Origin of the 6T/H Aquatic Feed Mill project
The client of this 6t/h aquatic feed mill project is mainly engaged in the production and sales of livestock and poultry, pellet fish feed and extruded fish feed.
In order to better integrate production, sales, and raw material resources, reduce comprehensive technology costs, and expand and stabilize the company’s market share, the customer invested 4 million US dollars (including all upfront costs) to add an extruded fish feed pellet production line to the existing feed workshop. After the project is completed and put into operation, it can form an annual production capacity of 25,000 tons of extruded feed.
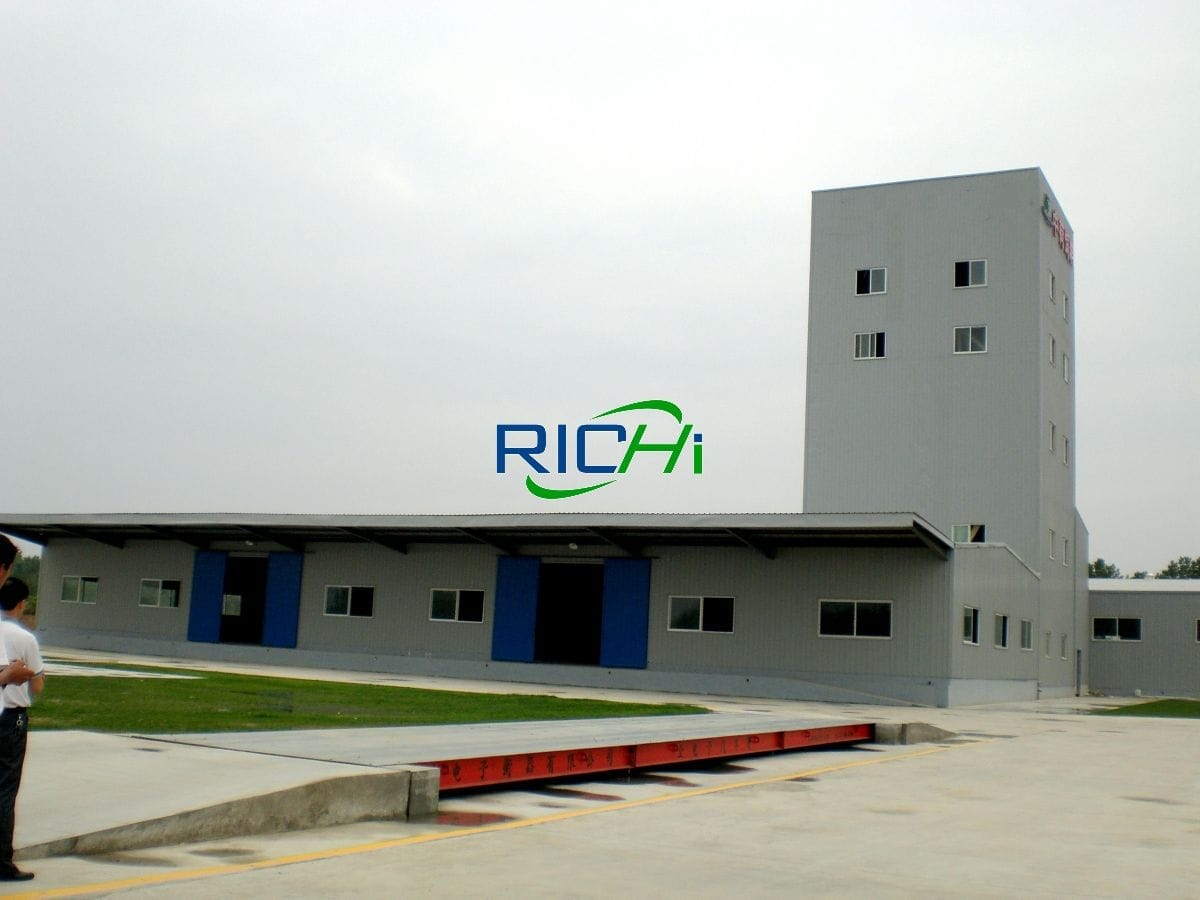
The client is a subsidiary of a very well-known company, so it has strong reliance on economic strength. The environmental protection of the fishery is becoming stricter, the fishing volume is shrinking, the removal of cages and the return of fish to the lake are favorable factors, the development prospects of the aquatic product breeding industry are broad, the aquatic feed industry is expected to share the policy dividend, and the demand is growing steadily.
Especially for mid-to-high-end varieties, downstream farmers may increase the amount of feed fed to increase and accelerate product weight gain, thereby driving demand for feed.
