Overview of 4 t/h aqua feed mill
The customer’s original engineering products are mainly pig feed, ordinary fish feed, chicken feed, duck feed, etc. In order to adapt to changes in market demand and increase the diversity of feed products, the customer invested 220,000 US dollars in the expansion of original project and product structure, to build a 4 tons per hour aqua feed mill.
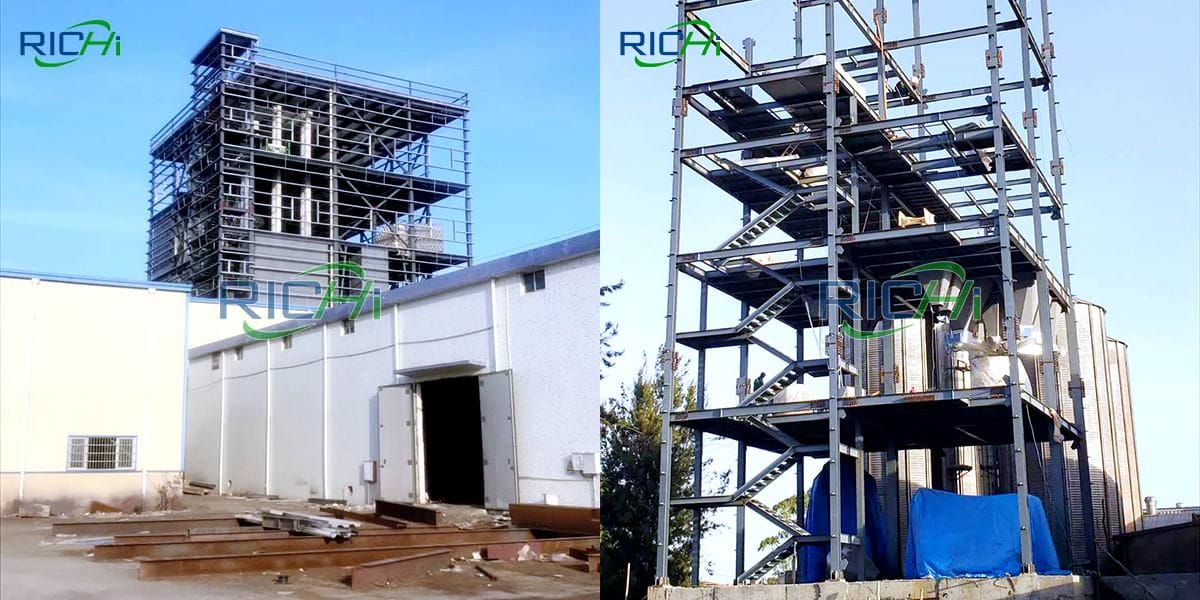
The specific content is:
- Reduce the existing granular pig feed products by 10,000 tons, and add pulverizers, fish feed extruders, dryers, coolers and other equipment at the same time, and build a new production line of 10,000 tons of extruded fish feed products. The total production capacity remains unchanged;
- In order to facilitate production, a powder premixing production line is added in the existing spare warehouse on the north side of the factory area to crush and premix raw materials with less demand such as methionine and lysine;
- For the convenience of production, four 150t small silos are newly added this time, and the small particle raw materials of the existing project are temporarily stored in the small silos and then enter the pulverizer;
- Due to the increase in the steam consumption of the whole plant after the completion of this technical upgrading project, the existing 2t/h gas-fired boiler will be replaced with a 4t/h low-nitrogen condensing waste heat recovery boiler. After steaming, remove the boiler in time.
