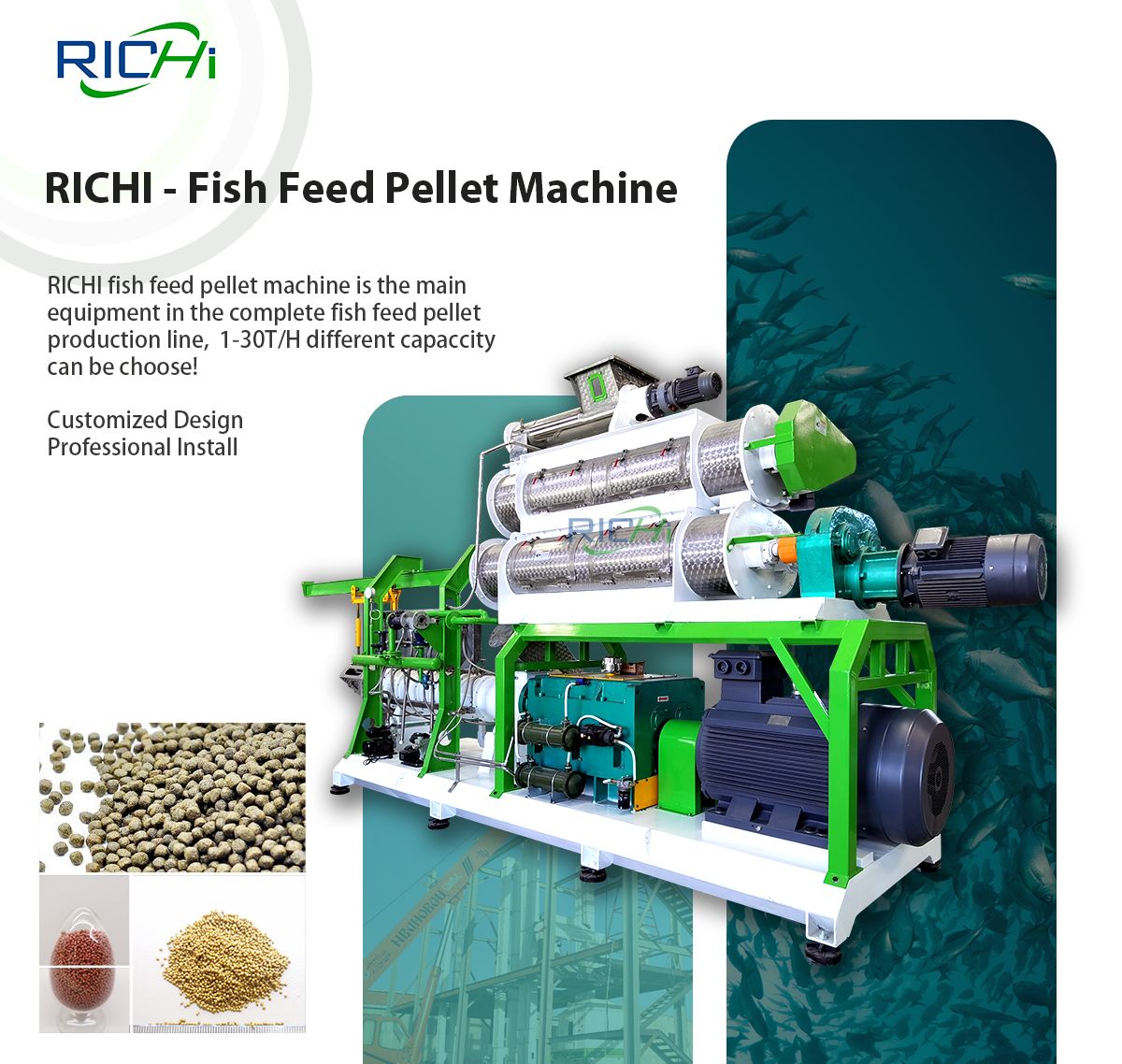
RICHI 6-7 t/h floating fish feed pellet mill is a kind of fish extruder for processing high, medium and low formula extruded feed, which can meet the needs of various feed processing customers. It represents state-ofthe art technology, ensuring unique quality feed at minimum operating costs.
The optimized extrusion concept for unmatched performance consists of controlled feeding of dry ingredients, optimal conditioning with steam and liquid addition, an even flow rate to the extruder, and high extrusion flexibility and controllability.
In addition to providing manufacturing, transportation and installation services, our expert team will also help you with training courses and the actual learning process, helping you become one step ahead in the market.
- Capacity: 6-7 tons per hour
- Type: Twin screw
- Application: for processing floating aqua feed, sinking aqua feed, pet food, poultry & livestock feed, etc.
Video of floating fish feed pellet mill
With over 20 years of experience in aqua feed and pet food extrusion, RICHI 6-7 t/h floating fish feed pelleting mill is a reliable system for a wide range of feed products. We not only manufacturing the machine, but also establish fish production plant for global customers.
Application of 6-7 t/h floating fish pellet mill
It can adapt to the processing of various types of aquatic feed such as floating water, fast sinking, and slow sinking, such as fish, shrimp, river eel, crab, turtle, bullfrog, ornamental fish and other high-end feeds that require floating pellet mills, especially particles aquafeed (diameter 0.5mm ~ 1.5mm), high-fat aquatic feed and feed with small production volume but often changing formula must be produced by twin-screw type floating fish feed extruder machine.