Seeing the development prospects of extruded fish feed, as an enterprise that processes livestock and poultry feed and high-grade shrimp feed, the customer decided to build a new extruded aquatic feed mill relying on its own advantages in raw materials, formula, capital and technology.
With an output of 6 tons per hour, it is not a small scale for a new production line, and customers have higher requirements for the configuration of this fish food processing line and a high degree of automation. Robots, palletizers and other equipment have also been added to improve the overall and configuration level of the aquatic feed production line.
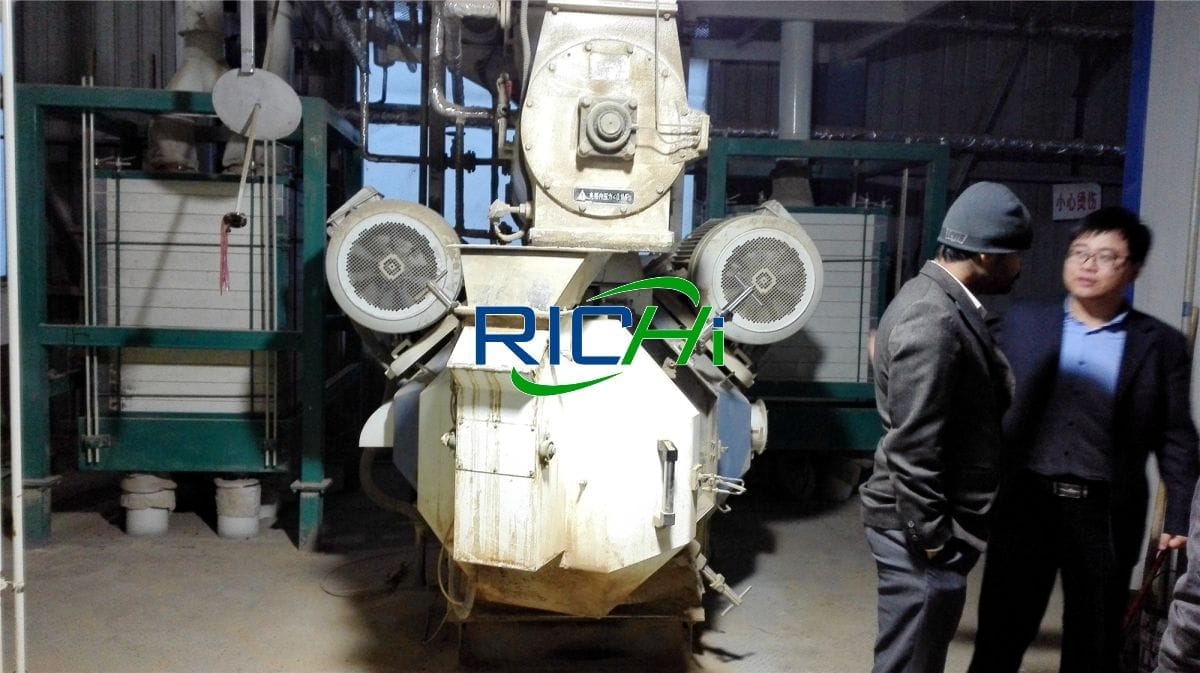
Because the customer’s request is to process high-end extruded feed products. In addition, customers also expect to increase the possibility of processing extruded shrimp feed products with the help of this extruded aquatic feed mill.
Main engineering and product plan
Engineering name | Capacity before expansion (t/a) | Capacity after expansion (t/a) |
---|---|---|
Livestock and poultry feed production line | 120000 | 120000 |
High-grade shrimp feed production line | 15000 | 15000 |
Extruded feed production line | 0 | 25000 |
Annual operation time
Engineering name | Yearly run hours |
---|---|
Livestock and poultry feed production line (cattle, chicken) | 6000 |
High-grade shrimp feed production line | 4000 |
Extruded feed production line | 4000 |
Public and auxiliary works of 6 t/h aquatic feed mill
- Raw material warehouse: 2000 m², relying on the existing, add 2*50m³ oil tanks for storing soybean lecithin oil;
- Finished product warehouse: 1000m², relying on the existing.
