Background of 25 t/h aqua feed production line
The client company of this large aqua feed production line project was established on March 27, 1996. Its business scope: production and sales of feed, feed additives, fishery machinery and facilities, fishery medicine, seedlings, biological agents, water quality improvers; grain purchase and sales; aquatic product purchase, sales; aquaculture and technical consulting services; crop planting; photovoltaic power generation; site rental; sales of soybean meal, rapeseed meal, cotton meal, peanut meal, fish meal, chicken meal, shrimp meal, flour, and corn gluten meal.
In order to meet the market demand, the client company invested 8 million US dollars (including civil engineering) to build a new production plant and its auxiliary facilities in the existing factory area, with a total construction area of about 14,000m².
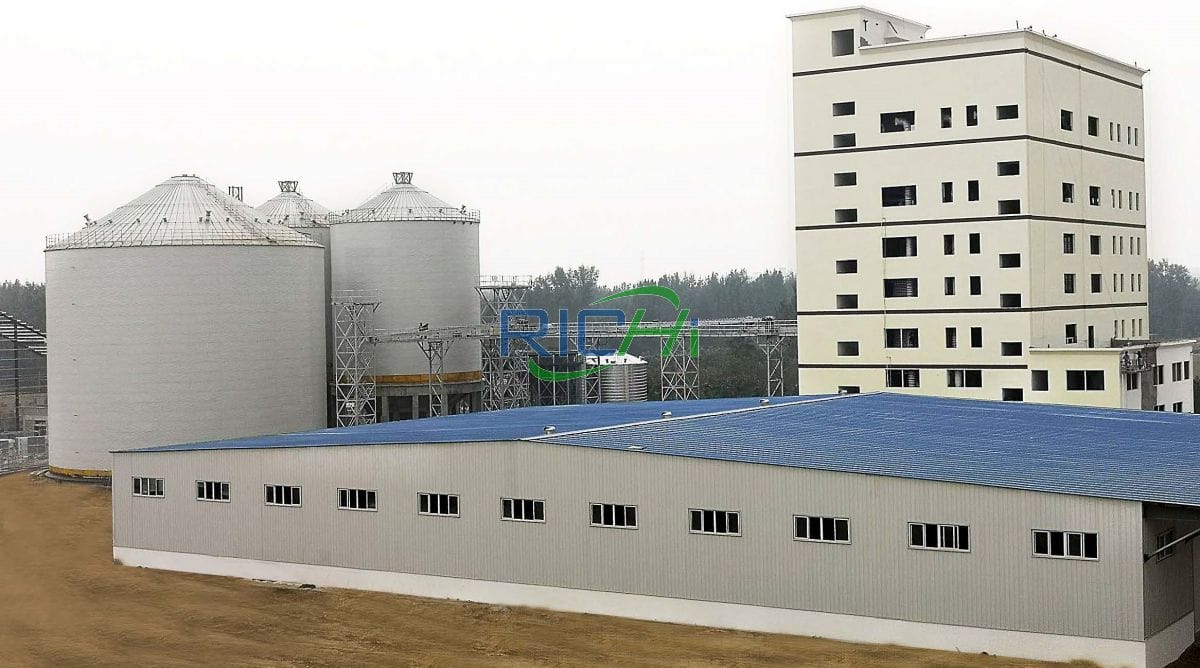
At the same time, it also purchased twin-screw extruders and shrimp feed pellets machine, twin-shaft paddle type high-efficiency mixer and other main production equipment.
After the 25t/h aqua feed production line project is completed and reaches its full capacity, it can form an additional production capacity of 190,000 tons of compound feed such as prawns, crabs, and lobsters. (Related solution: 20T/H fish feed production plant)
- Project nature: expansion;
- Number of employees: 20 new employees;
- Working system: production in three shifts, 8 hours per shift, 312 working days per year.
Main Products and Capacity
The product plan of the 25t/h aqua feed production line project is shown in the table below.
