Origin of 5 t/h aqua feed Project
The client of 5t/h aqua feed plant is a feed production enterprise integrating R&D, production and sales. The customer’s existing project has set up 2 fish feed lines (capacities of 50000 t/a and 10,000 t/a) and 4 prawn feed production lines (4 production lines of 3750 t/a), with a total annual output of 15,000 fish feed t/a, shrimp feed 15,000 t/a. The existing project uses two 6t/h coal-fired boilers.
In order to support the nearby and convenient development of the local agricultural industry and better serve agriculture, the client company continued to increase capital and expand production, introduce new production technology and equipment, improve market competitiveness, and invest 3 million US dollars to build an expansion facility with an annual output of 25,000 tons of aquatic feed mill project.
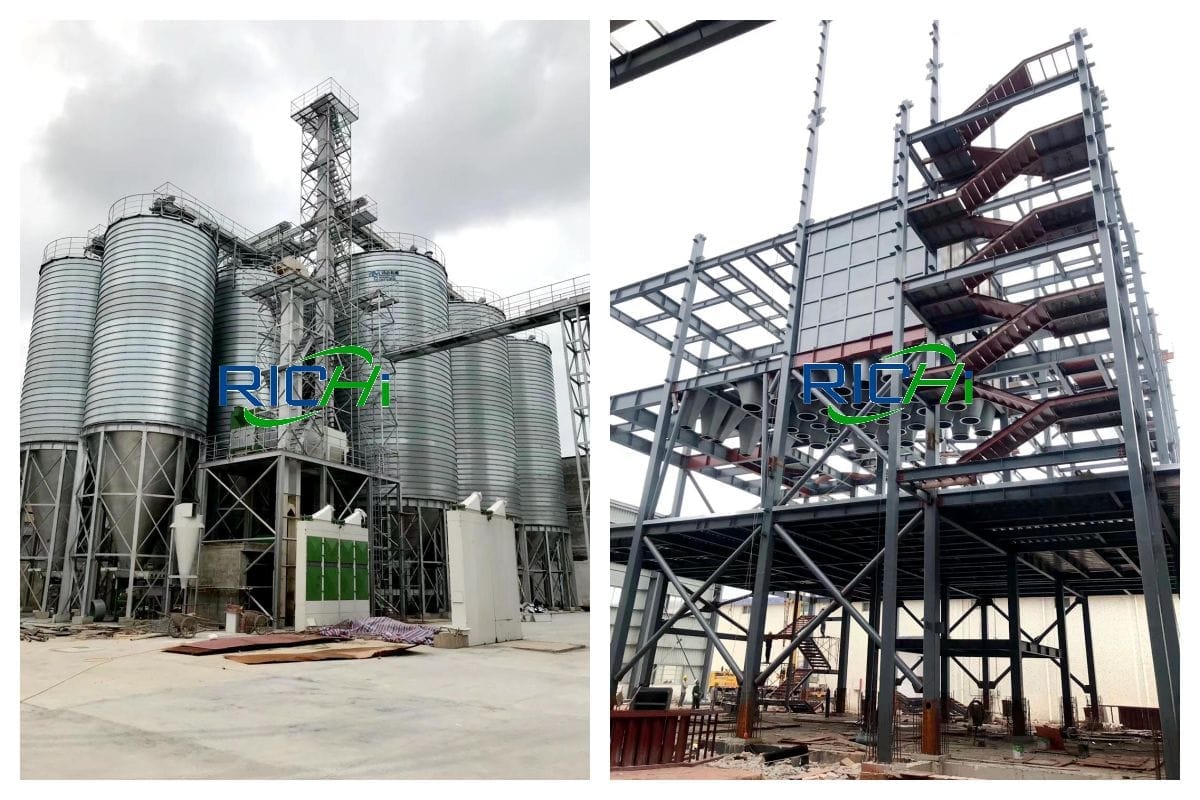
The project is located in the customer’s existing factory area, and no new land is required. After the project is completed and put into operation, it can form an annual production capacity of 75,000 tons of aquatic feed.
This project is a typical expansion project of an aquatic feed factory. On the basis of good market prospects and better income, the customer chooses to expand production capacity and enhance its own market advantages
. As of 2022, the feed company has been established for 15 years. It is worth mentioning that the client’s original project was also undertaken by us. During this period, the equipment of this project has been running stably, meeting and exceeding the client’s expectations for the quality of aquatic feed processing.
In addition, during the operation of the 5t/h aqua feed plant project, we provide customers with accessories and a full set of after-sales service for all products. In 2018, the client asked for an expansion project, which is how this project came about.
Product plan
The customer of this aqua feed mill project purchases raw materials (corn, soybean meal, flour, peanut bran, rapeseed meal, barley, fish meal, soybean oil, fish oil, lecithin, etc.) , drying, cooling, screening, packaging and other processes to produce the final finished aquatic feed.
