Background of 4-5 t/h feed pellet production line for fish
The customer company covers an area of about 20392m² and a construction area of about 3733.38m². The 4-5t/h fish feed pellet production line project is mainly engaged in aqua feed production. Due to market expansion and development needs, the customer expanded the existing buildings in the factory area.
This project increased the supporting equipment on the basis of making full use of the original equipment, and adjust the working hours from 8h/d to 24h/d. The production capacity will be expanded by means of expansion. After the expansion, the feed production capacity will increase from 5000t/a to 35000t/a.
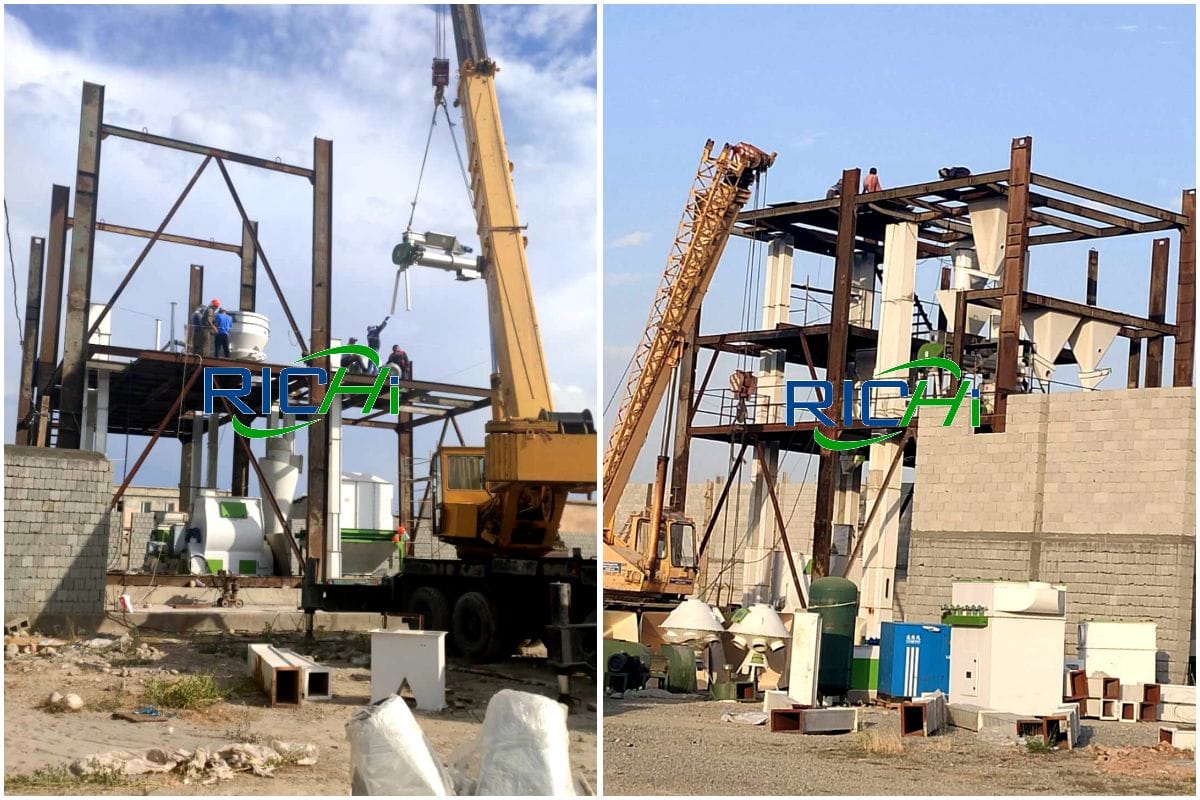
The feed production capacity of the project depends on the number of fish pellet machine and the production time. After the expansion, the fish feed pelletizer will be increased from 1 to 3, and the production capacity per unit time will be increased from 1.5~5t/h to 4.5~15t/h; after the expansion, the production time will be 8h /d increased to 24h/d.