This 4t/h aqua feed mill project belongs to the common expansion of feed factories, because many livestock and poultry feed factories have begun to set foot in the field of aquatic feed processing. Even if this customer originally processed fish feed, it is general sunken fish feed, which is not different from other livestock and poultry feed. (Related solution: 3-4t/h floating fish feed mill)
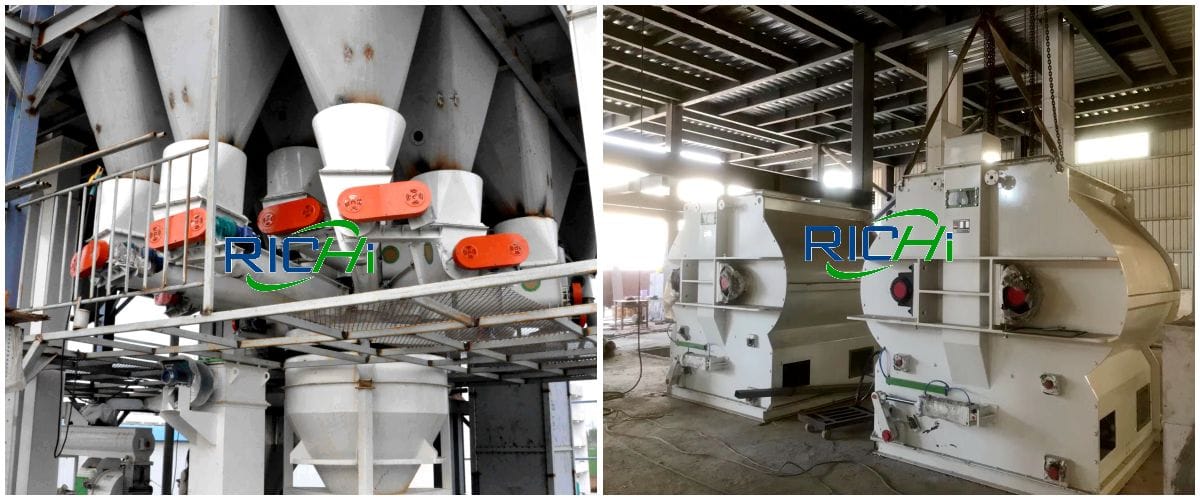
Therefore, the extruded process has been added, and the product types of extruded fish feed have been increased, which has brought considerable changes to customers. At present, the customer is also considering the possibility of producing suckling pig feed by extruding process.
Product plan and production scale
The existing engineering product is animal feed, with a production scale of 240,000 t/a. After the completion of this technical transformation project, the total production capacity of the whole plant will remain unchanged, and the product structure will be adjusted. The existing pig feed products will be reduced by 10,000 tons and replaced with extruded fish food.
Product name | Existing (million t/a) | After expansion (10,000 t/a) | Increase or decrease |
---|---|---|---|
Extruded fish Feed | 0 | 1 | +1 |
Common fish feed | 0.5 | 0.5 | 0 |
Pig pellet feed | 7 | 6 | -1 |
Powdered pig feed | 1 | 1 | 0 |
Layer feed | 8 | 8 | 0 |
Broiler Feed | 6 | 6 | 0 |
Duck feed | 1.5 | 1.5 | 0 |
Total | 24 | 24 | 0 |
Consumption of raw and auxiliary materials
The newly added extruded 4t/h aqua feed mill needs to use the following raw materials:
Name | Annual consumption (t/a) |
---|---|
Peanut Cake | 850 |
Flour | 900 |
Rapeseed Cake | 2500 |
Rice bran | 500 |
Wheat germ | 850 |
Soybean oil | 850 |
Fishmeal | 1700 |
Puffed soybeans | 1700 |
L-threonine | 50 |
L-lysine | 40 |
DL-methionine | 10 |
Choline chloride | 30 |
Salt | 20 |
(Note: Fish meal is a high-protein feed raw material that uses one or more types of fish as raw materials, after degreasing, dehydrating, and crushing. It is necessary to control the temperature and humidity of the storage space to prevent oxidative deterioration. The company has set up a heat-sensitive raw material room , using air conditioning to control the temperature at 20-25°C and the humidity at 40-50% to ensure the quality of fish meal)