Consumption of main raw and auxiliary materials
Name | Annual Usage (t/a) |
---|---|
Barley | 726.01 |
Corn | 0.55 |
Cheap flour | 705.10 |
High gluten flour | 2390.08 |
Wheat middlings | 17.89 |
Rice Bran | 1599.22 |
43% soybean meal/46% soybean meal/45% soybean meal | 25.83/5730.00/69.12 |
Cottonseed Protein/50% Cotton Meal | 1560.23 |
Rape meal | 1857.60 |
Peanut Meal | 951.54 |
Corn Gluten | 467.41 |
30% cornstarch residue | 441.75 |
Imported fishmeal (Denmark) | 53.37 |
Imported fish meal (Taiwan grade) | 234.28 |
Imported fish meal (Japanese grade | 1422.69 |
Imported fish meal (Thailand grade) | 89.45 |
Vietnamese Seawater Fish Meal | 32.63 |
American red fish meal | 102.17 |
In addition to the above raw materials needed in the 6t/h aquatic feed mill, also need shrimp powder, dried shrimp, 46% shrimp shell powder, 30% shrimp shell powder, imported chicken powder, pork powder, soybean oil, phospholipid oil, fish oil, rice bran meal, stone powder, calcium dihydrogen phosphate, bentonite , squid paste, blood globulin powder, premix and other raw materials.
Main aqua feed production equipment
(1) Feeding section:
2 pulse dust collectors*LNGM18A, 2 scraper machines*TGSSP16, 2 bucket elevators*TDTG40/28, 2 cleaning screens*SCQZ90*80*110, 2 permanent magnet cylinders*TCXT25, 2 distributors *TFPX12A;
(2) Primary batching section:
23 batching bins, 23 batching augers*TLSUW20, 3 batching scales*PLDY1000-C/PLDY250-C, 2 mixers*SLHSJ2A, 1 scraper conveyor*TGSSP16, 1 bucket elevator* TDTG40/28, 1 permanent magnet cylinder * TCXT25;
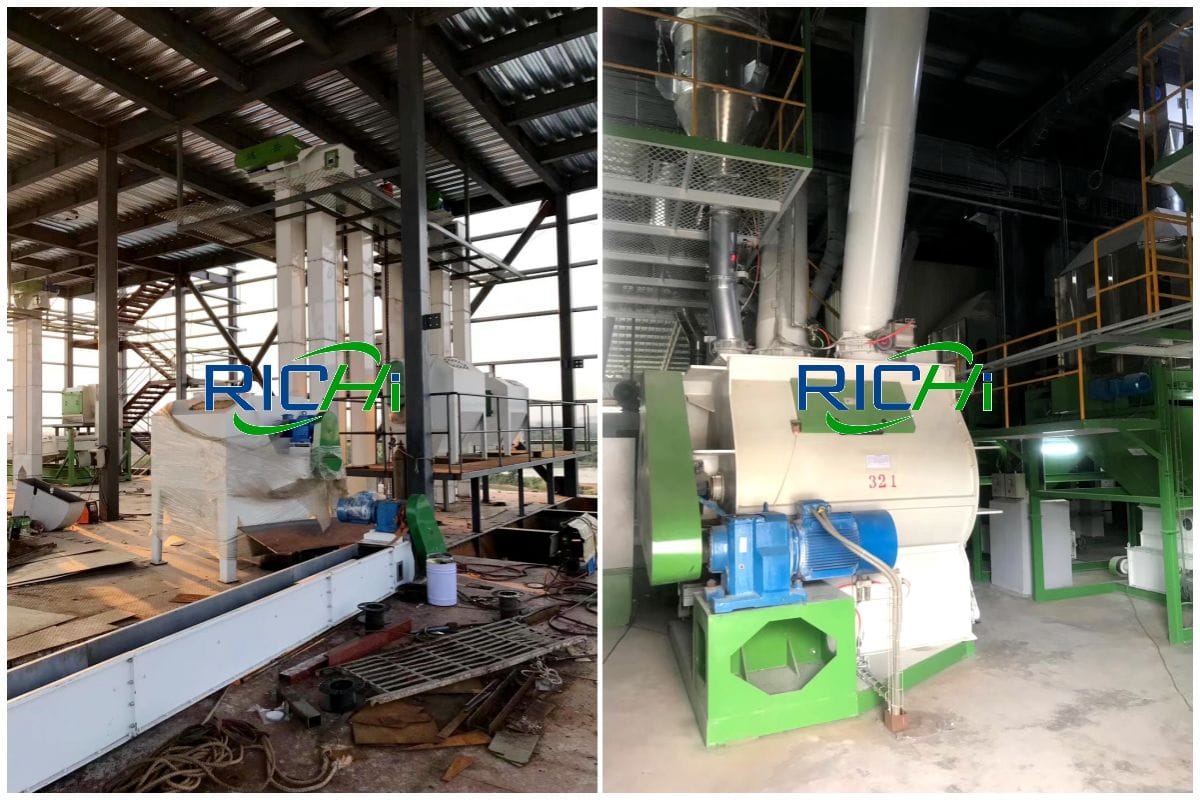
