Origin of 20 t/h fish feed production plant project
The customer’s feed company was established in April 2013 and is mainly engaged in feed processing and production. The total fish feed production plant area is 9077.8m². In June 2013, the customer invested about 500,000 US dollars to build a “feed production line project with an annual output of 30,000 tons”.
The main construction contents of the project are: 1 production workshop (5 floors in the main production area), 1 finished product warehouse, and raw material warehouse 1 room, as well as packaging room, office room and corresponding environmental protection facilities.
The original compound feed mill project used corn, soybean meal, wheat bran, wheat, rapeseed, cottonseed, etc. as raw materials, and through the processes of mixing and crushing ingredients, the annual production of livestock and poultry feed was 30,000 tons.

In order to meet the market demand, the customer company invested an additional US$2 million to expand the existing factory area. After the expansion, 50,000 tons/year of special aquatic extruded feed was added, and the original 30,000 tons/year livestock and poultry feed production line remained unchanged.
This 20t/h fish feed production plant project does not add new construction land, but only expands the special aquatic product extruded feed production workshop in the open space east of the original factory area. In addition, raw material workshops, product workshops, packaging workshops, office buildings, hazardous waste temporary storage rooms, solid waste temporary storage rooms, etc. all rely on the original project and will not build new ones.
The 20t/h floating fish feed mill project covers an area of 2400m², construction area of 2400m², and 7 new employees.
Product solutions
Before the expansion, the project was mainly engaged in the production of compound feed for livestock and poultry, with an annual production of 30,000 tons of compound feed for pigs, chickens and ducks. This 20t/h fish feed production plant project is mainly engaged in the production of special aquatic extruded feed, with an annual output of 50,000 tons of special aquatic extruded feed.
Product Name | Before Expansion (t) | Output after expansion (t) | Storage location and maximum reserve (t) |
---|---|---|---|
Livestock Feed | 30000 | 30000 | Finished product warehouse, 200 |
Extruded Fish Feed | 0 | 50K | Finished product warehouse, 500 |
Energy consumption
Water | 1838.45m³/a |
Electricity | 800,000 KWh/a |
Main raw material consumption
Name | Consumption after expansion (t/a) |
---|---|
Corn | 33000 |
Wheat Bran | 5050 |
Wheat | 2450 |
rape meal, cotton meal | 4500 |
Soybean Meal | 23250 |
Rice bran meal | 3200 |
Calcium carbonate powder | 850 |
Fishmeal | 5250 |
Grease | 1225 |
Salt | 110 |
Wheat middlings | 1250 |
Vitamin Supplements | 55 |
Amino acid additive | 240 |
Propionic acid type antifungal agent | 100 |
Enzymes | 42.8 |
Mineral Additives | 130 |
- Enzyme preparations: The enzyme preparations used in this 20t/h fish feed production plant project are mainly amylase, lipase, maltase, mannanase, pectinase, phytase, protease, etc.
- Fishmeal: The fishmeal used in this project is purchased from a legal enterprise. The fishmeal in this project is mainly stored in the raw material workshop.
- Soybean meal: The soybean meal used in this project is purchased defatted soybean meal, which is mainly light yellow and irregular fragments, and the beany smell produced by it is small. The soybean meal used in this project is stored in the raw material workshop. Secondly, in order to ensure product quality and safe use, the raw and auxiliary materials used in this project all meet the feed and feed additive management regulations.
Work system
Before the expansion, there were 23 employees, and 7 new employees were added in this new 20t/h fish feed production plant, all of whom did not stay in the factory area for board and lodging.
The working system remains the same before and after the expansion, with 300 working days in a year, one shift per day, and 8-hour production per shift.