Features of 6-7 t/h floating fish feed pellet mill
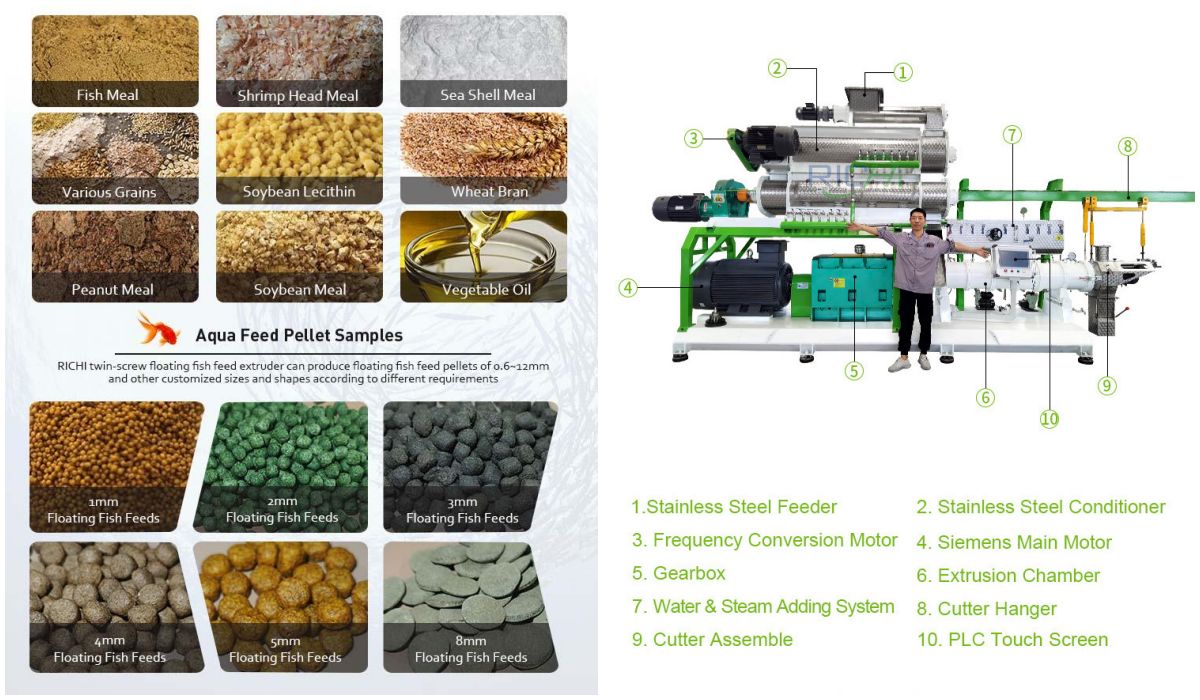
- The biggest feature of the RICHI twin-screw extrusion 6-7 t/h fish feed pellet mill that the two screws rotate in the same direction and are fully meshed to have the function of a positive pressure pump. It can mix various raw materials regardless of their composition.
- Various components such as protein, animal protein, fresh meat slurry, fat, high fiber, starch and wet fish residue can be easily processed, and are suitable for high-viscosity materials, low-viscosity materials or high-moisture, high-fat formula products processing.
- The screw design can uniformly pressurize the raw material to generate uniform expansion to develop a crunchy texture in pet food.
- The friction of the screw and liner inside the barrel can perform high-temperature short time cooking for the grains material.
- The main engine adopts frequency conversion control, and the screw speed can be adjusted, which is suitable for different formulas (sinking material, semi-floating material, floating material) .
- The fully meshed, zero-clearance twin-screw mechanism can effectively control the shear force and ensure that the curing time of all materials in the extruding cavity is consistent with the particle expansion coefficient.
- The appearance of the particles is neat, the water resistance is good, and the diameter of the mold is φ0.6mm-20mm; the vertical gear reducer drives the arch breaking device.
- The bearing in the transmission box adopts FAG or SKF bearing to ensure long-term stable operation.
- Effectively distribute the reasonable shear force in different areas of the extrusion cavity, and effectively increase the output under the premise of ensuring high quality.
- Our automatic fish pellet extruder machine adopts PLC+touch screen control system, easy to operate and simple.