Product name | Feed size (mm) | Existing capacity (t/a) | Output of expansion (t/a) | Capacity after expansion (t/a) |
---|---|---|---|---|
More than 300 kinds of feeds in five categories including livestock and poultry, general aquatic feed, special aquatic feed, premix and additives | / | 20000 | / | 20000 |
Ecological nutritional special aquatic feed | / | 60000 | / | 60000 |
Shrimp feed/crab feed/special aquatic feed | (1.0-1.2)/ (0.1, 0.3, 0.5)/(1.0-4.0) | / | 90000/50000/50000 | 90000/50000/50000 |
Main Raw Materials
The use of main raw and auxiliary materials in the 25t/h aqua feed production line is shown in the table below:
Material Name | Annual consumption (tons/year) | Maximum storage capacity (tons/year) |
---|---|---|
Corn | 20,000 | 150 |
Wheat | 15,500 | 120 |
Additives | 15,000 | 0.05 |
Soybean Meal | 70,500 | 800 |
Rape Meal | 15,000 | 800 |
Flour | 30,000 | 400 |
Peanut Meal | 30,000 | 400 |
Fishmeal | 70,000 | 800 |
Chicken Powder | 10,000 | 300 |
Grease | 5000 | 100 |
Hydrochloric Acid | 0.5 | 0.05 |
PAC | 0.5 | 0.05 |
PAM | 5 | 0.5 |
25T/H aqua feed production line process design
Aqua feed Pellets production
- 1. Manual feeding: The soybean meal, rapeseed meal and peanut meal are manually put into the pipeline according to the proportion. The feeding port is under negative pressure. The raw materials are flake and powder, and the particle size is large.
- 2. Crushing: The raw materials of the 25t/h aqua feed production line project, such as soybean meal, rapeseed meal and peanut meal, are crushed by a closed water drop type crusher. (Related solution: 18t/h shrimp and fish feed factory)
- 3. Mixing: according to the recipe requirements, put flour, imported fish meal, domestic fish meal and chicken meal into the mixer in turn after weighing, and mix evenly in the double-shaft feed mixer. The effective mixing time of each batch is 90 seconds. This process is completely sealed.
- 4. Superfine pulverization: The mixed raw materials are pulverized with a superfine pulverizer. The pulverizer chamber adopts a fixed knife structure as a secondary impact pulverization technology, which can increase the output by more than 30%, and can change the position of the hammer on the rotor.
The position can form two kinds of hammerstone sieve gaps, which are suitable for ordinary crushing and fine crushing, and the crushing fineness is more uniform, reaching 100 mesh and 96% 2 tons per hour. The superfine pulverization equipment is equipped with a shock-absorbing foundation and a muffler. Crushing, mixing, and superfine powder process materials are transported by wind pipelines. - 5.Secondary mixing: The ultra-finely pulverized material is transported to the bin to be batched, and the material enters the computer-controlled secondary batching scale through the bin discharger and enters the feed mixer after automatic weighing according to the formula requirements.
Liquid raw materials are added during the mixing process (grease) and 5% water, the effective mixing time of each batch is 4 minutes. Part of the mixed raw materials go to the granulation process, and some of the mixed products enter the feed extrusion process.