Energy consumption of 4 t/h aqua feed mill
Name | Original | After expansion |
---|---|---|
Water | 7521.2t/a | 9270.2t/a |
Electricity | 11.3 million kWh/a | 13.3 million kWh/a |
Gas | 880,000 m³/a | 1.16 million m³/a |
Main aqua feed production equipment
This technical transformation project mainly adds extruded fish feed production line equipment, premix production line equipment and small silos, and replaces the existing gas boiler at the same time, while other equipment in the whole plant remains unchanged. (Related solution: 5t/h aqua feed plant)
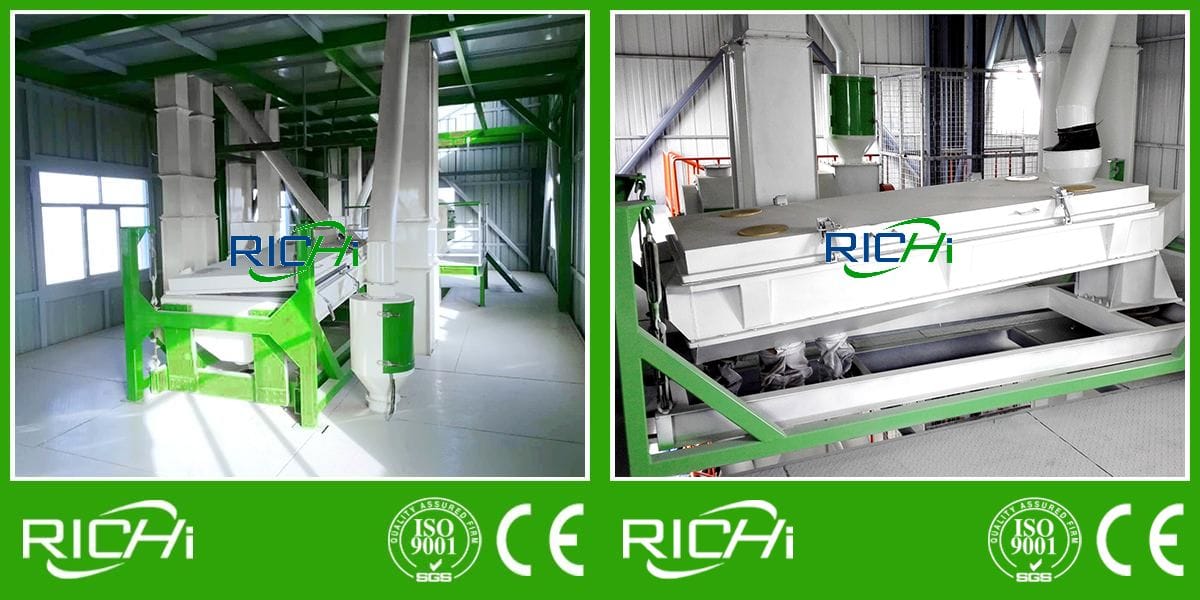
Newly added equipment for 4t/h aqua feed mill:
Name | Model and specification | Capacity | QTY |
---|---|---|---|
Scraper conveyor | LLCA100 | 30-40t/h | 1 |
Scraper conveyor | LLCA50 | 20-25t/h | 1 |
Permanent magnet cylinder | TCXT25 | 30-50t/h | 2 |
Bins for superfine grinding | 3m³ | 15-18t/h | 1 |
Vertical ultrafine pulverizer | LDSWFL180 | 10-15t/h | 1 |
Two-way feeding auger | TGSS25 | 15-20t/h | 1 |
High square sieve | AHCTS125×190 | 15-20t/h | 2 |
Bucket elevator | TDTG400×230 | 18-20t/h | 1 |
Bucket elevator | TDTG500×280 | 20-30t/h | 1 |
Closed air screw conveyor | AHSG200 | 10-15 t/h | 1 |
Store to be puffed | 15m³ | 12t | 1 |
Fish feed extruder machine | BCCH-125/20D | 8-12t/h | 1 |
Belt conveyor | B500 | 15-20t/h | 2 |
Rotary classifier | AHJH140*2C | 15-20t/h | 2 |
Grease Addition Tank | SYTV120 | 500kg | 1 |
Grease adding machine | SYTC300-F | 2-4t/h | 1 |
Finished product warehouse | 15m³ | 12t | 2 |
Double Scale Baling Scale | – | 12-20t/h | 1 |
Seam Conveyor Combination Machine | – | 10-15t/h | 1 |
Small Silo | 150t | – | 4 |
Low nitrogen condensing waste heat recovery boiler | WNS4-1.25-Q (LN) | 4t/h | 1 |
Labor quota and work system
This 4t/h aqua feed mill technical upgrading project has newly added 3 laborers, all of whom do not have board and lodging in the factory area.
After the completion of this technical transformation project, the running time of the existing project’s granular material preparation, powder material preparation, and mixing processes will remain unchanged, and the running time of the granulation cooling and packaging processes will be reduced.