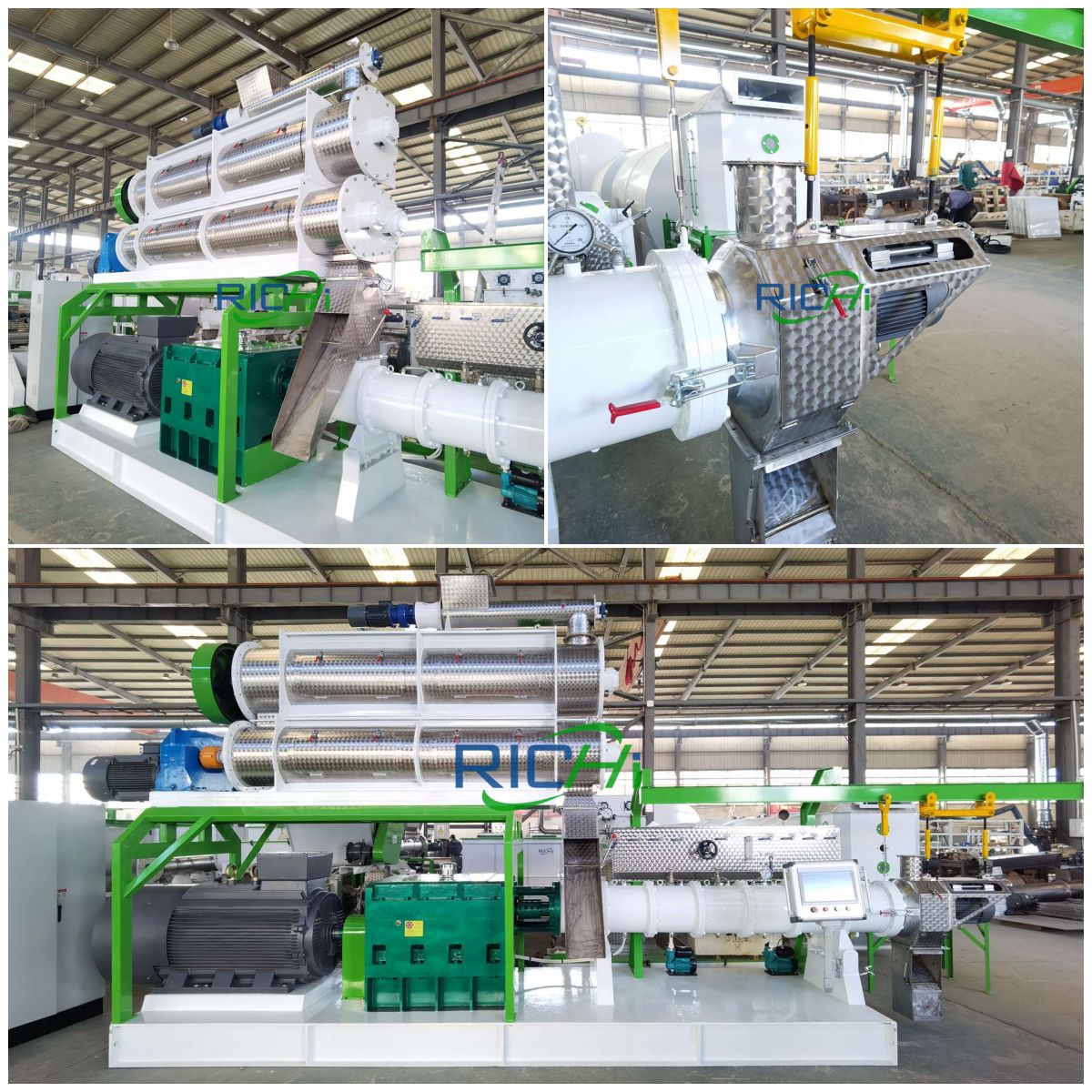
6-7 t/h floating fish feed pellet mill price & Parameters
6-7 t/h floating feed pellet mill cost: 140000-150000 USD
NAME | MODEL | QTY | POWER(KW) |
Anti-caking bin | PGS900/800 | 1 | 1.5+0.3 |
Inverter feeder | WLQ219-1300 | 1 | 1.50 |
Conditioner | DC500/244 | 1 | 11.00 |
DDC-conditioner | DDC500/400/244 | 1 | 11.00 |
Twin screw extruder | RCPH150*2 | 1 | 200.00 |
PLC control system | / | 1 | 0 |
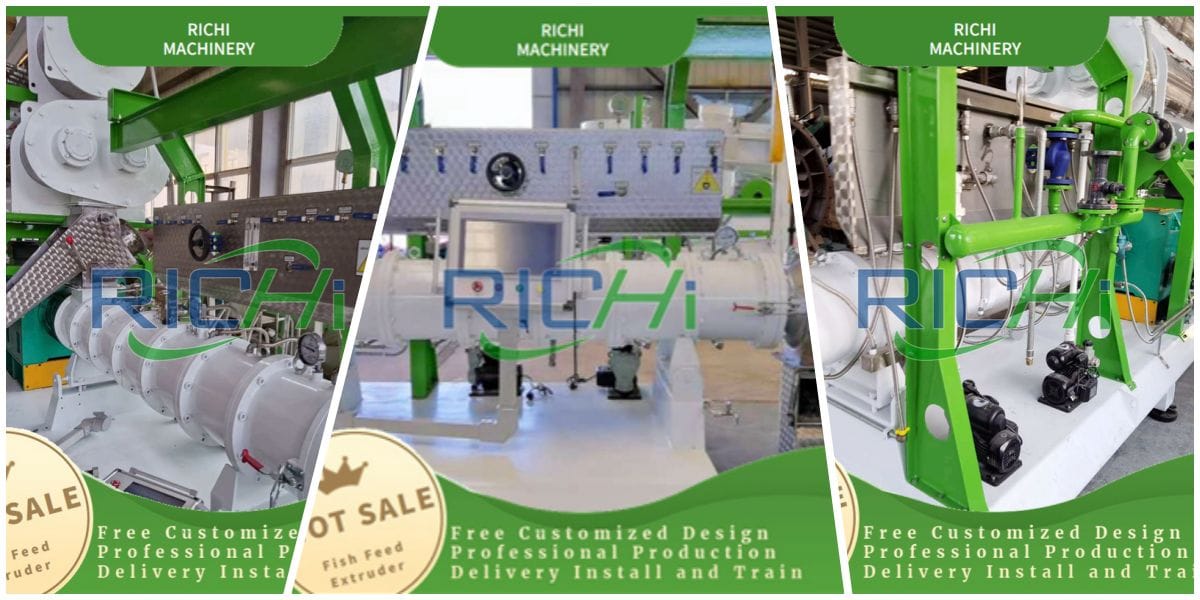
What kind of extruded feed do you want to process?