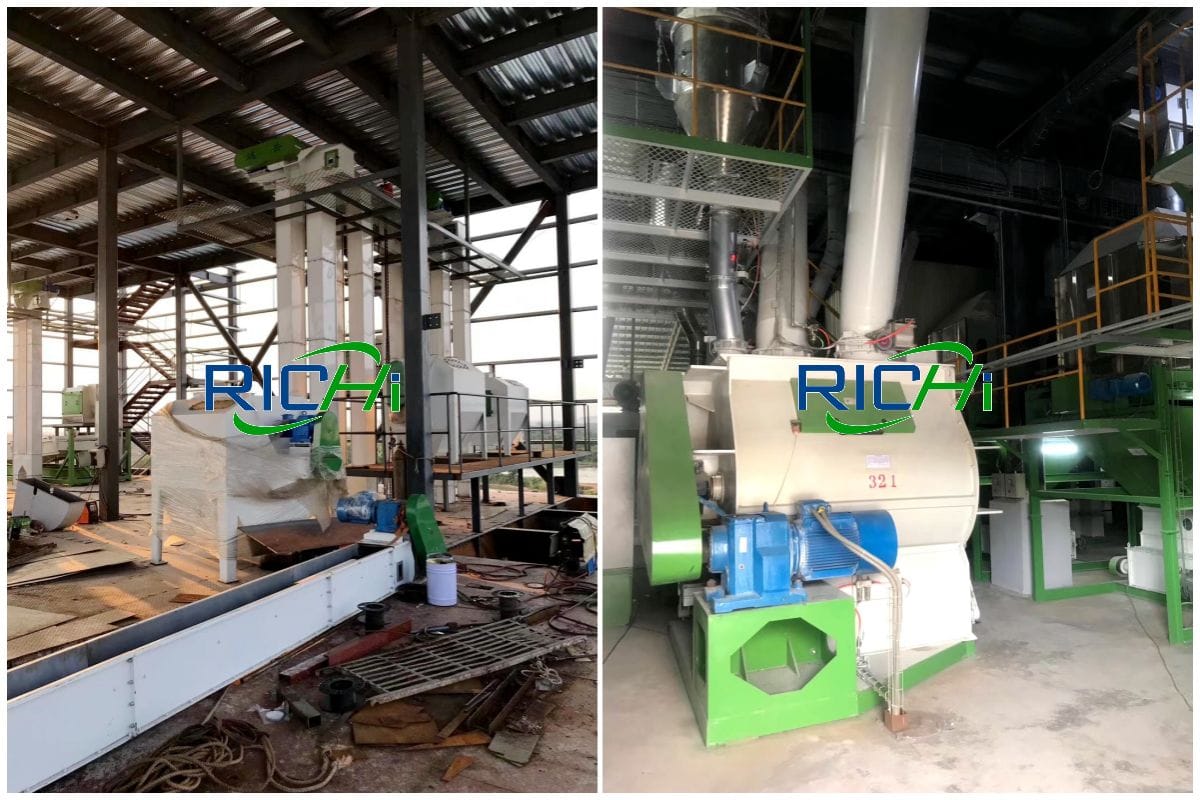
According to the difference of product processing technology, the products can be divided into fish feed products (extrusion process products) and shrimp feed products (granulation process molding), and the raw materials used for the two products are the same.
The existing project has a total of 4 shrimp feed production lines (each with a production capacity of 3,750t/a, a total of 15,000t/a), and 3 fish feed pellet processing lines (with a production capacity of 5,000 t/a, 10,000 t/a, and 20,000 t/a , a total of 3.5t/a).
This expansion 5t/h aqua feed plant project continues to use the fish feed production process of the existing project, adding 3 new fish feed making lines (capacities of 5,000 t/a, 10,000 t/a, and 10,000 t/a, totaling 2.5 t/a), This expansion project will produce 25,000 t/a of feed per year.
Product Category | Main Craft | Current Capacity | Expansion of production capacity |
---|---|---|---|
Shrimp Feed | Pelletization process | 15000 | 0 |
Fish Feed | Puffing process | 35000 | 25000 |
Total | / | 50000 | 25000 |
Fish feed production line setup
(1) Existing feed production line
According to different customer formulas, the existing project has a production workshop with an annual output of 50,000 tons of aquatic feed, including an annual output of 15,000 tons of prawn feed (4 production lines for prawn feed), and 35,000 tons of fish feed per year (3 fish pellet feed production lines).
Production line | Capacity t/a |
---|---|
Fish food production line 1# | 5000 |
Fish feed processing line 2# | 10000 |
Fish feed manufacturing line 3# | 20000 |
Shrimp Feed Production Line 1# | 3750 |
Shrimp Feed Production Line 2# | 3750 |
Shrimp feed production line 3# | 3750 |
Shrimp Feed Production Line 4# | 3750 |
(2) New production lines for 5 t/h aqua feed Factory
Production line | Capacity t/a |
---|---|
Fish feeds line 4# | 5000 (1t/h) |
Fish feed produce line 5# | 10000 (2t/h) |
Fish feeds production line 6# | 10000 (2t/h) |
Construction content
The content of this 5t/h aqua feed plant project is: to expand a workshop in the company’s originally reserved and planned workshop plot (the new workshop construction does not need to apply for a new construction land), design and install three feed production lines, and invest about 3 million US in the expansion of the aqua feed production line (including environmental protection equipment), and the designed production capacity is 25,000 tons/year.