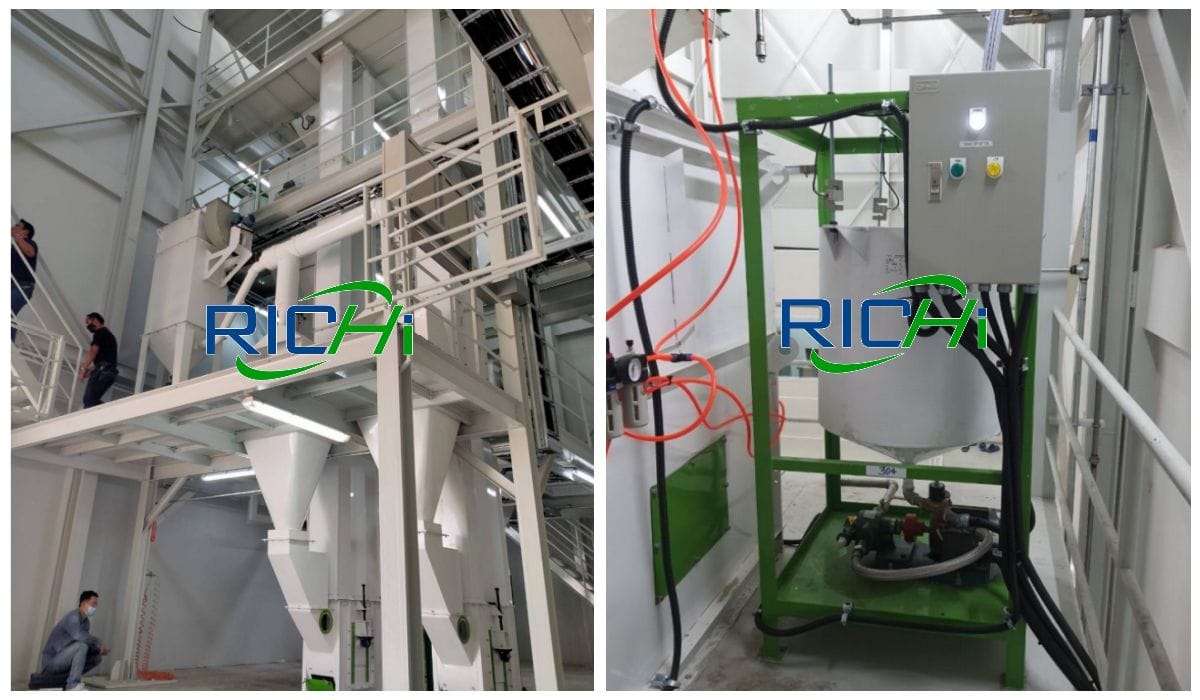
Engineering technical transformation
The technical renovation of the 4t/h aqua feed plant project does not add new workshops, and does not involve civil construction. The main content of the construction period is the installation of production equipment, environmental protection equipment, and pipelines.
(1) Technological transformation – extruded fish feed line
The production process of the 4t/h extruded fish feeds production line mainly includes the processes of granular material preparation, powder material preparation, material mixing, magnetic separation, crushing, screening, magnetic separation, extruding, drying, adding oil, cooling, screening, packaging and so on. (Related solution: 6t/h fish feed mill plant)
Among them, the processes of particle material preparation, powder material preparation, and material mixing rely on the existing project, and will not be introduced here. The new part of the production process is as follows.
①Magnetic separation and crushing
The material mixed by the existing engineering mixer is sent by the scraper conveyor to the permanent magnet cylinder for iron removal, and then sent by the scraper conveyor to the vertical shaft ultrafine pulverizer for crushing.
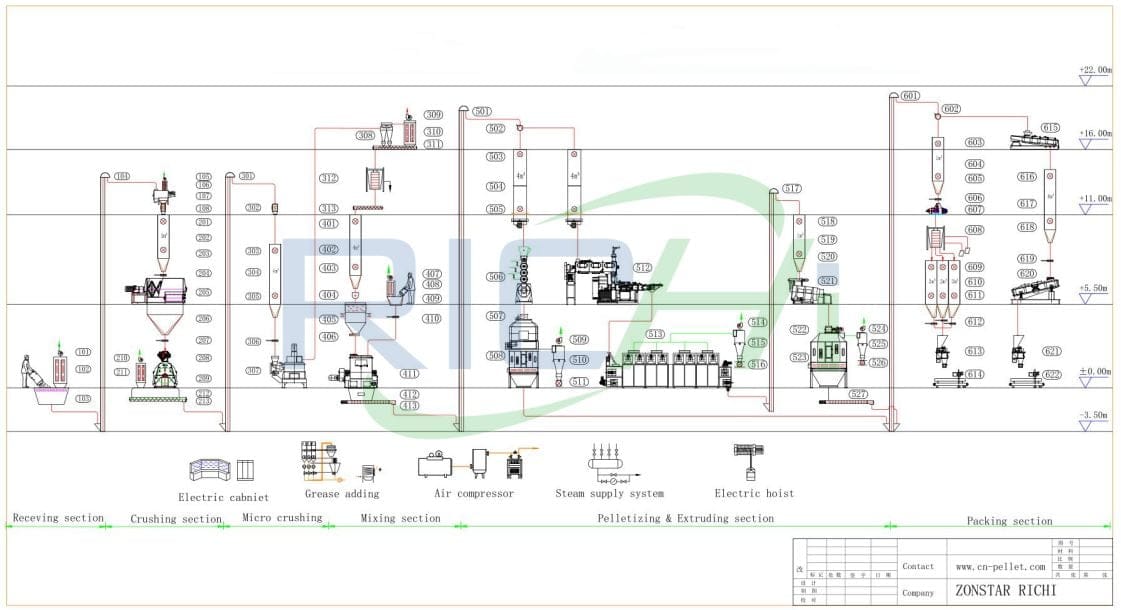
The vertical shaft ultrafine pulverizer is a vertical shaft reflective micro pulverizer, which can simultaneously complete the two processing procedures of micro pulverization and micro powder sorting.