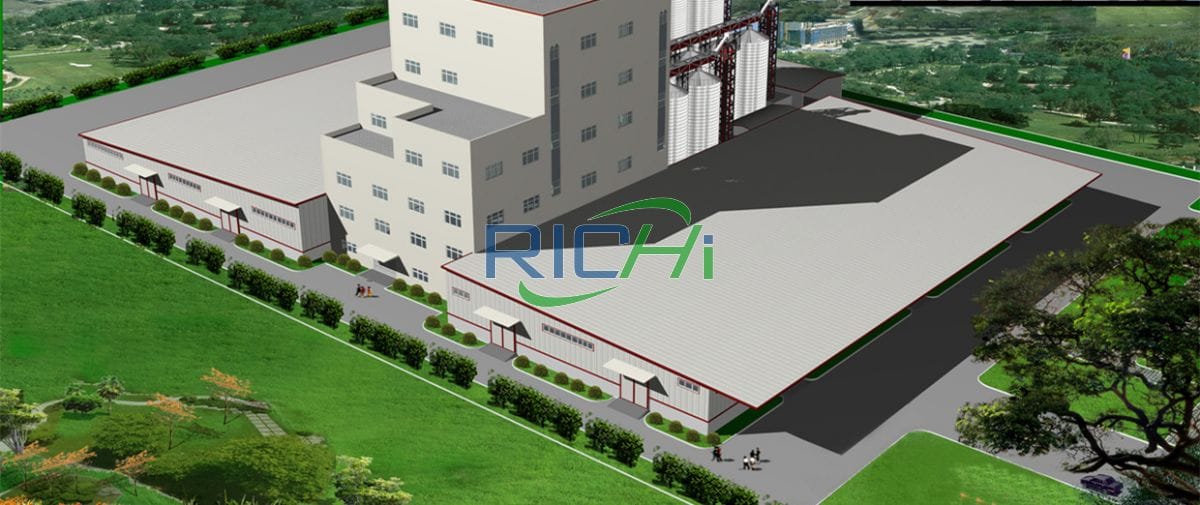
- 6. Pelletizing: Put the mixed raw materials into the shrimp feed pellet machine, adjust the temperature of the material to 80-85℃ through steam, and the water content of the material is about 15%, and then pass through the shrimp feed pellet mill to make pellets with a specified pellet size. This is one of the most critical processes in the 25t/h aqua feed production line.
- 7. Maturation and cooling: The hot granulated shrimp feed from the shrimp feed granulator enters the stabilizer evenly, and is built into a stable container heated by a spacer. It can keep warm for a certain period of time by using the temperature when the pellets are released from the mold, so that the shrimp feed can be further matured.
When the accumulation reaches a certain height and keeps warm for a certain period of time, the material level sensor of the silo generates a signal, which makes the hydraulic cylinder push the crank connecting rod mechanism to reciprocate, the flaps rotate around their respective axes, and the materials fall from the gaps between the flaps, the pellets enters the pellet cooler evenly.
After the feed pellet is filled with the cooling chamber, the material touches the pellet feed level device, and the motor is connected to drive the discharge mechanism to work and discharge.The cooling is air-cooled, using air as the heat exchange medium for heat exchange, and the heat is taken away by the air. Part of the cooled feed pellets enters the screening process, and part of it enters the crumbling process for finished powder. - 8. Screening: The feed pellets passes through the vibrating screen to remove the broken pellets that do not meet the requirements. In this 25t/h aqua feed production line, the pellets size of 1.0-1.2mm is qualified, and the unqualified product enters the granulation process again.
- 9. Finished product packaging: the finished product is packed into the warehouse and stored for sale;
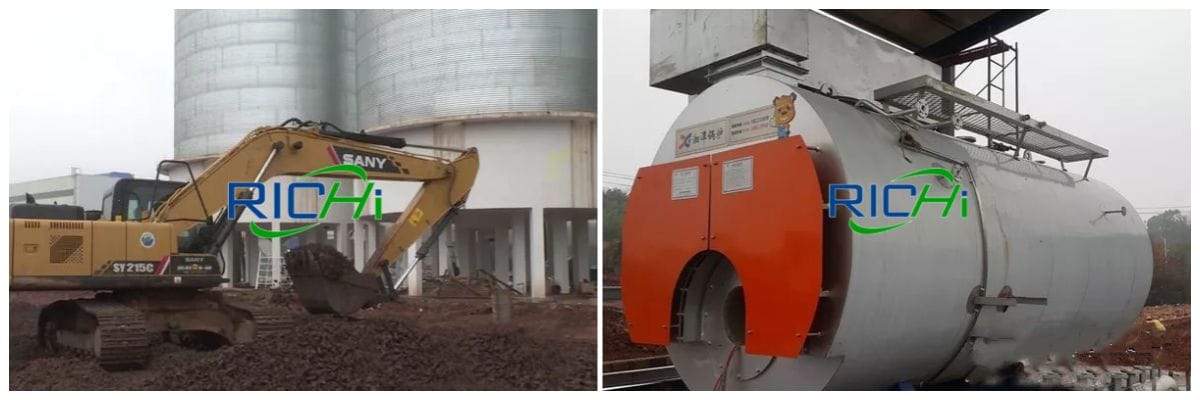
Powder feed production:
In this 25t/h aqua feed production line, powder feed processing is mainly for premix and some special aquatic feed processing
- 11. Crumbling: The cooled pellets passes through the pellet crumbler to make the size of the feed pellets finer.