(3) Primary crushing section:
2 bins to be crushed, feeding auger *TWLY20*125, pulverizer *SWFP66*125D, closed air auger *TLSUF25, bucket elevator *TDTG40/28, permanent magnet cylinder *TCXT25;
(4) Secondary crushing section
2 bins to be crushed, 2 feeding augers *TDWLSS.200, 2 superfine pulverizers *SWFL017C, 2 cyclone dust collectors *SKLX55, 2 air shutoff devices *TCFZY-9, 2 pulse dust collectors* TBLMYZ108, 2 high-pressure blowers *TY55-1C, 2 high square screens *SFJM125*4;
(5) Secondary batching section
3 batching bins, 3 batching augers*TWLL32, 1 batching scale*PLDY1000-C, 1 mixer*SLHSJ0.5A, 2 scraper machines*TGSSP16, 1 bucket elevator*TDTG40/28 , 1 permanent magnet cylinder * TCXT25;
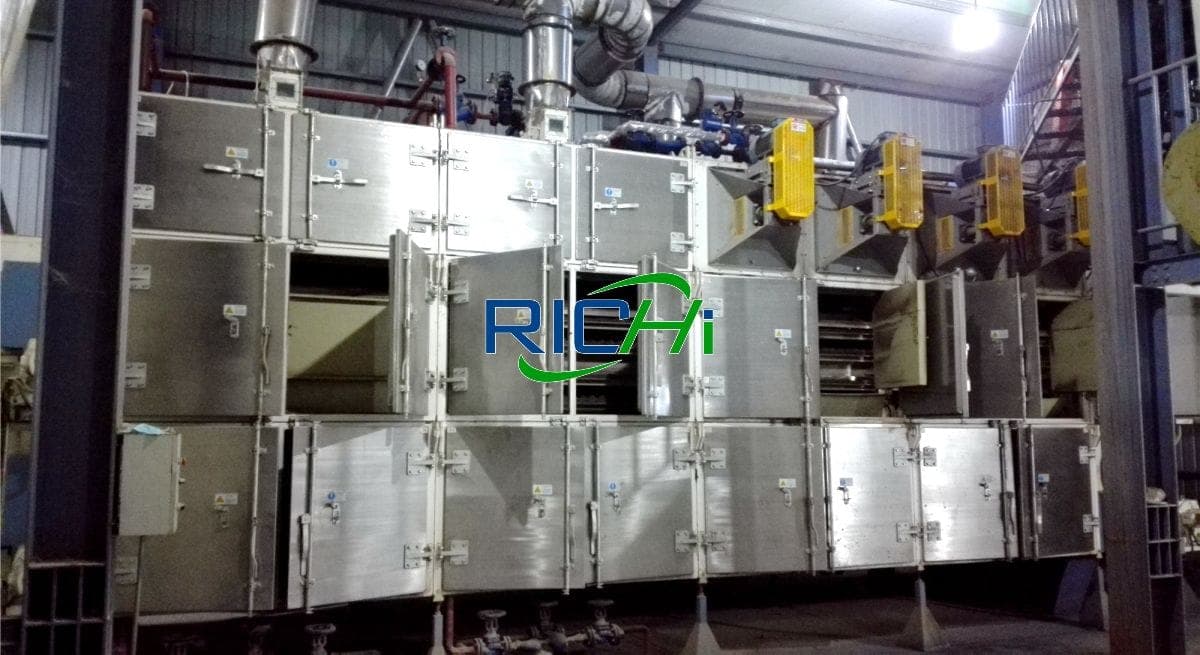
(6) Expansion drying section
2 bins to be extruded, 1 distribution tray*TXLP160A, feeder*TWLL24A, 1 single-shaft conditioner*TDTZ450*3000, 1 dual-shaft differential speed conditioner*SCTZ39, 1 extruder*SJPS166 *2, 1 suction fan*2378A/505A, 1 cyclone dust collector*XKLX55, 1 air shutoff device*CFDWZB-45-E, 1 dryer*TDHG.25/8F.4, 1 fan *4-72-5.5C, 1 Sacron*SKLX55, 2 conveyor belts, 1 bucket elevator*TDTG40/28, 1 grading screen*SFJH180;
(7) Cooling and packaging section
5 finished product warehouses, 1 grease spraying machine*VPLV135, 1 cooler*SLNF32*32, 1 cooling fan*TY55-1C, 1 cyclone dust collector*SKLX55, 1 air shutoff device*GF-12, 1 Bucket elevator * TDTG50/32, 1 distributor * TFPX4A, 1 grading screen * FJH130 * 2C, 1 buffer bucket, 2 packaging scales * PSC50, 3 conveyor belts, 1 robot, 1 yard Stacker.