The heating capacity of the existing boiler is 4t/h, the feed steam consumption is 250~350kg/t, and the supporting feed production capacity of the boiler is 11.5~16t/h, that is, the existing 4t/h boiler can meet the expansion of 3 sets pellet machine heat demand. (Related solution: 3-4T/H floating fish feed mill)
Therefore, this expansion only expands the number of production equipment and working hours, and the existing 4t/h boiler is used. After expansion, the production capacity will increase from 5000t/a to 35000t/a. Before and after the expansion of this 4-5t/h feed pellet production line project, there is a production line, and the equipment added in the expansion is located in the production line. After the expansion, the production capacity of the production line increases from 2.5t/h to 5t/h.
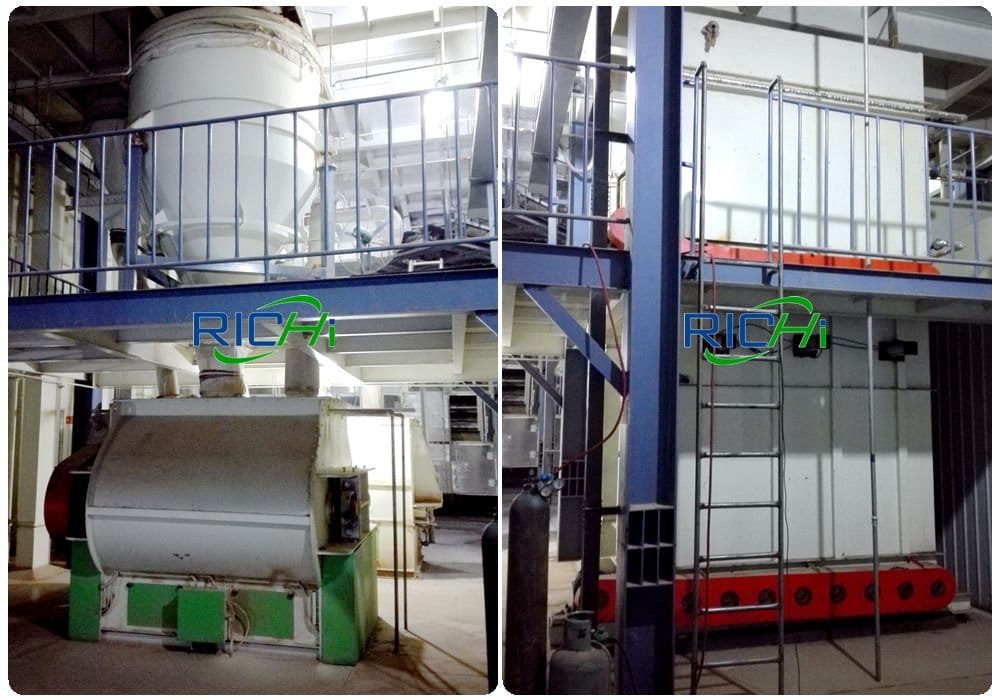
- Customer type: Owns its own comprehensive compound feed factory. Due to the good operating conditions, the customer intends to expand production, because the competition of feed enterprises is the competition of cost and scale. Only by increasing the scale of the enterprise and optimizing the industrial structure can the enterprise compete more easily to win.
- Expansion project investment: 1.6-1.7 million US dollars (including equipment and all other costs)
- Reminder: The client of this project is quite special, because under the current market background of vigorously promoting extruded feed, this client has blazed its own path of specialization by processing and selling sinking fish feed. What deserves attention here is actually the quality of fish feed pellets and the management and sales model of the client company.
Overview of 4-5 t/h feed pellet production line
The project covers an area of 20,392m² before and after expansion, and a construction area of 3,733.38m². After the expansion, due to the update of equipment and the automatic operation of the same type of equipment, through the adjustment of personnel positions, there is no need to increase the number of employees before and after the expansion, and the 50 people remain unchanged.
After the expansion, the working system is 300 working days per year, 24 hours a day, three days shift system. The project has a dining hall and dormitories.