Aquatic feed can be divided into four categories: floating feed, semi-floating feed, sinking feed and slow sinking feed.
The main advantage of using the extrusion method to produce aquatic feed is that both sinking feed and floating feed can be grown with the same equipment, but as long as the characteristics of the floating fish feed pellet mill are mastered, ideal extruded feed products can be processed.
In addition, when RICHI configures floating pellet mill extrusion equipment and designs extrusion extrusion process for customers, you must first consider the requirements of your products:
- 1) shape and size requirements;
- 2) Density requirements;
- 3) nutritional requirements;
- 4) Stability requirements in water;
- 5) Appearance requirements;
- 6) Other requirements.
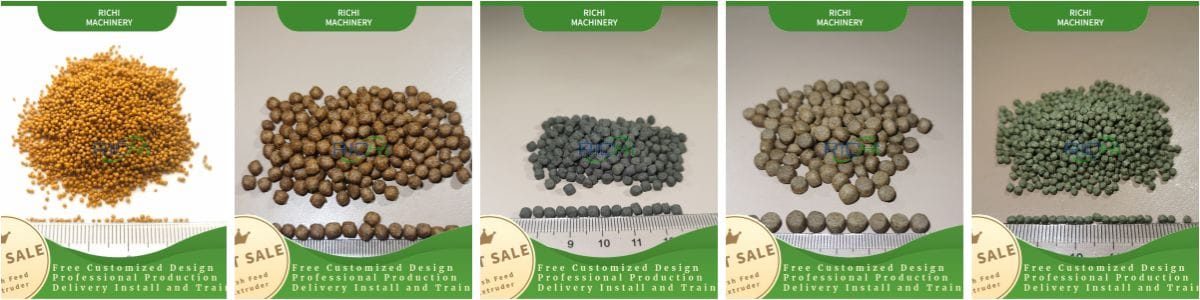
According to your product requirements, plant specifications, and process requirements, we will provide you with the most suitable floating fish feed pellet making machine products and a complete set of floating fish feed production line solutions!
How to choose a high-performance floating fish feed pellet mill?
When purchasing an fish feed extruder, customers must consider the reasonable structure and configuration of the floating fish feed pelletizing mill. The design of fish extruder components directly affects processing performance:
- The discharge end of the screw sleeve should be equipped with a device to adjust the material flow to reduce the difference in particle length;
- There should be a pressure relief device on the screw sleeve to facilitate the processing of relatively heavy sinking aquatic feed;
- The temperature control device should be installed on the screw sleeve to facilitate the control of the temperature of the screw sleeve.
- Whether the preconditioner device matches directly affects the product quality and operating cost, and should also be paid attention to. The pre-conditioner should be able to meet the needs of production, but also be able to add various liquid raw materials.
- At the same time, pay attention to whether the supporting system matches. The supporting system includes water adding system, steam adding system, other liquid adding system, temperature control system, etc.
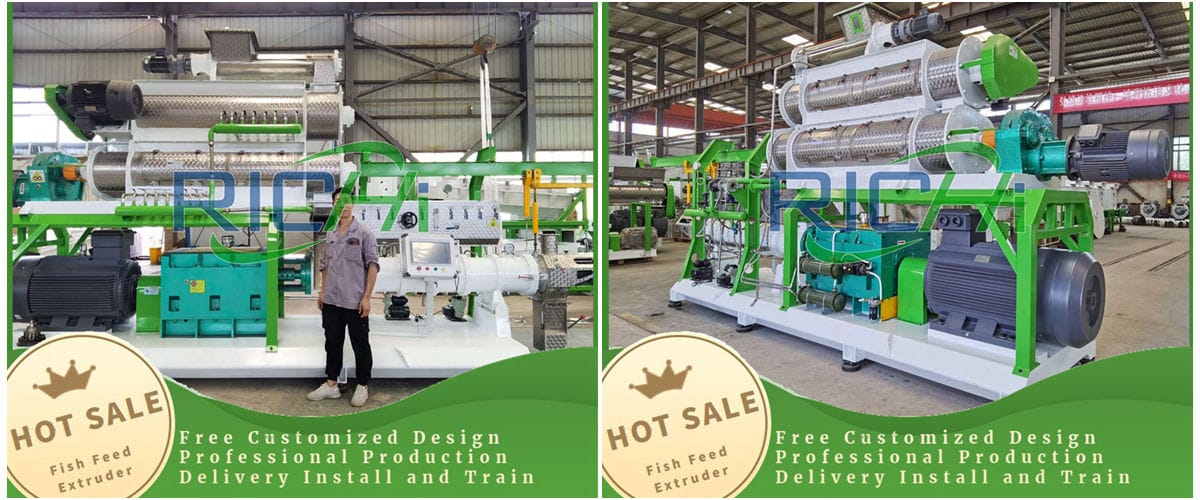
Raw material requirements for floating fish feed pellet mill production
The choice of feed formula has a decisive impact on the quality, nutritional content, shape and economy of the finished product. The selection of raw materials should not only consider the nutritional requirements, but also its processing performance.