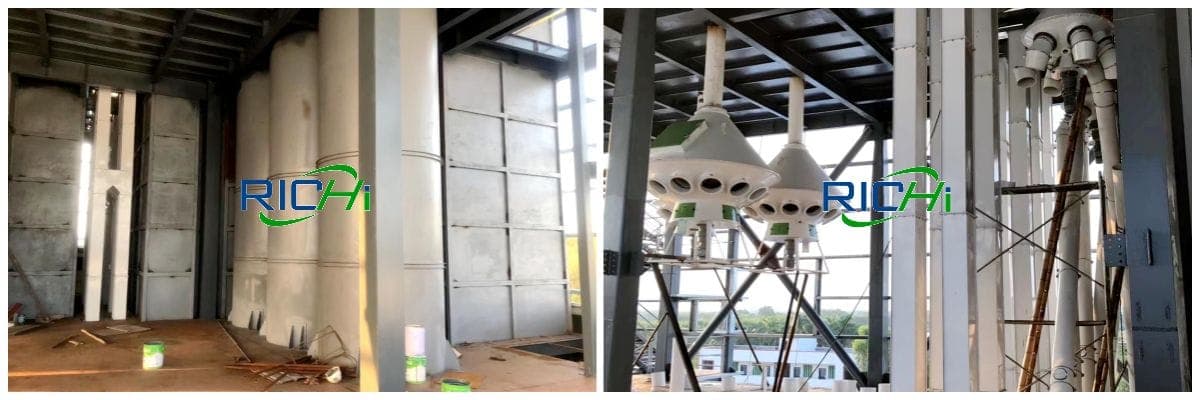
- Aquatic feed production line: A new feed production workshop is built, and three fish aquatic feed production lines are set up. The annual output of aquatic feed in the expansion project is 25,000 tons/year. After the expansion, the total production capacity of the whole plant will reach 75,000 tons/year.
- Heating Boiler: A 15t/h biomass briquette fuel steam boiler is installed in the existing project, and a spare 6t/h biomass briquette fuel boiler is installed; a 10t/h biomass briquette fuel boiler is newly added steamer.
- Raw material storage: A raw material warehouse is set up on the 3F of the production workshop, and three oil storage tanks with a total of 270m³ are installed; a raw material warehouse is added at the 3F of the new workshop, and three oil storage tanks with a total of 150m3 are added.
- Finished product storage: The existing production workshop 1F is connected to the finished product warehouse.
- Temporary storage of hazardous waste: set up a temporary storage room for hazardous waste (continue to use the existing temporary storage room for hazardous waste).
Labor quota and production plan
The number of employees in the existing project is 70, all of whom are boarding and lodging in the factory. This expansion 5t/h aqua feed processing project will add 30 new employees, all of whom belong to the production line staff.
According to the production rules of the industry, the feed industry will be divided into peak production season and off-season production every year.
The customer company implements three shifts per day (about 8 hours per shift) during the peak production season, and continuous production for 24 hours a day; production off-season (November-April of the next year, off-season during the production period of 150 days), one shift per day is implemented, and the daily production is 8 hours.
A total of 300d/a is produced throughout the year, and the total production time is 4800h/a. (Related solution: 6t/h fish feed mill plant)
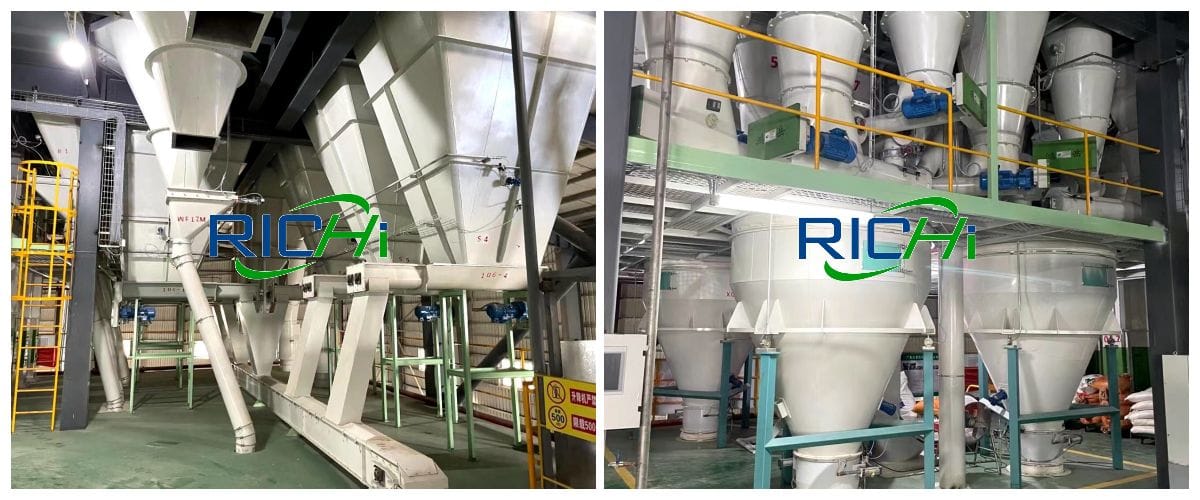
After the expansion of this project, the production plan of the expansion project is the same as the existing production plan, that is, the annual production is 300d/a, and the total production time is 4800h/a.
Main raw material consumption
The following is only the consumption of raw materials for the new 5t/h aqua feed plant. The raw materials of this project are mainly packed in 40kg bags, and only liquid raw materials such as soybean oil, fish oil, and phospholipids need to be stored in storage tanks.