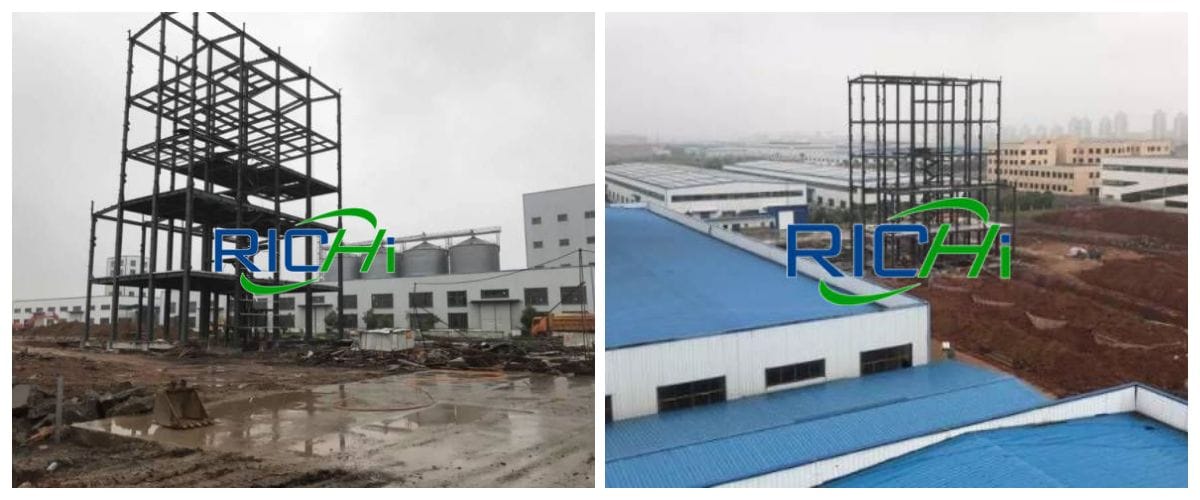
Main fish feed equipment
Before the expansion, the project mainly produced compound feed for livestock and poultry, and the list of supporting production equipment is no longer displayed; this 20t/h fish feed production plant project mainly adds the production of aquatic feed, and the list of supporting new equipment is shown in the following table:
Device name | Model |
---|---|
Scraper Conveyor | TDJSS10 |
Twin-shaft high-efficiency mixer | SLHY2-2 |
Air Cooler | SKLN24*24 |
Pulse dust collector | TBLMFa32 |
Bucket elevator | TDTG36/23 |
Preliminary cleaning | ZCCQ100 |
Fish feed grinder | SFSP138*50C |
Automatic packer | DCS |
Screw conveyor | LXG250 |
Feed pellet mill | SZLH508 |
Superfine Pulverizer | TDCWF |
Automatic batching system | TSC-1000 (including batching bin) |
Fish Feed Extruder | RCPH |
Fish feed dryer | HRHG8000 |
Rotary classifier | SFJH140-2C |
Counterflow cooler | 25*25 |
Public works
(1) Water supply and drainage
Water supply
The water used in this 20t/h fish feed production plant project is mainly water for cleaning the expansion chamber and domestic water for employees. Among them, the cleaning water of the expansion chamber is 60t/a, and the new increase of domestic water is 105t/a.
Drainage
The drainage system of this project adopts rain and sewage diversion system. Since the sewage pipe network in the project site has not yet been fully constructed, and the new waste water produced by the project is relatively small, about 132t/a.
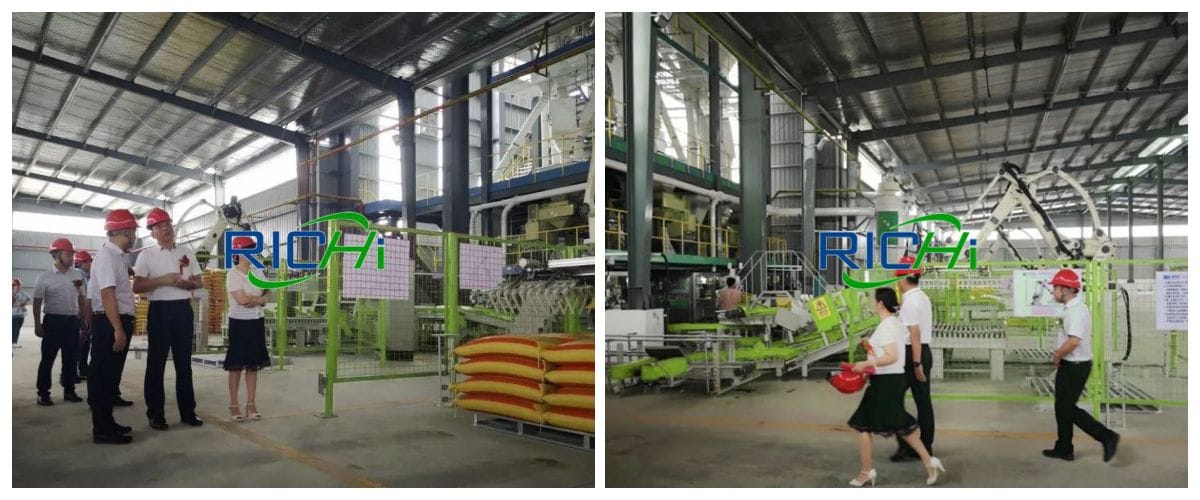
(2) Energy consumption
The power supply of this fish food processing line project comes from the local power supply network. The original project is equipped with an 800KV transformer, which can meet the power demand of the project.