It consists of a body, a frame, a feeding device, a crushing device, a discharge pipe, and a devices and motors. The material crushing process is sealed, and after the crushing is completed, it is sent to the high square screen by the screw conveyor and bucket elevator.
② Screening, magnetic separation
The materials are sieved through two-stage square sieves, and the materials with a particle size greater than 0.18mm (fineness of 80 mesh) are returned to the pulverizer for further crushing. The elevator is sent to the twin-screw fish feed extruder.
③Puffing
Before the material enters the extrusion process of aqua feed mill, the moisture content is about 10-12%. After the material is subjected to high temperature, high pressure, instant aging and shearing in the twin-screw extruder for fish feed, it is puffed into shape. (Hot products: floating fish feed machine)
④Drying, adding grease, cooling
The extruded fish feed enters the fish feed dryer through the chute for drying. The drying temperature is 100-125°C, the drying time is 20 minutes, and the moisture content of the material after drying is 9-11%. The drying process uses the steam provided by the gas boiler as the heat source, and the heating process is indirect heating.
The dried material is sent to the oil adding tank through the belt conveyor, and the oil is pumped into the tank. At this time, the temperature of the material is about 50-60°C. After that, the material is sent to the pendulum cooler through the elevator, and after cooling to 30°C, it is sent to the finished product warehouse by the bucket elevator and screw conveyor.
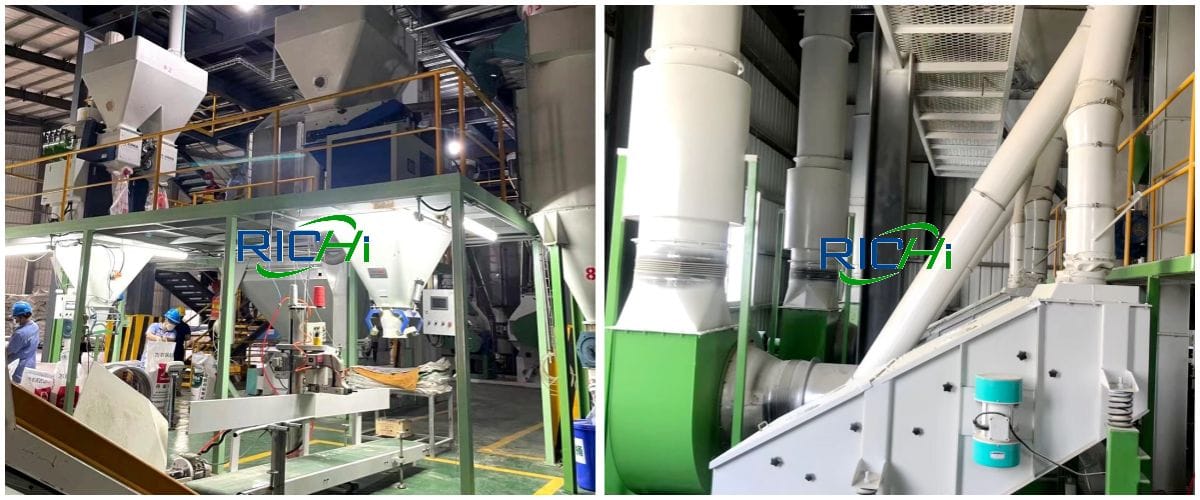
⑤ Screening and packaging
After the material enters the finished product warehouse, it is sent to the rotary grading screen by the screw conveyor, and the unformed powdery material is returned to the crushing process for further processing.