Raw materials | Amount (t/a) | Maximum storage capacity (t) |
---|---|---|
Corn | 7534 | 100 |
Soybean Meal | 3767 | 300 |
Flour | 5023 | 200 |
Peanut bran | 1507 | 100 |
Rapeseed Meal | 1507 | 100 |
Wheat | 2009 | 100 |
Fishmeal | 1256 | 500 |
Soybean oil | 804 | 93 |
Fish oil | 402 | 218 |
Phospholipids | 904 | 318 |
Other premixes (vitamins, trace elements, etc.) | 402 | 500 |
Energy consumption
The biomass briquette fuel of the 5t/h aqua feeds plant project comes from the remaining agricultural and forestry straw, excluding waste furniture, etc.
Raw materials | Amount (t/a) | Maximum storage capacity t |
---|---|---|
Biomass briquette | 6464 | 400 |
There is a total of 1 15t/h biomass briquette fuel boiler in the existing project production workshop. This expansion project plans to add 1 10t/h biomass briquette fuel boiler. The calorific value of the material briquette fuel is calculated according to 16780MJ/t (equivalent to 4.01 million kcal/t). The amount of biomass briquette fuel after the expansion of the project is as follows.
Heat process | Heating objects | Amount t/a |
---|---|---|
Cooking | Fish feed products (25,000 t/a) | 923 |
Puffing | Fish feed products (25,000 t/a) | 2462 |
Drying | Fish feed products (25,000 t/a) | 3078 |
Main production equipment
The existing equipment of the 5t/h aqua feed processing plant project includes 3 sets of twin-screw fish food extruders, ring die granulator, superfine pulverizer, hammer mill, high-efficiency mixer, cyclone dust collector, batching auger, square screen, scraper conveyor , belt conveyor, dryer, vacuum spraying machine, automatic plastic film sealing machine, palletizing robot, intelligent automatic packaging machine, 15t/h biomass boiler, 6t/h biomass boiler (standby), counterflow cooler machine, etc.
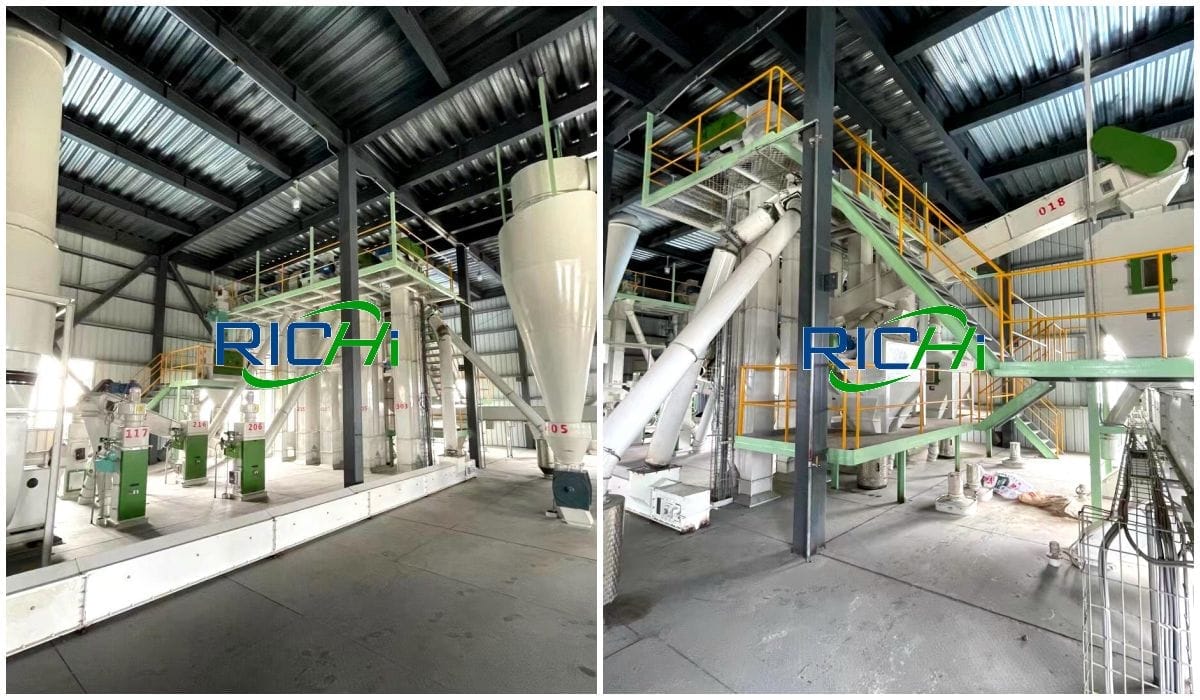
The main equipment of the new project is as follows:
Device Name | Model/Specification | QTY |
---|---|---|
Twin-screw extruder | SJPS166*2 | 2 |
High square sieve | TLSS 16 | 9 |
Particle Classification Sieve | ESFG1*6*83 | 2 |
Bucket elevator | TDTG50/32 | 6 |
Vertical ultrafine pulverizer | LDSWFL150 | 4 |
Three-axis modulator SPTZ45 | SPTZ45 | 2 |
Belt Type Circulation Dryer | SDZB3000-16 | 2 |
Dust collector | TBLMy156 | 4 |
Flip cooler | SLNF22X22 | 4 |
Twin Shaft Mixer | TDYHS3.0 | 2 |
Palletizer | LP130 | 2 |
10T/H biomass boiler | SZL10-1.25 | 1 |
Process flow design of 5 t/h aqua feed plant
(1) Raw material processing stage:
The raw material processing stage mainly includes raw material processing procedures such as primary cleaning of raw materials, batching, coarse crushing, screening, primary mixing, ultrafine grinding, and secondary mixing.