The 20t/h fish feed production plant project is not equipped with diesel generators, and the power consumption before and after the expansion is shown in the table below.
Name | Before the expansion | After the expansion |
---|---|---|
Electricity | 300,000 kWh | 800,000 kWh |
20T/H fish feed production plant process design
This project is a reconstruction and expansion project. The factory building is based on the original factory building, and there is no need to excavate earth to build a new one. Therefore, the construction period is relatively simple, and only the factory building renovation and equipment installation are required for the extruded aqua feed mill. The construction period takes a short time and is all indoor operations.
The production process of extruded aquatic feed adopts a complete production process of crushing first, then batching, intermittent mixing, (ultra)fine crushing, secondary batching, extruding, drying, oil spraying, cooling (air cooling), screening into the finished product warehouse and packaging.
This 20t/h fish feed production plant project adopts the current relatively advanced fully automated production technology, and all links of the entire production process are completed in a sealed state.
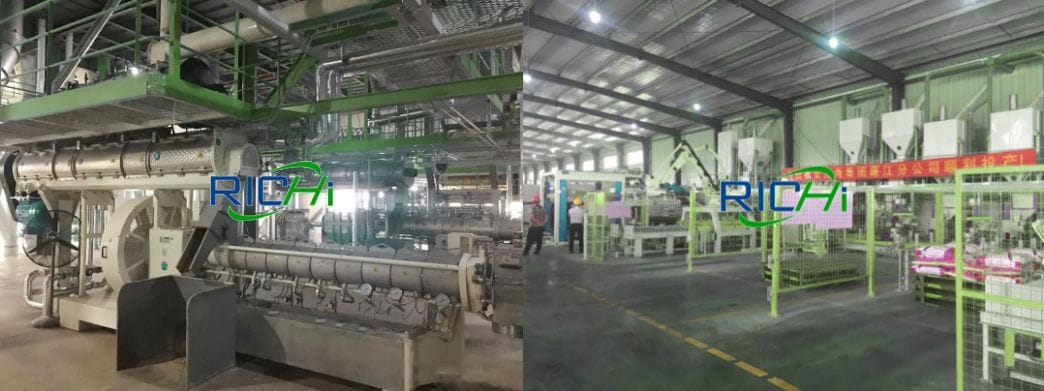
(1) Feeding cleaning section
Because the raw materials purchased by the fish feed factory contain a certain amount of impurities, the grid screen at the feeding port can be used as the first impurity removal equipment to remove impurities such as sack lines.
Each feeding port is equipped with a separate square pulse dust collector; the powder and meal are manually unpacked in the aquatic feed production workshop and then put into the feeding port.
After cleaning and iron removal by scraper machine and elevator, the meal enters the standby The crushing bin, the auxiliary powder material enters the batching bin. (Vehicles for purchasing raw materials for the project can go directly to the raw material stacking area, and unloading is carried out manually. Dust is only generated from the moving of raw materials. In fact, raw materials are all packed in woven bags.)
(2) Primary crushing section
Due to the large particle size of raw materials such as corn and soybean meal, they need to be crushed to meet the production requirements so that they can be turned into powdery materials. The crushed raw materials are lifted to the batching bin by an automatic elevator for temporary storage.
(3) Primary ingredient mixing section
The batching process adopted in this 20t/h fish feed production plant project is batching with multiple bins and scales, which is a kind of automatic batching. The crushed raw and auxiliary materials are sent to different batching bins by the distributor.