For example, the crushing fineness of raw materials has an important impact on the appearance quality of finished products, and it will also affect the stable production of fish feed pellet mills. To produce high-grade aquatic feed, high-quality raw materials must be used, because extrusion processing cannot improve the quality of raw materials.
- Protein is an important component of aquatic feed, and its content is usually 25% to 60% or even higher in the entire feed composition. Protein raw materials are divided into two categories: plant protein and animal protein. Both types of protein should be used in the formula to avoid the lack of certain nutrients.
- In aquatic feed, starch is usually the second most important component next to protein, and its content can range from 5% to 60%. It is recommended that the starch content of sinking feed is not higher than 10% to 15%, and the starch content of floating feed is not lower than 20%. Carbohydrates also act as binders, suspending agents and emulsifiers in extrusion processing and are an important determinant of flavor profile.
- Fat or lipid is a very good energy source for aquatic feed, and the total content in the formula usually does not exceed 22%, so that the energy consumption and the wear of the vulnerable parts of the floating fish feed machine are less.
- Fibers include cellulose, hemicellulose and lignin, which are usually used as fillers and also provide some nutrients. Only a small amount of fiber can be added to the product to improve the puffing effect, but if the content is too high, the puffing will be reduced instead.
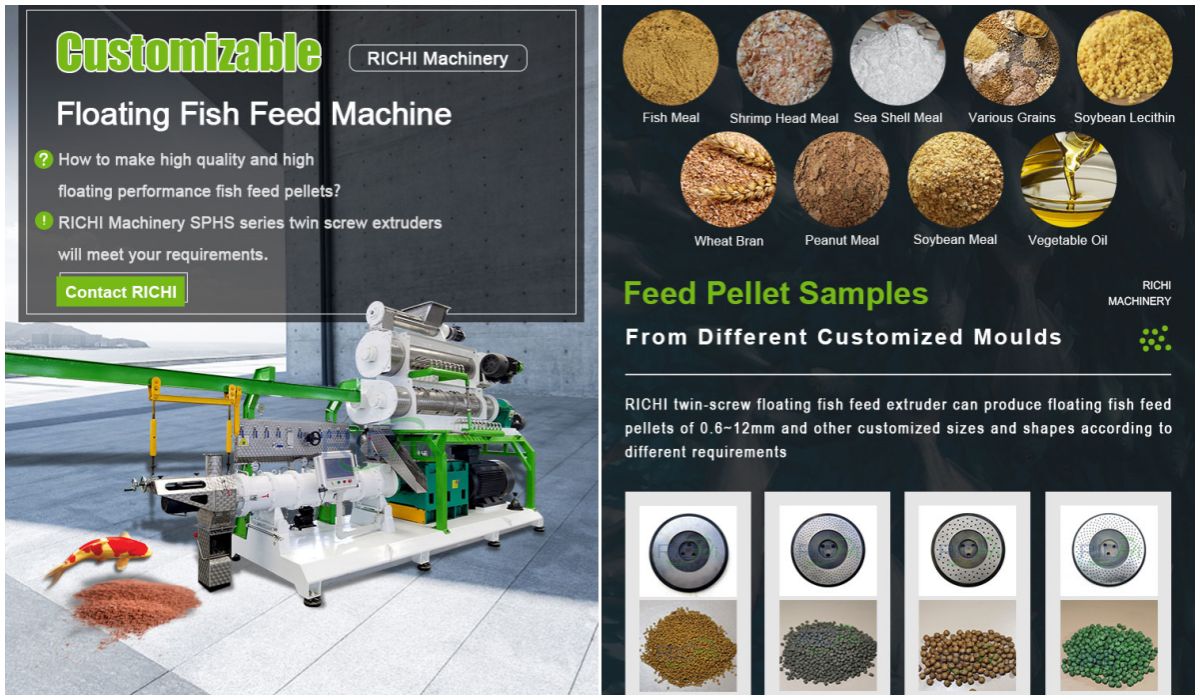
Requirements of raw materials crushing particle size
Since the digestive tract of aquatic animals is short and thin, it is not easy to digest large pellet feed, so it is necessary to reduce the fineness of raw materials. The aperture of the sieve plate of the hammer mill is usually only 1mm minimum, and can only produce particles above Φ3mm. If you want to produce particles below Φ3mm, you generally need to use a micro pulverizer to meet the requirements.
The finer the fineness, the smoother the surface of the produced pellets and the higher the maturity of the extrusion pellets. In addition, the finer the fineness, the more stable the production of the floating fish feed pellet mill and the smaller the wear of the wearing parts.
Processing conditions of 6-7 t/h floating fish feed pellet mill
- The control of feed pellet density can be realized by controlling the steam and water in the screw sleeve, and the fish feed should be depressurized before being extruded. The volume of floating feed is generally increased by more than 1∙5 times, and the volume of sinking feed is generally increased by 1∙05~1∙1 times; the product size is realized by controlling the cutter speed, and the product length is generally 1∙0~1∙5 times of the aperture.
- Appearance control According to different characteristics of the product, different cutting methods are adopted. Particles with a diameter below Φ3∙0mm are cut with a thin blade; particles with a diameter above Φ3∙0mm are cut with a thick blade.