The raw and auxiliary materials are lifted to the 6th floor of the production workshop through the airtight conveyor belt, and then the materials are transported to each production equipment through the airtight conveyor belt. The location of the production equipment is set according to the full use of gravity, and the first process equipment is prevented from being relatively high. The process equipment carried out is kept at a relatively low position.
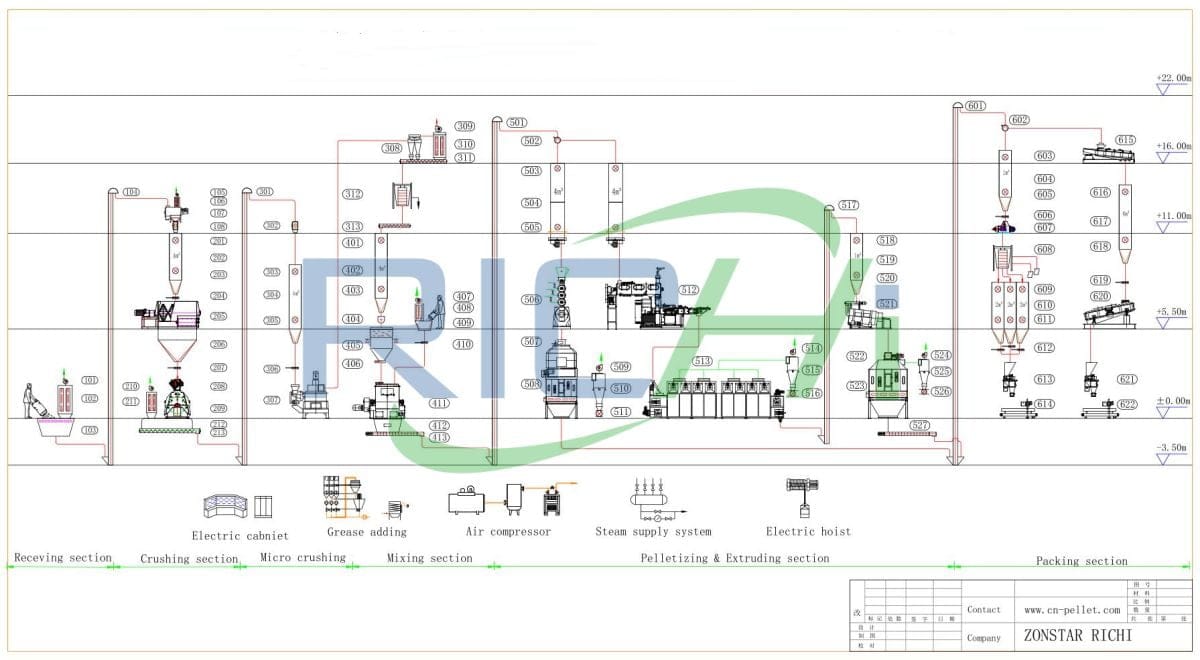
① Raw material reception and initial cleaning: Raw materials such as soybean meal are sent to the bucket elevator through the scraper conveyor, lifted to the cleaning sieve to remove sundries, and then the ferromagnetic sundries are removed by the permanent magnet cylinder for preliminary cleaning of raw and auxiliary materials, after distribution The machine is assigned to the corresponding batching bin located on the top floor of the production workshop.
② Batching and coarse crushing: After weighing and batching various raw materials through computer control, the materials are sent to the bucket elevator through a fully enclosed conveyor belt scraper conveyor, and after being lifted to the bin to be crushed, the materials are discharged into the grinder for coarse crushing is carried out, and the material is crushed into fine powder. (Related solution: 20t/h fish feed production plant)
③ Screening and primary mixing: Coarse materials are formed from coarsely crushed materials, and the powder materials are transported to high square sieves, rotary vibrating sieves or grading flat sieves for screening by belt conveyor according to 5t/h aqua feed production requirements. To the auger conveyor, sent to a mixing bin for uniform mixing. The process is all closed and automated to prevent dust from spilling out.
