0t/d (900t/a).
- Drainage: The factory area adopts a rainwater and sewage diversion collection system, and the rainwater is discharged into the rainwater pipe network of the park through the rainwater pipe network.
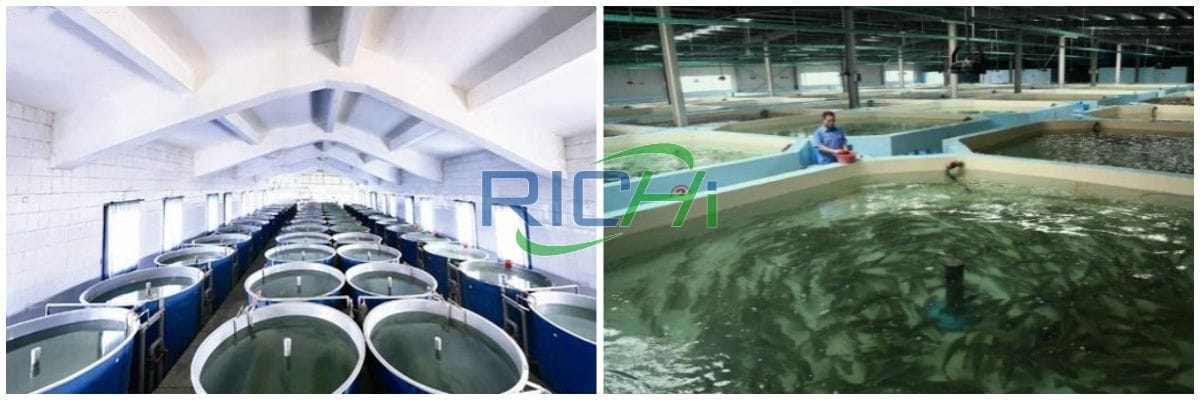
Plant layout
According to the principle of “reasonable zoning, smooth process, short logistics; emphasizing environmental protection and safety” of the factory area, combined with the land use conditions and production technology of the site, and comprehensively considering the requirements of environmental protection, the overall layout of the factory area was arranged. (Maybe you are interested in: aqua feed production projects)
The 500kg/h fish food processing line project is divided into two different functional areas of the production plant, mainly the warehouse and the production area. According to the production process of the project, workshops are arranged in the factory building to make the links of the production process more closely connected and easy to manage. And the warehouse and production area are separated from each other.