- 12. Screening: The feed pellets passes through the vibrating screen to remove unqualified pellets. The powder material with a size of 0.1mm, 0.3mm, and 0.5mm is qualified, and unqualified products are re-entered into the granulation process.
- 13. Finished product packaging: the finished product is packaged into the warehouse and stored for sale;
Extruded feed production:
- 14. Expansion: The material from the secondary mixing section is added with 25% water, heated to 85℃ by high-temperature steam for gelatinization, and a full-structure matrix is produced in the extruded pellets containing soluble sugar and fiber during the process, which is The particles increase in size and become porous, allowing more fat to be absorbed. (Related product: floating fish feed machine)
- 15. Drying: The moisture content of the extruded pellets is higher than the moisture content specified in the product specification, so it needs to be dried in a drying oven. The drying temperature is controlled at 100℃ and the drying time is controlled at 30 minutes. The drying oven in the 25t/h aqua feed production line volatilizes the excess moisture in the material through electric heating, and finally makes the moisture content of the product reach the specified standard.
- 16. Cooling: The extruded granules enter the feed cooler for cooling, the feed temperature is reduced from 50-60℃ to normal temperature, and the cooling is air-cooled, using air as the heat exchange medium for heat exchange, and the heat is taken away by the air.
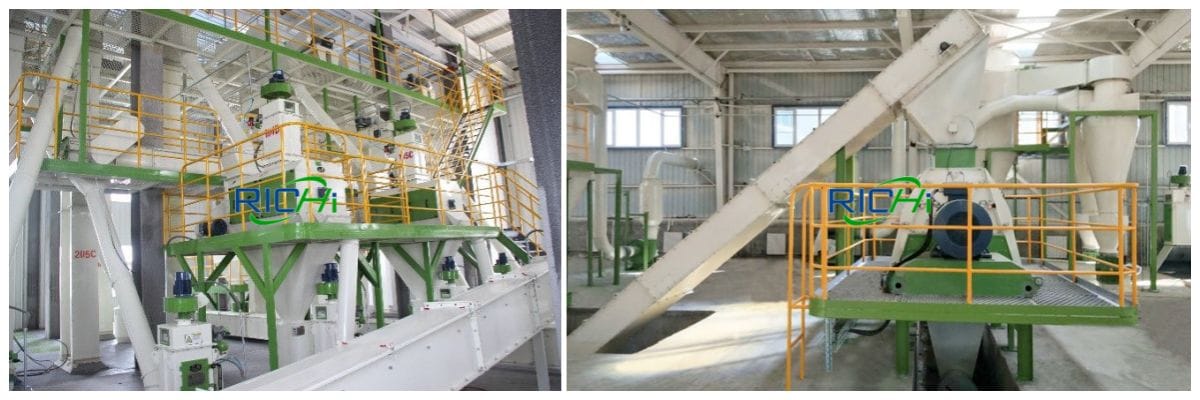
- 17. Vacuum spraying: The feed enters the vacuum spraying mixer after being weighed. During the mixing process, the vacuum pump vacuumizes the mixer to discharge the air in the mixer. At the same time, the air trapped in the micropores inside the pellet feed is also sucked out.