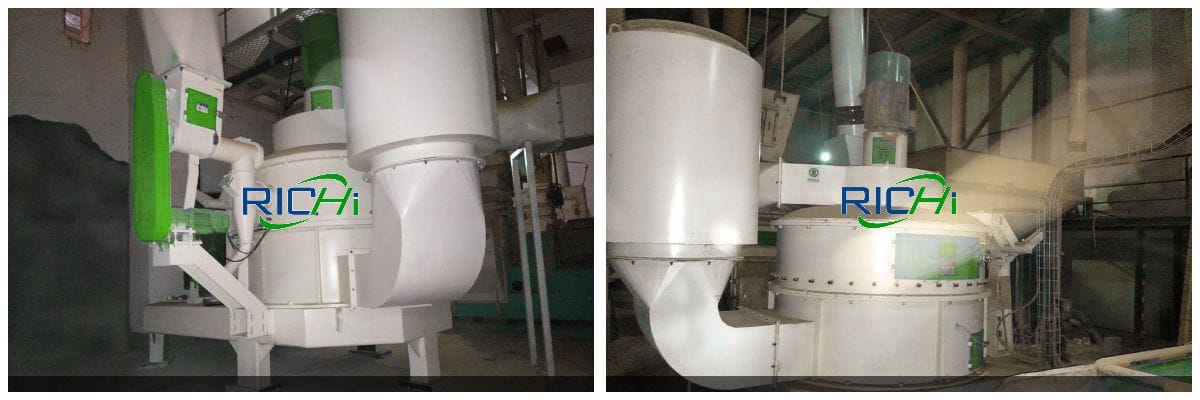
④ Superfine pulverization: The once-mixed material is transported to the hopper by closed pneumatic force, and the mixed material is sent to the closed superfine pulverizer through the conveyor according to the production demand. Using the high-speed rotation of the pulverizing disc in the superfine pulverizer, Under the action of the hammer, the material is crushed by the impact of the hammer knife installed on the crushing plate, and then is rotated to the surrounding ring gear at a very high speed.
Because the gap between the hammer knife and the gear ring is small, the hammer knife and the tooth between the circles changes along the trend due to the change of the tooth shape. The material is subjected to alternating stress during the probation again, and is further crushed under repeated action.
The crushed material is brought between the inner wall and the shunt hood by the airflow entering under the crushing disc, and then enters the classification chamber, and is classified by the selected grading wheel through the action of wind and centrifugal force, and the separated coarse material is discharged from the shunt hood The inner cavity of the crusher returns to the crushing chamber for re-crushing, and the qualified fine materials enter the grading impeller and enter the collection system from the discharge port.
⑤ Secondary mixing: The superfine pulverized qualified material is weighed and proportioned by computer control, and then enters the mixer for secondary mixing. The mixing process is completely sealed, and this process will generate noise.
(2) Cooking and ripening stage:
After the raw and auxiliary materials go through the raw material processing stage to form a uniformly mixed semi-finished feed powder, they will enter the cooking stage. The cooking stage of 5t/h aqua feed plant is to heat and cook the feed to change the feed from raw to cooked. After the feed is matured, it is processed by a fish feed extruder at high temperature and dried to form a bulky and porous pellet feed.
① Mauration: The mixed material enters the maturation equipment, and the product is steamed by high-temperature steam (80~90°C), so that the feed changes from raw to cooked and forms a slurry. The aging process produces a foul odor. The heating method of the aging process is the steam direct contact type, the steam is in direct contact with the material, and the steam is used as the aging water to mix with the material.
② Expansion: The cured slurry material is passed into the closed aqua feed extruder. Feed expansion in the extrusion cavity is actually a high-temperature instantaneous process.
That is, the feed is subjected to high temperature (110-200°C), high pressure (25-100 kg/cm2), high shear force, high moisture (10%-20% Even 30%) environment, through continuous mixing, tempering, heating, pressurization, extrusion die hole and sudden pressure drop to form a bulky and porous pellet feed.
The heating method of the puffing process is the steam indirect heating method. The puffing process will produce a certain amount of malodorous gas. (Related product: floating fish feed machine)
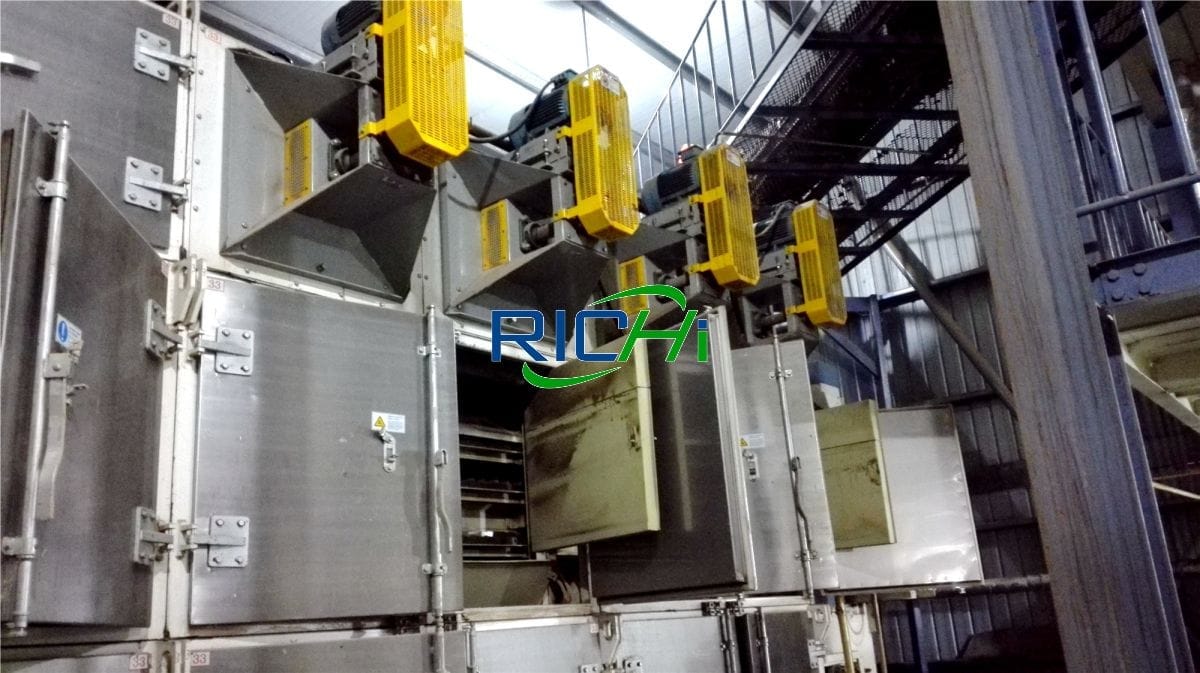
③Drying: The expanded material forms a bulky and porous pellet feed, but the moisture content in the pellets is still high, and will continue to be dried. The drying equipment of 5t/h aqua feed plant is adjacent to the extruding equipment and adopts the method of steam indirect heating. The drying process will produce a certain amount of malodorous gas.