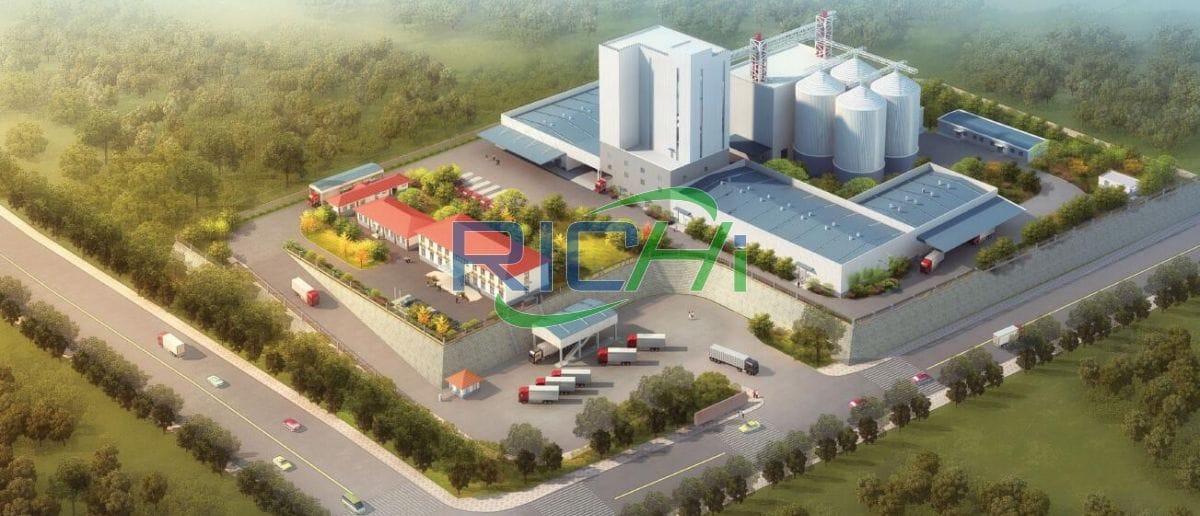
(4) Secondary ultrafine grinding section
In order to increase the taste of the feed and make the feed more suitable for fish consumption. After the various raw materials are mixed, they will enter the closed ultrafine pulverizer for secondary pulverization.
(5) Secondary ingredient mixing section
Assuming that according to the formula requirements, various raw materials participating in the batching are weighed and entered into the mixer in sequence, and various core materials are added into it during the mixing process. The mixing cycle is 6 min.
(6) Extrusion and tempered
Raw materials after secondary crushing enter the single-cylinder conditioner, and the materials are extruded and tempered by high temperature and high pressure (about 120℃, 2 atmospheres).
(7) Drying and oil spraying
In the process of extruding and tempering, due to the introduction of high-temperature and high-humidity steam. And the extrusion of materials generates a lot of heat, the moisture content of the extruded aquatic feed is relatively high when it comes out of the conditioning machine. (Related post:floating fish feed machine )
And it will also cause sticking when it is directly stored. and mildew phenomenon, so the material is dried through steam heat exchange, and oil is sprayed into the material at the same time to increase the edible taste of the feed.
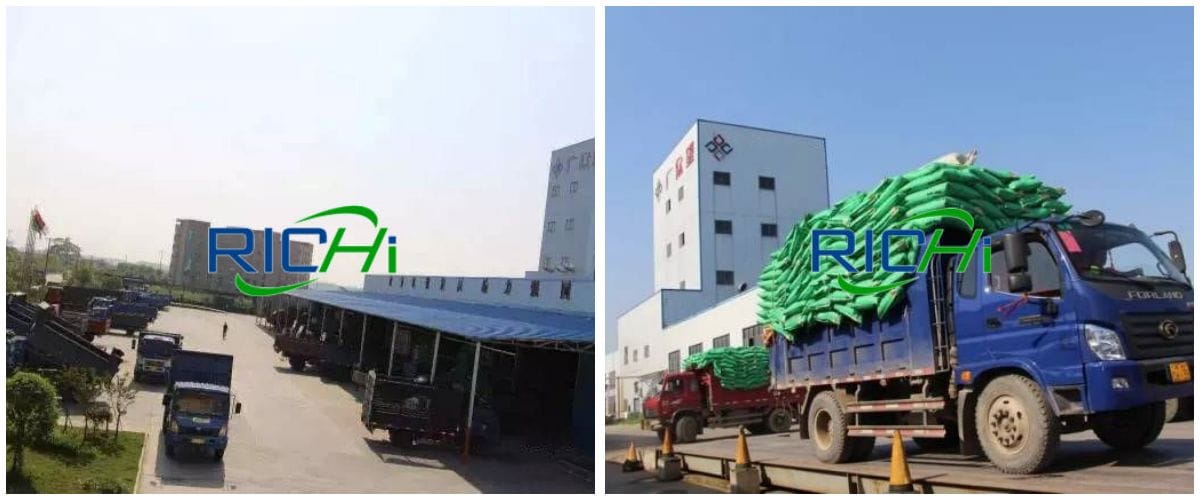
(8) Ventilation and cooling process
The temperature of the material coming out of the drying equipment is as high as 70℃-85℃. Under this condition, the pellet feed is easily deformed and broken. This 20t/h fish feed production plant process adopts the form of countercurrent ventilation and cooling to reduce the temperature of the feed to below 8℃ higher than room temperature.