And the formed material is packed by the baler and put into storage for sale. During the production process of 4t/h aqua feed mill, the material conveying equipment and processing equipment are fully enclosed.
(2) Technical improvement – low nitrogen condensing waste heat recovery boiler
This technical upgrading project replaces the existing ordinary gas-fired boiler with a low-nitrogen condensing waste heat recovery boiler. The boiler is a variable frequency boiler, the main body adopts a two-pass wet back structure, and a two-stage energy-saving device is added at the rear.
The first stage is a finned tube type pressure-bearing economizer, and the second stage is an atmospheric condenser, which is also equipped with high-quality low-nitrogen.
The hot-air burner absorbs the sensible heat in the exhaust smoke at the tail of the boiler and the latent heat released by the condensation of water vapor through a high-efficiency condensing heat exchanger and an air preheater. And realizes continuous water supply by frequency conversion and combustion ratio adjustment by frequency conversion, to improve the thermal efficiency of the boiler and reduce the emission of pollutants.
We provided the customer with a new low-nitrogen condensing waste heat recovery steam boiler. According to the test data on the day of installation, after conversion, the emission concentrations of particulate matter, SO2 and NOx at the outlet of the exhaust pipe of the low-nitrogen condensing waste heat recovery boiler were 4.41mg/ m³, 6mg/m³, and 27.4mg/m³, all of which can meet relevant environmental protection requirements.
(3) Technical transformation – small particle material silo
This 4t/h aqua feed mill project adds 4 small silos for the temporary storage of small particle materials. Dust particles are generated at the balance port on the top of the silo. (Hot products: sinking fish feed machine)
Note:
- In the extruded fish feed workshop, a new vertical shaft ultrafine pulverizer, 3 high square sieves, and 2 rotary grading sieves will be added to the project, and the production process will be airtight.
- The project adds 2 finished product warehouses in the extruded fish feed workshop for temporary storage of extruded feed.