(3) Cooling forming, screening and packing stage:
The raw and auxiliary materials are cooked and matured to form a bulky and porous pellet feed, which will be cooled and cooled. After packaging, the product is formed.
① Cooling: In the production process of feed pellets, the temperature of the pellets after pellet expansion and drying is as high as 90°C, and it must go through a cooling process to achieve the purpose of cooling. The countercurrent cooler used is composed of a material inlet, an air outlet, a silo, a collecting hopper, a frame and a discharge mechanism.
The discharge mechanism adopts a reciprocating discharge fence type discharge mechanism, and the fan passes through the air outlet. Negative pressure is generated in the silo, and cold air outside the silo enters the silo through the gap between the movable sieve and the fixed sieve, contacts with the hot pellets, takes away the heat of the pellets, and cools the pellets. The cooling process produces a small amount of malodorous gas.
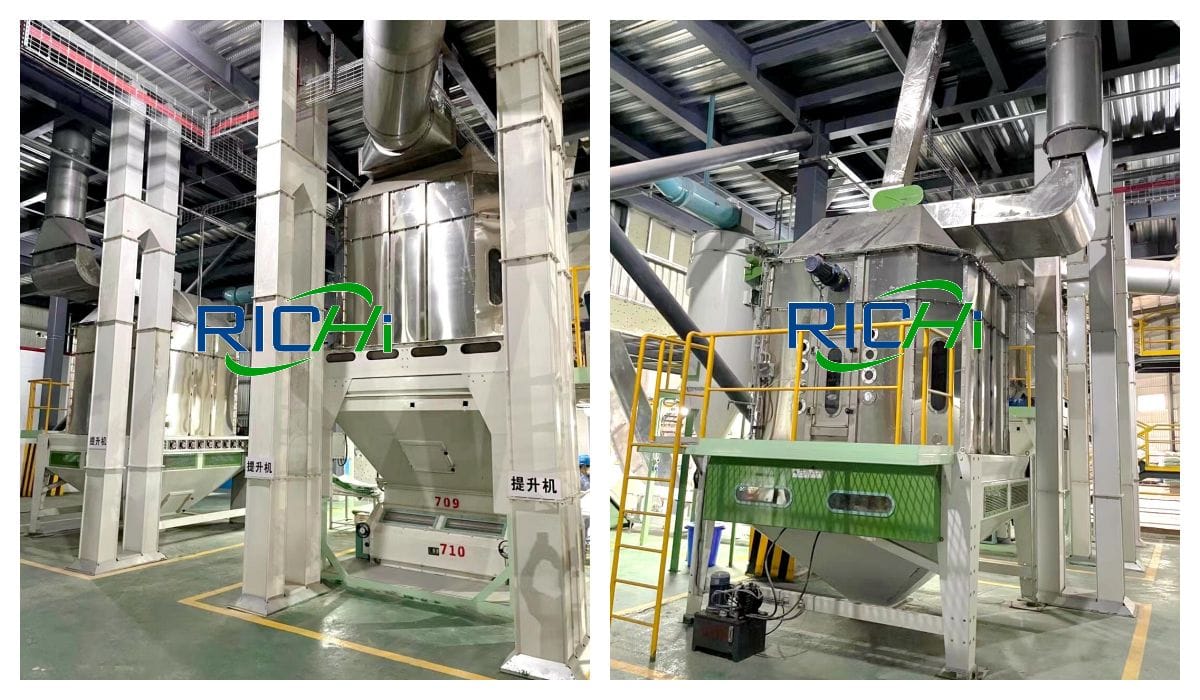
② Screening: A part of the cooled pellets are directly lifted by the elevator to the grading screen, and the qualified ones enter the packaging process; the rest enters the crushing process, and the products of different specifications are obtained after being screened by the grading sieve.
③ Packing and warehousing: The finished products are automatically stacked by robots and palletizers, and shipped to the warehouse for storage. Dust will be generated during the packaging process, and it is equipped with a pulse dust collector to collect the dust.