- The speed of the cutter and the form of the cutter have an important impact on the appearance of the product. Accurate metering control is required for the materials entering the 6-7 t/h floating fish feed pellet mill. Accurate metering of the amount of materials entering the extruder is the basis for judging how much steam, water and other liquids should be added, which is very important for the stable operation of the system.
- Steam conditioning is very important for the production of floating feed. High-quality dry saturated steam should be used. The temperature of the material after conditioning should be around 90℃, and the humidity should be 25% to 30%. Steam conditioning can also increase the degree of expansion of the product, which is very beneficial to the production of high-protein/fat floating feed, but it is not suitable for the production of small particle sinking feed.
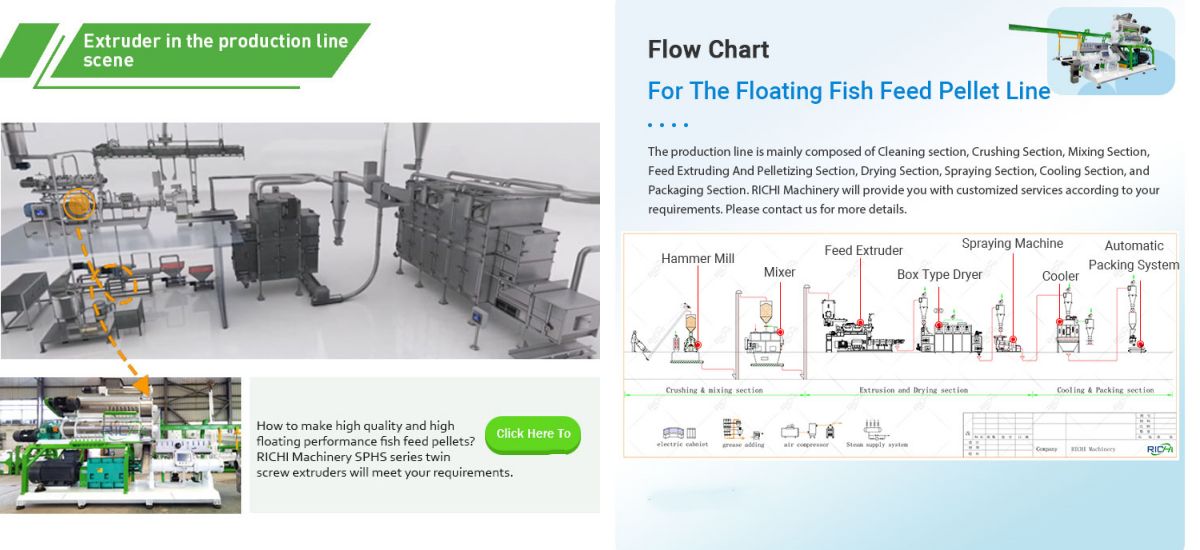
- Post-processing of extrusion Drying, post-spraying, cooling and grading are also indispensable for the production of high-quality aquatic feed. The freshly extruded feed is very fragile, and a reasonable conveying system needs to be installed to transport the feed to minimize product damage, preferably a conveyor belt or an air transport system.
- To produce high-quality aquatic feed, the drying process is as important as floating fish feed pellet mill extrusion. To master the drying time, control the drying temperature at no more than 100℃, so that the thickness of the material layer and the drying time are in the best process condition. After the product is dried, it should be sprayed with fish oil and other liquid raw materials while it is hot. The hot product can quickly absorb the liquid and maintain the stability of the particles in water.
- Fat-sprayed aquatic feed is more palatable to fish. In addition, the appearance is more beautiful and easy to be accepted by customers.
- Cooling is required after spraying, because the particles are still very hot after spraying, and the product will condense if not cooled, resulting in mildew and deterioration. The product must be cooled to no higher than 4℃ above the ambient temperature, so as to ensure the quality of the product.
- Finally, it is required to sieve out the powder formed in the process before packaging.
We do that by providing RICHI floating fish feed equipment that makes up complete, customized solutions from mixing and grinding to sifting, extruding, shaping, drying and coating/cooling feed pellets for various species, match fish feeding habits, and ensure optimum health and feed conversion rates.
Together with us, you may benefit from establishing your own aquaculture feed production based on high-performing standardized feed processing plants from Richi Machinery.
Depending on which machinery is used, different fish feed plant design can be met. The floating fish feed pellet mill usually does not work independently, but forms a production line system together with other crushing, mixing, drying, spraying, and screening equipment to realize the extruded feed Accurate processing, improve product pertinence, increase its market value.