When the set vacuum requirement is reached in the mixer, a certain proportion of soybean oil is evenly sprayed on the pellet surface and mixed thoroughly. After the mixing is completed, open the valve of the vacuum mixer and release the vacuum. Under the action of the external atmospheric pressure, the liquid penetrates into the micropores of the pellets and replaces the air in the original internal spaces of the pellets. - 18. Screening: The puffed feed pellet passes through the vibrating sieve to remove the particles that do not meet the requirements. In this 25t/h aqua feed production line, the puffed pellets are 1.0mm-4.0mm as qualified, and the unqualified products enter the crushing process again.
- 19. Packaging of finished products: The finished products are packaged into storage and stored for sale.
Equipment for 25 t/h aqua feed production line
Device Name | Model | QTY |
---|---|---|
Boiler | 4t | 2 |
Scraper Conveyor | TGSU25 | 8 |
Scraper Conveyor | TGSU20 | 4 |
Pulse dust collector | LNGM18 (24 barrels) | 3 |
Pulse dust collector | TBLMY9 | 2 |
Pulse dust collector | LNGM36 | 2 |
Bucket elevator | TDTGK40/23 | 7 |
Bucket elevator | TDTGK50/23 | 7 |
Cylinder initial cleaning | SCY100 | 3 |
Permanent magnet cylinder | TCXT25 | 6 |
Water Drop King Crusher | 968-111-160KW | 3 |
Impeller automatic feeder | TWLY25X44 | 3 |
Big warehouse machine | TWLL32 N 2.5KW | 13 |
Big warehouse machine | TWLL25 1.5KW | 7 |
Small delivery machine | TWLL20 | 3 |
Small material adding machine | SBLMa4 | 3 |
Twin-shaft paddle type high-efficiency mixer | SLHSJ1.0 | 2 |
Material sealing screw conveyor | TLSSF32 | 3 |
Superfine Pulverizer | SWFL110 | 2 |
Feeding auger | TWLL16 | 2 |
Shrimp pellet machine | SZLH858 | 2 |
Ordinary feed pellet machine | SZLH520 | 2 |
Horizontal fish feed dryer | SWDQ4 | 1 |
Counterflow cooler | SKLN16X16 | 2 |
Cooling fan | 11KW | 2 |
Crumbler | 24X165 | 2 |
Air compressor | 22KW | – |
Twin-screw extruder | H156X2 | 2 |
Drying box | H156X2 | 2 |
Vacuum spraying | PTZL3000/PTCL3000 | 2 |
Shrimp pellet machine | SZLH768 | 4 |
170 Super micro (with bag dust removal) | SWFL170 | 8 |
Water drop type pulverizer (with bag dust removal) | SWFL170 | 4 |
Twin-shaft paddle type high-efficiency mixer | SLHS7 | 4 |
Crumbler (with bag dust removal) | 24×165 | 4 |
MCC Control Center | – | 1 |
Classifying sieve (with bag dust removal) | AHJH130×2C | 10 |
Packing Scale | DCS-50 | 10 |
Grease Storage Tank | 50m³ | 6 |
Product Index
- Crude protein (%)≥46.00
- Crude fiber (%)≤6.0
- Crude ash content (%)≤16.0
- Total phosphorus (%)≥1.20
- Crude fat (%)≥6.0
- Lysine (%)≥2.30
- Moisture (%)≤12.0
Public Works and Auxiliary Works
Water supply system
The fresh water consumption of the 25t/h aqua feed production line project is 60744.66t/a. The fresh water consumption of the expansion project is mainly used for the new employees’ domestic water, product water and production water.
At present, the diameter of the enterprise’s water supply pipe is ¢200mm, and the water supply pressure is 0.2MPa. There is enough water supply to meet the needs of the expansion project.

Drainage system
The “rain and sewage diversion” system is implemented in the factory area, and the rainwater is collected by the rainwater pipe network and discharged into nearby rivers.