Name | Building area |
---|---|
Production hall, 1st floor (with 5-story equipment tower) | 1260m² |
Warehouse, 1F | Finished product warehouse is 1296m², raw material warehouse is 1440m² |
Office Building, 2F | 432.65m² |
Dormitory, 3F | 564.73m² |
Green spaces, roads | 4800m² /11778.62m² |
4-5T/H feed pellet production line process design
According to the customer’s fish food plant, process requirements, raw materials, investment budget and other factors, RICHI’s custom-designed process flow for customers is as follows:
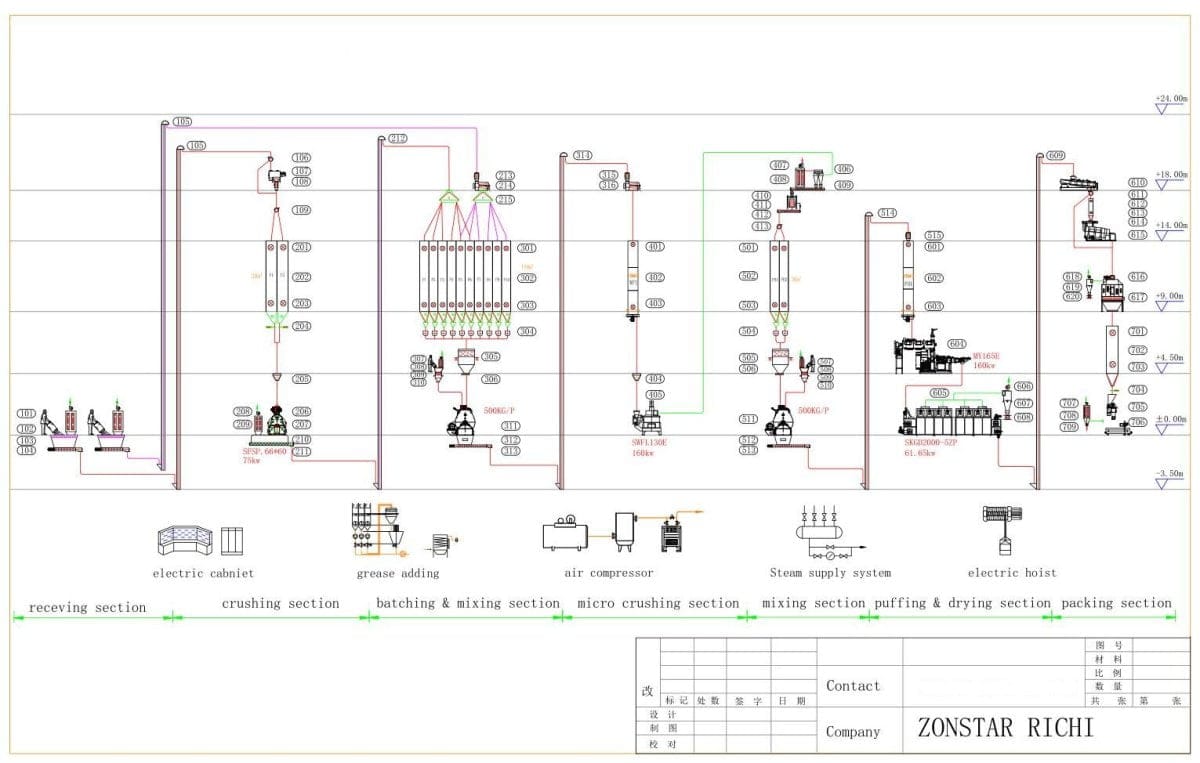
- Raw material input: According to the needs of the production plan, various raw materials are arranged and sent to the production workshop to be crushed (granular raw materials) and batching bin (powdered raw materials).
- Coarse crushing: The granular raw materials are coarsely crushed by a coarse powder machine, and the crushing particle size is less than 1.5mm. This process is attached to a bag filter to recover dust.
- Batching mixing: The powder in each batching bin is weighed by the batching scale according to the formula ratio of the product, and then enters the mixer. After mixing evenly, it is lifted into the micro-grinding bin.