(9) Screening, packing and warehousing process
After the cooled feed is screened, the qualified pellet size enters the finished product warehouse, and is packed into the warehouse through the automatic packaging machine.
Note:
- The fish feed mill plant project will generate dust during the feeding, crushing, mixing, screening and packaging processes, so the process considers installing fans and pulse dust collectors at each dust generation point to recover useful materials and reduce dust pollution in the workshop .
- The steam required for the expansion, conditioning, drying and other processes of this project comes from the centralized gas supply, and there is no boiler gas supply for this project.
Relying on engineering feasibility analysis
(1) Raw material workshop
According to the on-site survey, the customer company’s annual output of 30,000 tons of animal feed production line (the original project) has built a raw material warehouse with a construction area of about 1500m².
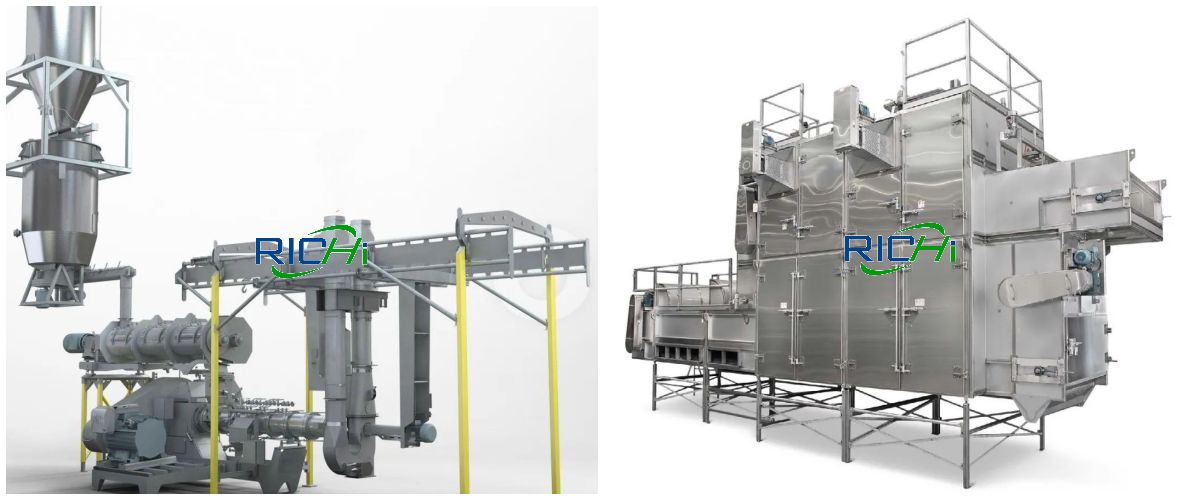
If the average stacking height is calculated as 2m, the existing raw material warehouse can store 3000m3 of raw materials. Since the raw and auxiliary materials used in this 20t/h fish feed production plant project are basically the same as the existing project, the maximum storage capacity after the expansion is about 2700t, so the existing raw material warehouse can meet the storage needs of raw and auxiliary materials after the expansion.
(2) Product Workshop
According to the on-site survey, the original project has built a product warehouse with a construction area of about 1500m², and the average stacking height is calculated as 2m, so the existing product warehouse can store 3000m³ products.
After the expansion, the total product output of the feed project is about 80,000 tons per year, and the storage period is calculated on the basis of half a month, so the maximum storage capacity of the product is about 3,333 tons. Therefore, the existing product warehouse can meet the needs of product stacking after expansion.
(3) Packaging workshop
According to the on-site investigation, the existing project has built a packaging workshop with an automatic baler, and there is still enough space in the existing workshop to install an automatic baler.