- In this technical upgrading project, 4 small silos (1#, 2#, 3#, 4#) were added next to the large silo for the temporary storage of small granular materials in the whole plant. After entering the pulverizer, after the reconstruction is completed, dust particles will be generated at the balance port on the top of the silo when the small particle material enters and exits the small silo.
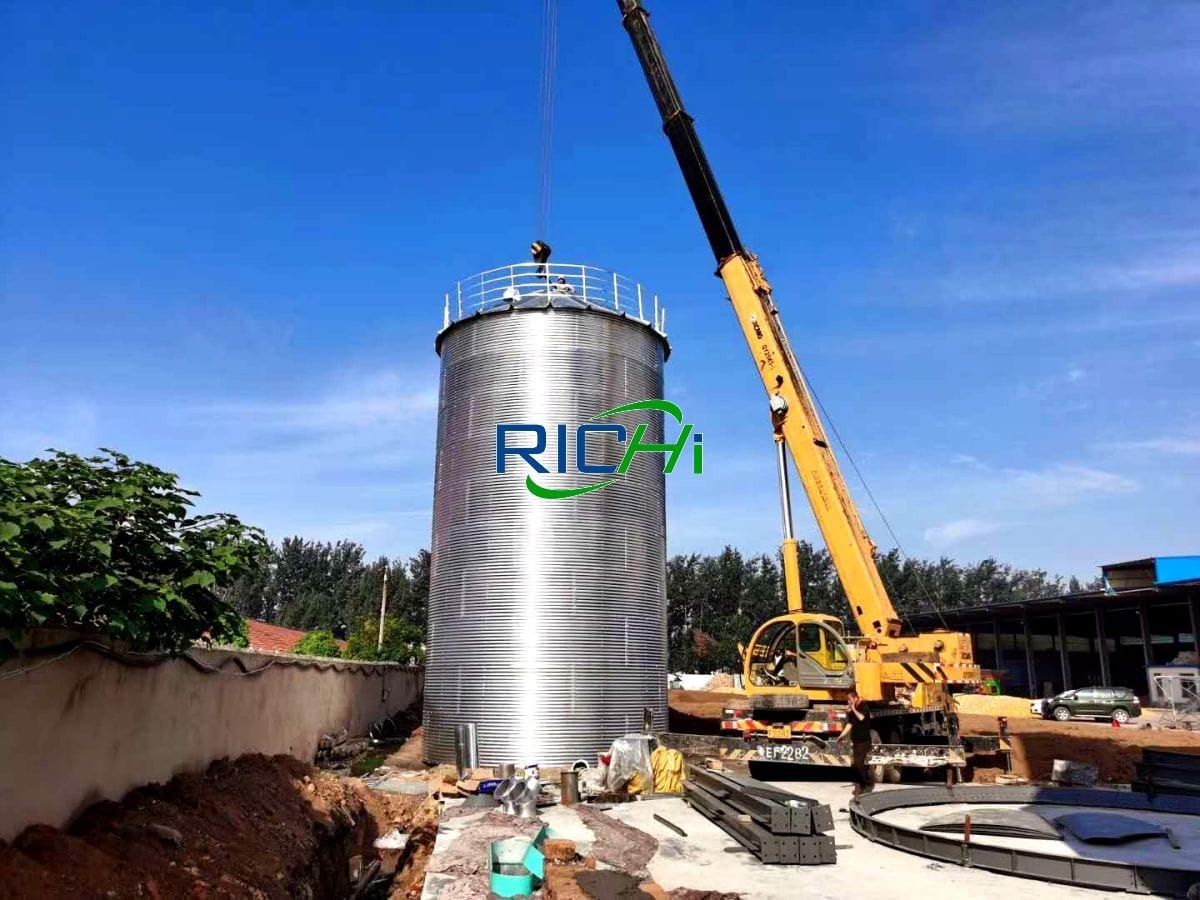
- This 4t/h aqua feed mill project replaces the existing ordinary gas-fired boiler with a low-nitrogen condensing waste heat recovery boiler to provide hot steam for the whole plant. The amount of steam used in tempering granulation, puffing, and drying processes is 50kg/t-product, 100kg/t-product, and 300kg/t-product respectively.
The dry products are 210,000 tons, 10,000 tons, and 10,000 tons respectively. After the technical transformation is completed, the total steam consumption of the whole plant will be 14,500 tons, which is an increase of 3,500 tons/a compared with the existing project, and the natural gas consumption of gas-fired boilers will be about 1.16 million tons. m³/a, an increase of 280,000 m³/a compared with the existing project.
Construction and layout
(1) Construction content
The construction content of this technical transformation project mainly includes extruded fish feed workshop and premix workshop, as well as supporting environmental protection projects.
①The main project:
- Extruded fish feed workshop: a building area of 300m², a steel structure workshop, located on the east side of the raw material warehouse;
- Pre-mixing workshop: with a construction area of 800m², the steel structure workshop is located in the warehouse on the north side of the factory area.
②Public works:
- Water supply: water supply pipe network, relying on the existing
- Power supply: power supply pipe network, relying on the existing
- Gas supply: gas supply pipeline network, relying on the existing
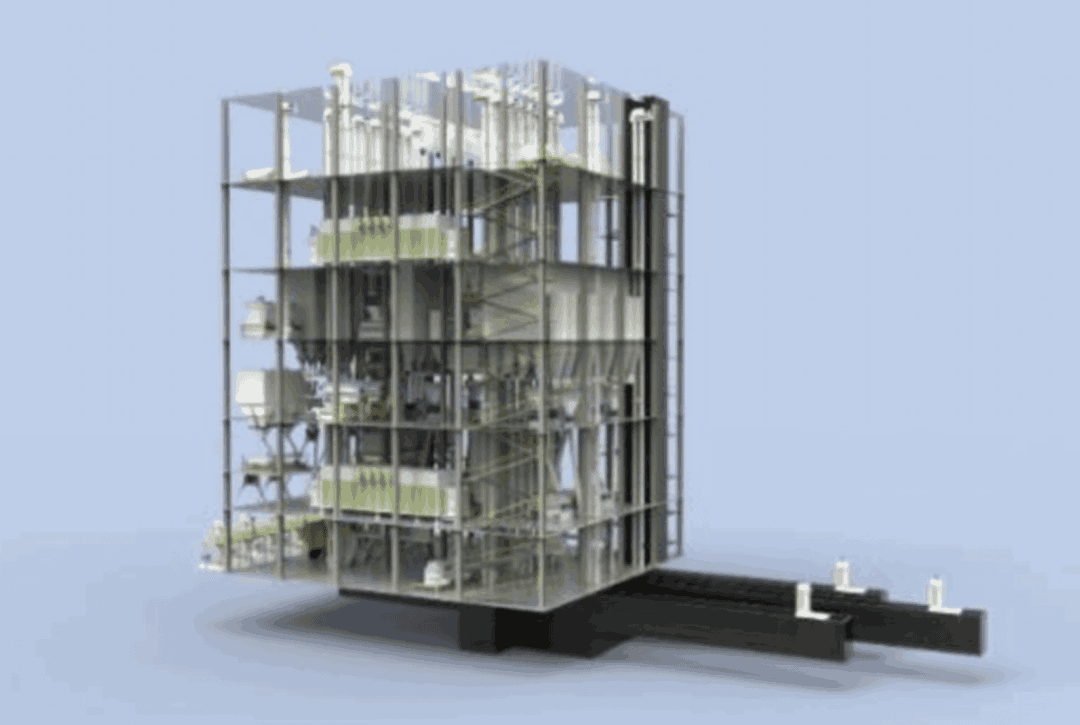
③Environmental protection project:
- Exhaust gas: pulse bag filter, cyclone dust collector, settling chamber, water spray, low-temperature plasma purification device, which are newly built;
- Wastewater: septic tank, relying on the existing;
- Sewage treatment station: newly built
- Solid waste: general solid waste warehouse (40m²) & hazardous waste warehouse (10 m²), relying on the existing;
- Noise: indoor layout, shock absorption foundation, muffler, etc., belong to new construction.