- Micro-grinding: The coarsely crushed raw materials are first mixed and then sent to a micro-powder machine for fine crushing. This process is equipped with a bag filter to recover dust. (Hot products: floating fish feed machine)
- Secondary ingredient mixing: the finely crushed raw materials, premixed materials and other small amount of raw materials that need to be added such as oil, water, etc., according to the formula ratio of the product, the raw materials in each batching bin are weighed by the batching scale and then enter the fish food mixer, and distribute it into the corresponding bin to be granulated through the distributor after lifting. Powdered products that do not need to be granulated are lifted into the finished product bulk warehouse, weighed by quantitative packaging scales, and packed into storage.
- Granulation: The raw materials in the granulation bin enter the conditioner of the fish pellet machine at the granulation speed under the control of the pneumatic gate, and the raw materials in the conditioner of the fish feed pellet mill are heated and tempered by steam (130°C steam heating, heating time It takes about 2 minutes to soften, condition and sterilize) and then make into granules.
- Mature: After the pelleted feed is heated by steam, the temperature is raised to 90-100℃, and the material is matured. This 4-5t/h feed pellet production line process is equipped with a cyclone suction facility, and the dust and odor are collected and sent to the dust removal and odor removal equipment for treatment.
- Drying and cooling: After the formed product is cured, it is sent to the dryer for drying treatment. (If the moisture content of the product is not high, no drying is required.) The dryer uses steam as the medium, and the air passes through the heat exchanger to increase the temperature. The high-temperature and dry air takes away the moisture in the product.
During the drying process, adjust the air temperature and conveying speed in the dryer according to the moisture content and particle size of the product. The temperature of the dryer should be controlled below 100°C as much as possible, and the residence time of the product in the dryer should be controlled within 30 minutes as much as possible.
Coordinate with those who try to control the moisture content of the product within the range of 9.0% to 10.5%. After the steam passes through the heat exchanger, it is converted into condensed water and is recycled to the boiler for reheating to produce steam. This process is equipped with a cyclone exhaust fan, and the dust and odor are collected and sent to the dust removal and odor removal equipment for treatment. The dried product is cooled to a state not higher than 5℃ above normal temperature, and enters the packaging process after grading. - Finished product packaging and warehousing for sale: Feed products are weighed by quantitative packaging scales, packed and put into storage, waiting to be sold.
Consumption of main raw and auxiliary materials
The following only lists the raw materials and annual consumption required for new 4-5t/h feed pellet production line for fish.
Ingredient name | Annual consumption (t/a) |
---|---|
Flour | 6600 |
Corn | 5400 |
Soybean meal | 6000 |
Rape meal | 5100 |
Peanut bran | 3750 |
Fish meal | 2700 |
Fat (soybean oil) | 300 |
Premix | 150 |
Main equipment for 4-5 t/h feed pellet production line
The following lists only the equipment required for the new fish feed processing line.
Device name | QTY |
---|---|
Fish feed hammer mill | 2 |
Fish feed mixer | 2 |
Micro pulverizer | 4 |
Fish feed pellet machine | 2 |
Fish feed dryer | 2 |
Fish feed cooler | 3 |
Quantitative packaging scale | 1 |
Raw material pre-mixer | 2 |
Greasing equipment | 1 |
High square sieve | 4 |
Rotary classifier | 4 |
Bucket elevator | 10 |
Scraper conveyor | 2 |
Batching warehouse group | 2 |
Grease storage tank | 4 |
Biomass boiler parameters:
- Rated evaporation capacity: 4t/h
- Rated working pressure: 1.25MPa
- Rated steam temperature: 194℃
- Feed water temperature: 20℃
- Fuel type: biomass pellets
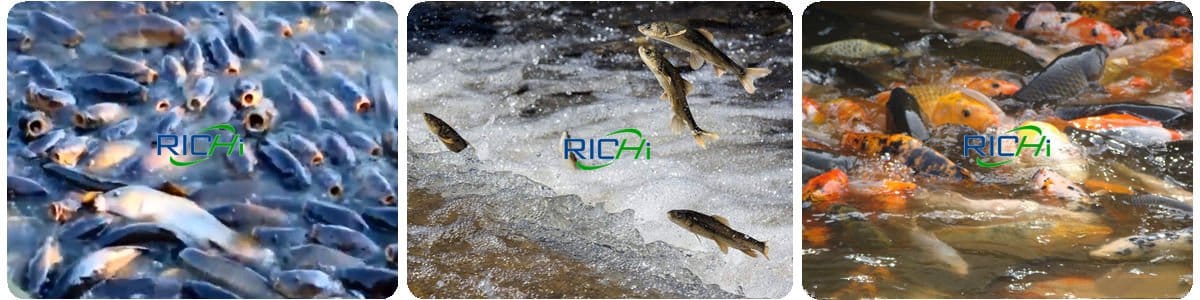
Public works
After the expansion, the steam heating capacity of the boiler remains unchanged at 4t/h, the heating time is increased from 8h/d to 24h/d, and the daily steam supply is three times that of before the expansion.