5T/H aqua feed plant layout
The existing project site covers an area of 56,850 m². The main buildings include office buildings, building A dormitory, building B, canteen, production workshop, raw material warehouse, finished product warehouse, packaging warehouse, boiler room, machine repair room , Power distribution room. The total construction area of the existing buildings is about 28609 m². (Related product: sinking fish feed machine)
In this expansion project, a 6-story production workshop will be built within the scope of the existing land use. The main production functions include ultrafine grinding, cooling, drying, curing, raw materials, storage of semi-finished products, spraying, screening, sieving, pulse dust removal, etc.
The newly added 10t/h biomass briquette fuel boiler will continue to use the existing boiler room, and through the upgrade of the existing exhaust pipe, it will share an exhaust pipe with the existing boiler for exhaust.
Building Name | Site area (m²) | Number of layers (F) |
---|---|---|
Office building | 382 | 3 |
A dormitory building | 404 | 5 |
Dormitory Building B | 375 | 5 |
Canteen | 362 | 2 |
Production Workshop | 1088 | 6 |
Material Warehouse | 6960 | 1 |
Finished goods warehouse | 7165 | 1 |
Package Warehouse | 1336 | 1 |
Boiler room | 443 | 1 |
Mechanical Repair Room | 332 | 1 |
Power distribution room | 81 | 1 |
New workshop (boiler relies on the existing boiler room) | 800 | 6 |
Water supply and drainage engineering
Water for the 5t/h aqua feed mill plant project is supplied by municipal tap water pipelines. The main water links of the project are as follows:
①Production water:
The total annual production time of the existing project is 4800h/a, and the main production water links include: boiler pure water manufacturing, boiler water replenishment, process waste gas spray tower replenishment, and boiler flue gas spray tower replenishment.
After the expansion of this 5t/h aqua feed plant project, the production plan, production process, and raw and auxiliary materials of the expansion project are exactly the same as the fish feed pellet production line of the existing project, so the production water consumption method and water quota per unit product of the expansion project are the same as those of the existing project.
② Boiler water
The water required for boiler heating is pure water, which is produced by a pure water machine using fresh tap water. The pure water efficiency of the pure water mechanism is 75%, that is, 1 ton of tap water can produce 0.75 ton of pure water and 0.25 ton of concentrated water.
The existing project has a total of 15t/h biomass briquette fuel boiler for steam production. Boiler steam is used for material slaking, fish feed puffing and feed drying processes. Boiler steam is mainly used in the aging process, granulation process, puffing process, and drying process of the steam conditioning stage.
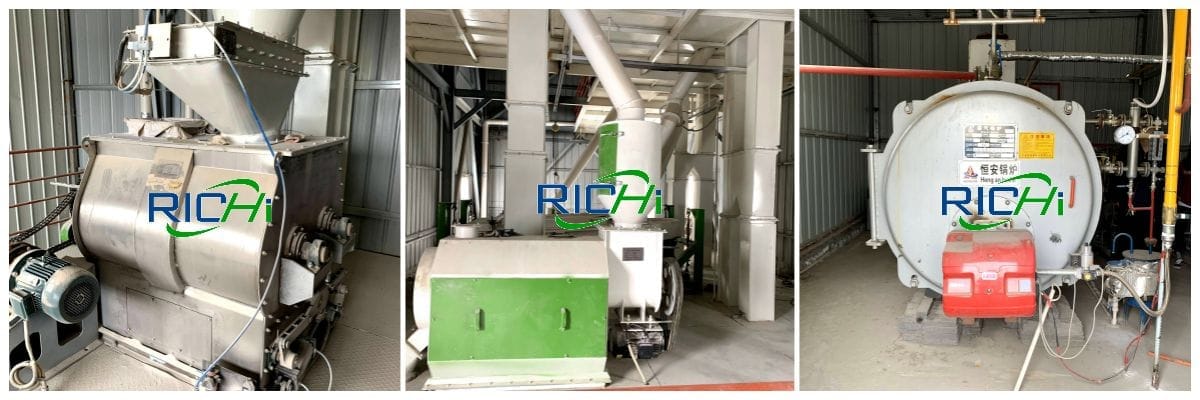
To sum up, the boiler steam loss in the existing project is 2.2t/h, that is, 2.2t/h of pure water needs to be added per hour (equivalent to 10560t/a), and the pure water efficiency of the pure water mechanism is 75%, that is, every 2.2t produced pure water requires 2.93t of fresh tap water (14080t/a).
This expansion 5t/h aqua feed production project with an annual output of 25,000 t/a fish feed will add a 10t/h biomass briquette fuel boiler. The purpose and service life of the boiler are the same as those of the existing project. Expansion and drying process, excluding granulation process.
Considering that the fish feed products produced in this expansion project are exactly the same as the existing fish feed production process and the types of raw and auxiliary materials for production, the steam supply of this expansion project is compared with the boiler steam of the existing project, and the expansion project is calculated in proportion.
The amount of steam used in the project’s ripening process, puffing process, and drying process is 1.3t/h (6170t/a), 3.4t/h (16457t/a), 4.3t/h (20560t/a), totaling 9.0t/h ( 43177 t/a). The amount of pure water supplemented by the boiler is 1.3t/h (6170t/a), and the pure water production efficiency is calculated as 70%, so the fresh water required for the newly added boiler for 5t/h aqua feed plant to produce pure water is 1.7t/h (8213t/a).