Main floating fish food production line equipment
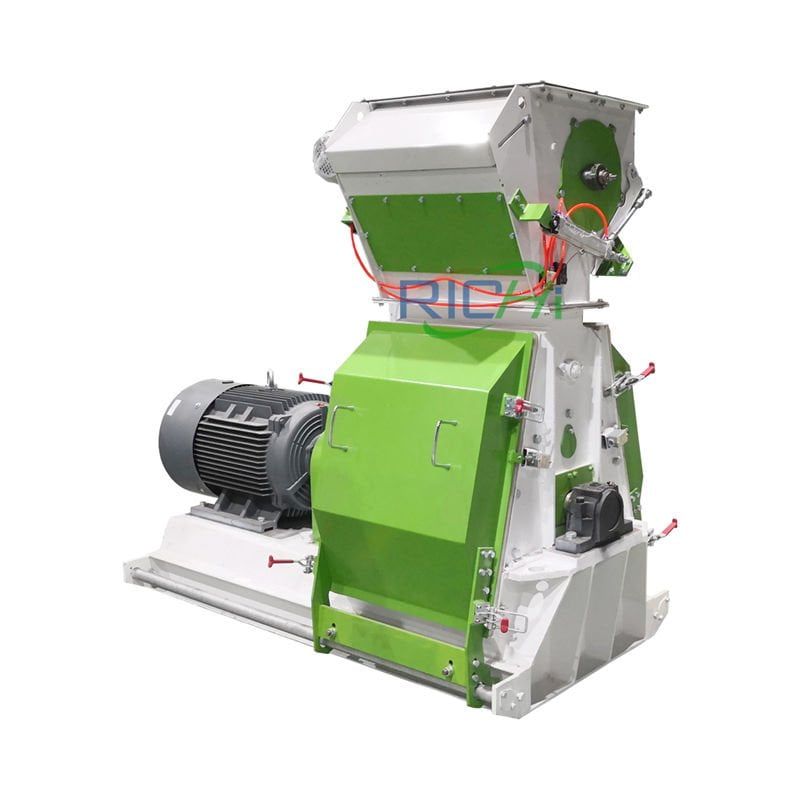
Fish Feed Grinder
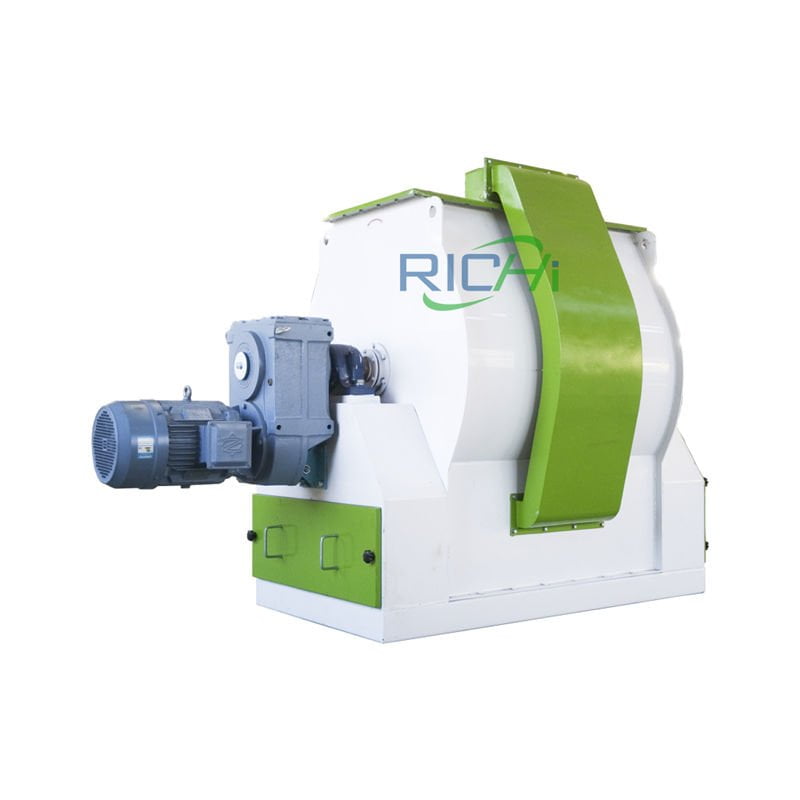
Fish Feed Mixer
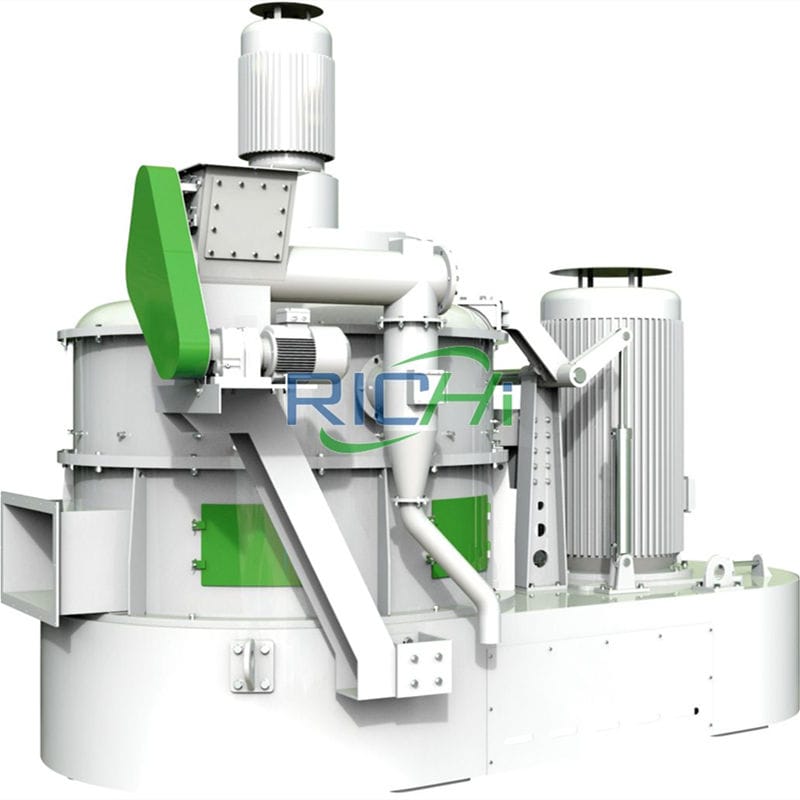
Ultrafine Grinder
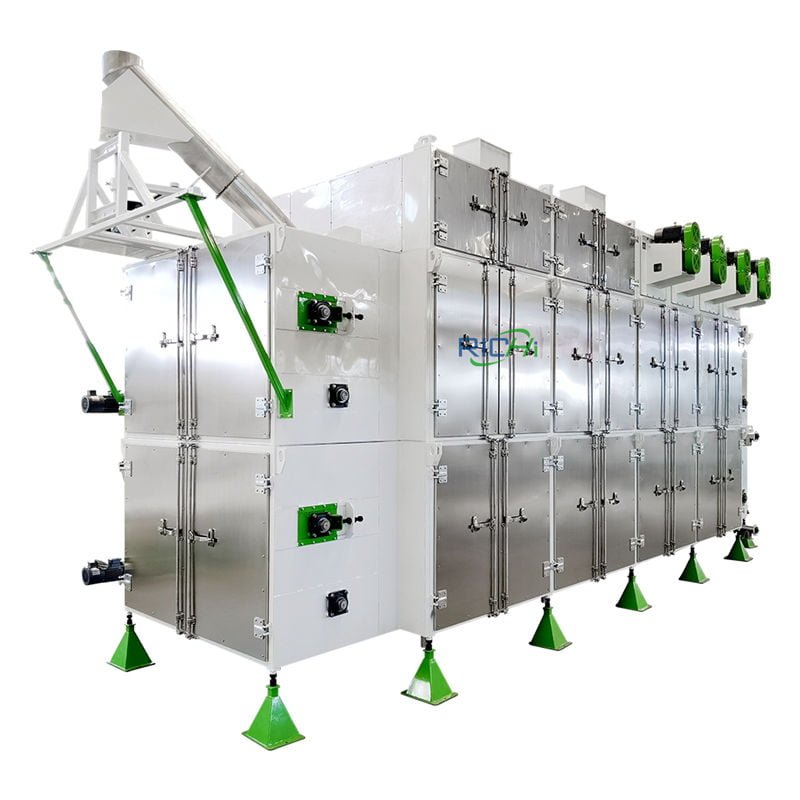
Fish Feed Dryer
about Us
Richi Machinery is a provider of feed machinery equipment and whole plant engineering system solutions with the feed industry as the main body. It specializes in the production of feed machinery, feed equipment, ultrafine pulverizers, dryers, grease sprayers, floating fish feed pellet mills and other products.
We provide complete aqua feed production solutions, ensure extruded feed safety and increase yield. Our aquaculture feed processing solutions provide complete control over the entire process so you can produce fish feed of the highest quality. (Find us on YouTube)
Featured floating fish feed plant solution
FAQs of floating fish feed pelleting mill
Our density control system is additional device for floating pellet mill line production for producing sinking feed, slow-sinking feed and density-controlled extrusion product.
The density control system comprised of airtight knife housing and airlock. The knife housing is paired with the airtight plate die to form closed environment. The airlock is fixed with a clamp to the knife housing.
The controlled pressure is able to:
Control the water boiling point, ensure less flash-off, prevent expansion, and increase pellet density.
Increase density of extruded pellets, increase feeding rate, thus increase the capacity.
We understand that maintenance is also one of the substantial aspects of choosing a machine. RCIHI floating fish feed making mills are made from high-quality metal with an advanced manufacturing process to ensure the durability of the fish food extruder. Continuous lubrication of the bearing house and gearbox are direct- linked to the main power as a safety precaution. The lubrication system minimizes the downtime caused by the gearbox and bearing house failure.
We have a professional after-sales technical team and a complete accessories supply system, which can provide you with a full range of services.