In addition, the production process of 4-5t/h feed pellet production line is optimized. In the original production process, 80% of the steam consumed by steam condensation and heat exchange when the product is dried is optimized. After optimization and improvement, the drying equipment and the internal circulation fan will recycle the hot air. (Related solution: 6t/h aquatic feed mill)
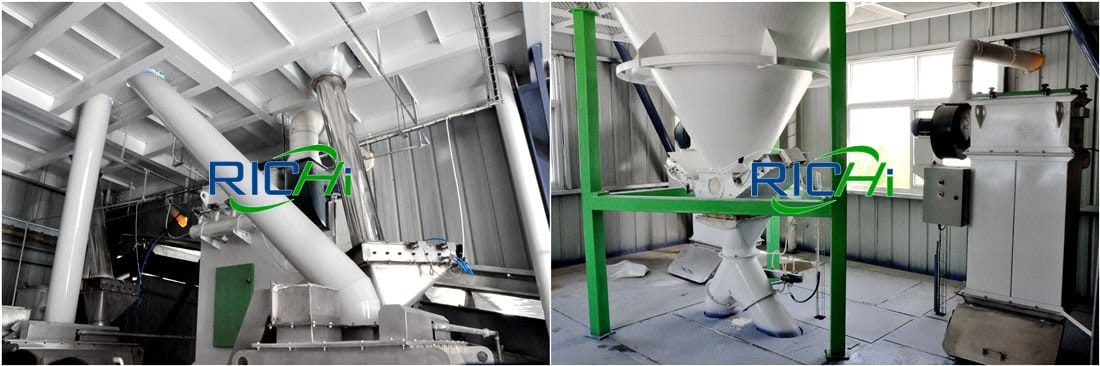
When the air humidity is not high In this case, the steam is not turned on for heat exchange, and the air at normal temperature is used to cool the material directly, saving the consumption of steam. Only in humid conditions, it is necessary to use steam for low-temperature drying. According to the calculation of the enterprise, after the process is optimized, the product output can be doubled with the same steam consumption.
To sum up, after process optimization, under the 24h/d production condition, the existing 4t/h boiler can support 6 times the original feed production capacity. After the expansion, the products have been adjusted. Some of the products are powdered feeds, which only need to be crushed and mixed, and there is no need to consume steam for granulation and drying.
Based on the above three points, it is reasonable and feasible to expand the feed production capacity to more than 7 times the original production capacity under the condition that the original boiler steam unit output remains unchanged.
Energy consumption of the expansion 4-5t/h feed pellet production line:
Name | Annual Consumption |
---|---|
Water | 13672.8t/a |
Electricity | 1600000kwh |
Biomass fuel | 1200t/a |
Remark:
- Biomass pellet fuel: The pellet biomass fuel is mostly a block-packed environmentally friendly new energy produced by processing stem-shaped crops. The diameter is generally 6-8 mm, the length is 4-5 times its diameter, and the breakage rate is less than 1.5%~ 2.0%, the dry basis moisture content is less than 10%~15%, the ash content is less than 1.5%, the sulfur content is less than 0.06%, and the nitrogen content is less than 0.24%.
- The amount of biomass fuel used before the expansion did not reach 2560t/a, and the actual amount used was 600t/a. Therefore, this 4-5t/h feed pellet production line project is analyzed based on the actual amount of 600t/a used before the expansion.