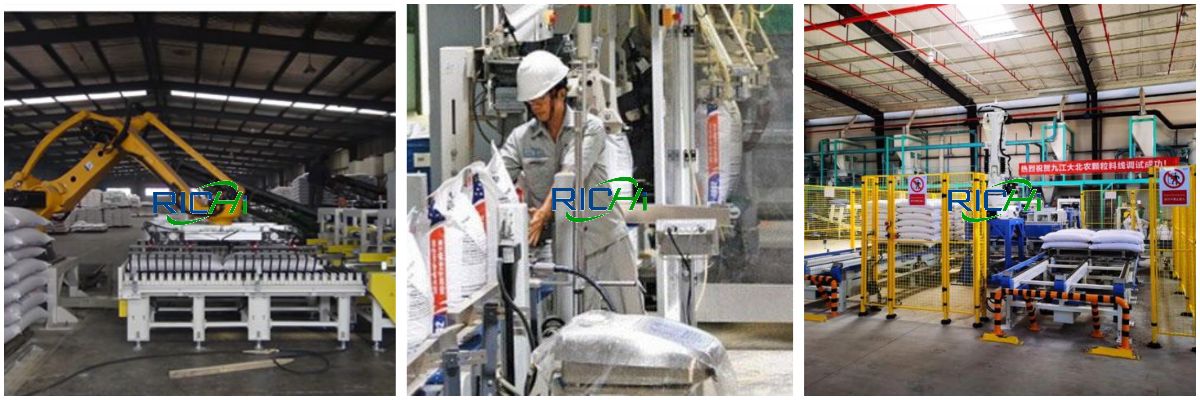
(4) Hazardous waste temporary storage room
According to the on-site investigation, the company has built a standardized hazardous waste temporary storage room for the annual production of 30,000 tons feed production line, which is located in the southwest corner of the factory area, covering an area of about 5m², and signed a hazardous waste disposal agreement with a local company.
he hazardous waste generated in this 20t/h fish feed production plant project is mainly waste activated carbon, and the existing hazardous waste temporary storage room can meet the temporary storage requirements of waste activated carbon.
Plane layout
The gate of the project factory area is set near the rural road on the west side. The factory area is mainly divided into living area and production area. The main production workshop of the original project livestock and poultry feed production line is located in the middle of the factory area, the finished product warehouse is located on the west side of the central part of the factory area, and the raw material warehouse of the factory area is located in the east.
The packaging room is located in the southwest corner, the expanded aquatic feed mill of the project is located in the east of the raw material warehouse, and the office space in the living area is located in the northwest corner.
According to the design principles of reasonable zoning and block layout, this 20t/h fish feed production plant project makes full use of the existing factory building for renovation and layout. The factory area is mainly divided into living area and production area.
The storage room and auxiliary room completely rely on the original project. The extruded aquafeed production area with strong peculiar smell is located far away from the office building to reduce the impact of peculiar smell on the living area of employees.
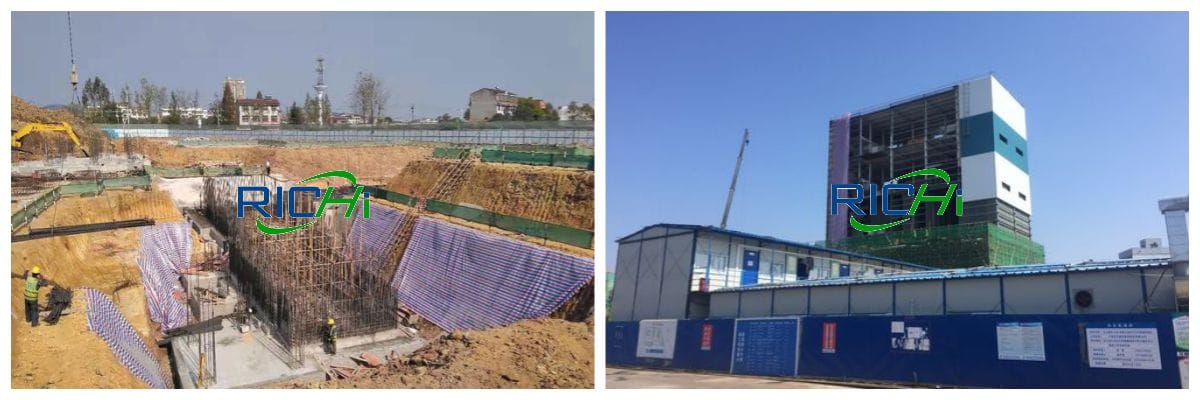
The rationality of the plan layout of the fish feed pellet production line project is mainly manifested in the following aspects:
- The transportation of the project is convenient, which facilitates the entry and exit of materials and timely delivery of products.
- There is a clear boundary between the production workshop and the office area, and each functional area is clear.
- The production equipment is arranged in the workshop, which can make full use of the wall to block the noise and effectively reduce the impact of production equipment noise on the external environment.
To sum up, from the perspective of environmental protection, the layout of the 20t/h fish feed production plant project is reasonable.