Regular inspections are needed for operation safety and to keep your production systems working optimally and efficiently. Please call us for your extrusion line maintenance with experienced engineer support. An ounce of prevention is worth a pound of cure.
The working principle of producing all kinds of aquatic feed by extrusion method is: after the powdery raw material containing a certain starch ratio (above 20%) is subjected to conditioning treatment by the conditioner, its moisture content rises to (20%-30%) ), the temperature rises to 80-90
℃, and then enters the screw extrusion cavity.
In the extrusion cavity, the extrusion force on the material gradually increases, and at the same time, the process of the material moving in the extrusion cavity is accompanied by intense shearing, kneading and friction action.
Sometimes, according to the need, the steam flowing through the barrel jacket can also be used to heat the partition wall of the material, so that the temperature of the material can be raised sharply by 110-200℃), so that the starch in the material is gelatinized, and the whole material becomes melted plastic jelly. But the residence time of the feed at high temperature is very short (5-10 seconds).
Before the material is extruded from the floating fish feed pellet mill template, the moisture contained in it does not turn into water vapor under high pressure, until the moment the material is discharged from the die hole, the pressure suddenly drops to an atmospheric pressure, and the moisture quickly turns into water vapor to make the material volume expands rapidly.
As a result of further evaporation and dissipation of water vapor, the moisture content of the material is reduced.
At the same time, due to the rapid drop in temperature, the gelatinized starch coagulates immediately, leaving many micropores in the coagulated colloidal material. This high-temperature, short-time floating fish feed pellet mill processing maximizes the heating of feed ingredients, improves digestibility, inactivates anti-nutritional factors, and sterilizes), while minimizing nutrient loss.