The production wastewater of the aqua feed plant project is treated by the sewage treatment station in the factory, and the treated water is recycled, and about 30% of it is discharged every day.
Power supply system
The new power consumption of the expansion project is 8.25 million kWh/year, which comes from the local municipal power grid. The current factory has built a substation and distribution station, and is equipped with 4 transformers, and the power supply of the expansion project is directly connected to the existing one.
Gas supply
The natural gas of the 25t/h aqua feed production line project is transported to the location of the expansion project through the gas supply pipeline in the park.
In order to meet the water quality requirements of gas-fired steam boilers, each boiler is equipped with a set of fully automatic softening water treatment device, the system design output is 8m³/h, and each set of softening water treatment device is equipped with an ion exchange column and a set of Brine regeneration unit.
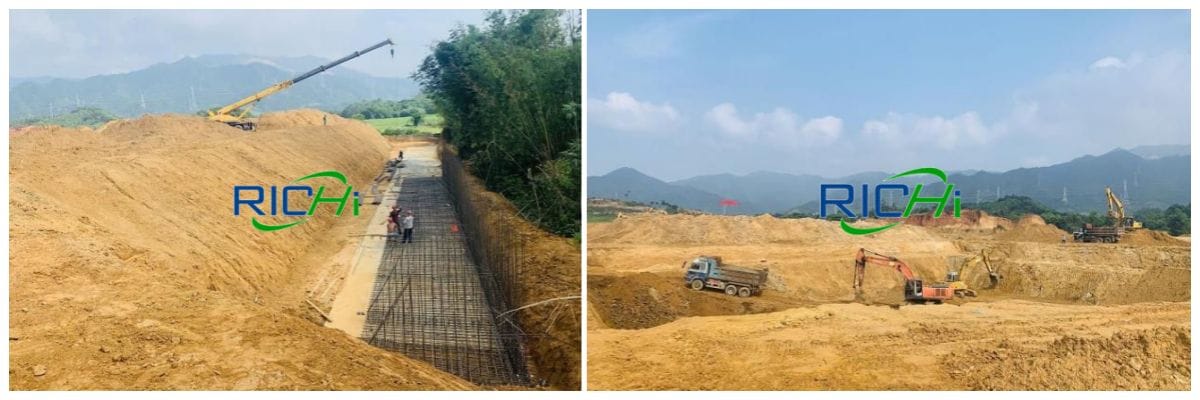
Relying relationship
The office building relies on the existing office building, the raw material warehouse and the finished product warehouse rely on the existing warehouse; the packaging workshop relies on the existing packaging workshop; the boiler room relies on the existing boiler room. The annual running time is 4992h, and the total steam output of the gas-fired boiler is 39936t/a.
- The steam consumption of the existing project is 9,800t/a, which can meet the annual production of 80,000 tons of aquatic feed for steam supply, and the remaining 30,136t/a.
- The steam consumption of the 25t/h aqua feed production line project is 28,000t/a, which can meet the steam supply of 190,000 tons of aquatic feed Need.
- The transformer relies on the existing 4 transformers with a total capacity of 6530kVA.
Main construction content
The west side of the aqua feed mill project is the boiler room, premix workshop, finished product workshop, comprehensive building, and the east direction is the premix packaging workshop, raw material workshop, feed engineering research and development center and dormitory.
Build Name | Area | Remarks |
---|---|---|
Boiler room | 184m² | One layer |
Premix Workshop | 658m² | One layer |
Premix packaging workshop | 799m² | One layer |
Finished workshop | 4905m² | One layer |
Raw material workshop | 8568.2m² | One layer |
Main Workshop | 3836m² | Six floors, height 37m |
Feed Engineering R&D Center | 2611m² | Four layers |
Comprehensive building | 1468m² | Three layers |
Dormitory building | 1147.84m² | Three layers |
Main Workshop No. 1 | 11203.09m² (new construction) | Six floors, height 37m |