(2) Feed plant layout
The factory area where the 4t/h aqua feed mill project is located has a rectangular shape as a whole, long from north to south and wide from east to west. The gate is located on the south side of the factory area for people to enter and exit. The roads in the factory area are smooth, which is convenient for logistics transfer. After the completion of this technical transformation project, the spare warehouse on the north side of the factory area will be changed into a premix workshop and a premix warehouse, and some raw material warehouses will be used as extruded fish feed workshops, and other buildings will remain unchanged from the existing project.
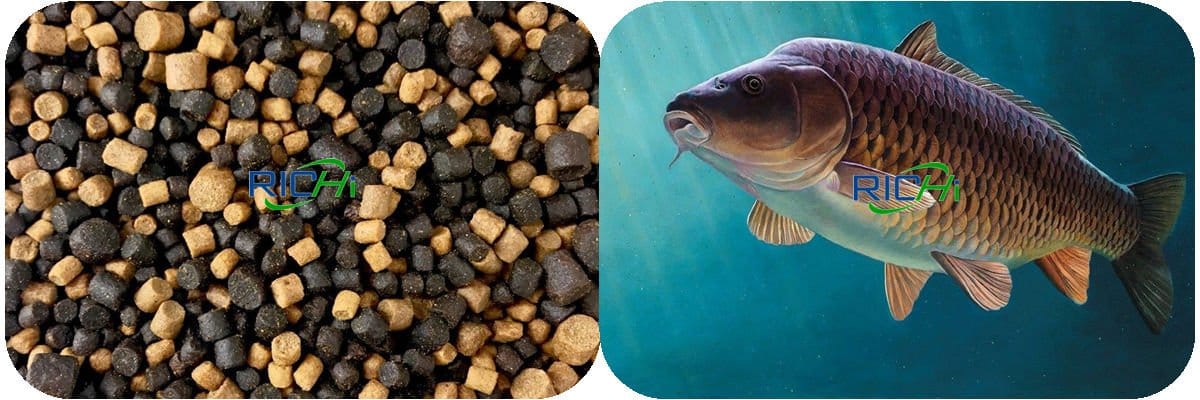
The factory area is divided into a living area and a production area. The living area is located on the south side of the factory area, including offices, dormitories, restaurants, etc.; the production area is located on the north side of the factory area. From south to north, they are: finished product warehouse, main workshop, puffed fish feed workshop And raw material warehouse, heat-sensitive raw material room, maintenance room, boiler room, premix workshop and premix warehouse, etc. The layout of the project is reasonable, which is convenient for the flow of people and logistics.
(3) Geographical location and surrounding environment
The site selection and surrounding environment of the project have the following characteristics:
- The project site occupies an industrial land, and this project does not belong to the prohibited and restricted projects in the agglomeration area.
- The project site is located in an industrial agglomeration area with relatively complete infrastructure, which is convenient for project construction.
- The project construction area belongs to the SO2 total control area. After the 4t/h aqua feed mill project removes the existing gas-fired boiler of the enterprise and replaces it with a 4t/h low-nitrogen condensing waste heat recovery boiler, the SO2 emission increases, but the natural gas used in the project is clean energy, which meets the Local regulations on the use of clean fuels.