Note: In this 6t/h aquatic feed mill project, except that the robot is shared with the high-grade shrimp feed production line, the rest are new equipment.
Working system and labor quota
- Working system: The production of this aqua feed mill project implements a two-shift system (about 10 hours per shift), and the annual effective working days are 200 days.
- Number of employees: There are currently 50 employees, and 20 people will be added for this project.
6T/H aqua feed mill process design
(1) Raw material receiving and initial cleaning: Raw materials such as soybean meal are sent to the bucket elevator through the scraper conveyor, lifted to the cleaning sieve to remove debris, and then the ferromagnetic debris is removed by the permanent magnet cylinder, and transported to the batching bin.
A certain amount of waste residue will be produced during the initial cleaning of raw materials, mainly waste grass ropes, sand and stones, and ferromagnetic sundries. The amount of waste generated is about 2‰ of the amount of raw materials used, about 50t/a.
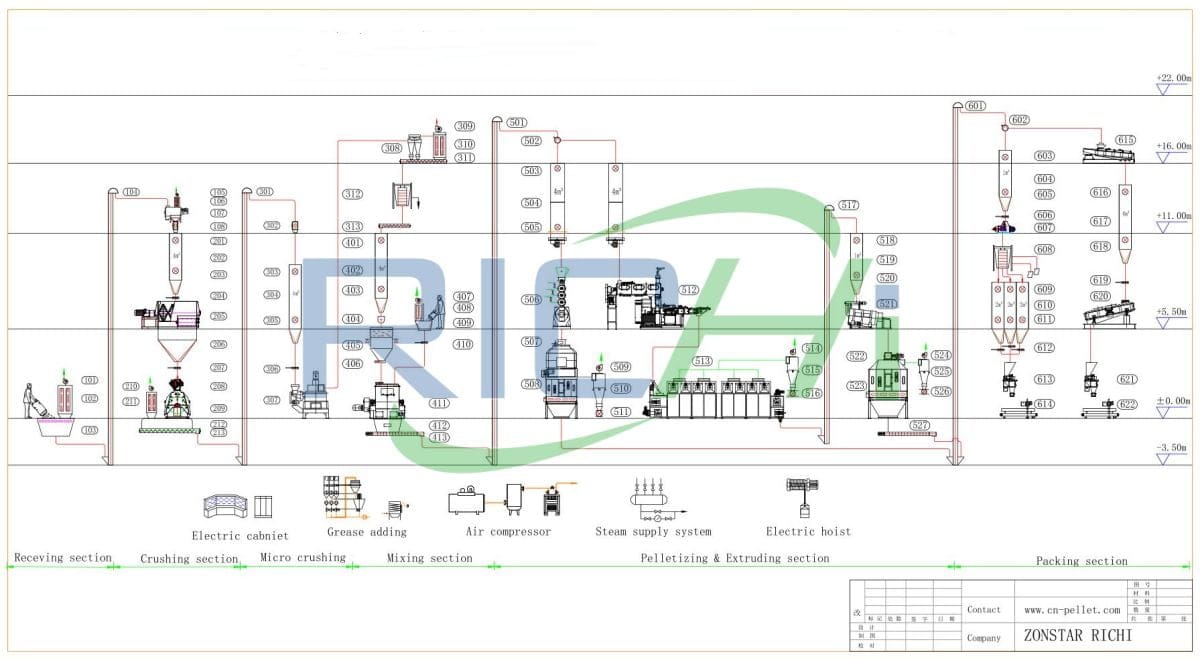
(2) Primary batching, mixing, primary crushing, and secondary crushing: various raw materials are weighed and batched through computer control, and then enter the twin-shaft high-efficiency mixer for primary mixing, and the mixed materials are transported into the pulverizer for secondary crushing. The whole 6t/h aquatic feed mill process is closed and automated.
(3) Secondary batching and mixing: various auxiliary materials are weighed and batched by computer control, and then enter the mixer together with the primary premix for secondary mixing. The mixing process is completely sealed.
(4) Extrusion: The mixed material enters the bin to be expanded, and is subjected to high-temperature treatment through a fish feed extruder, and the feed is matured by steam conditioning and reaches a certain uniformity. (Related post: floating fish feed machine)
(5) Drying: After the puffing is completed, it must be dried to remove moisture.
(6) Grease spraying: After the dried material is screened, it is mixed with grease evenly through a spraying machine.
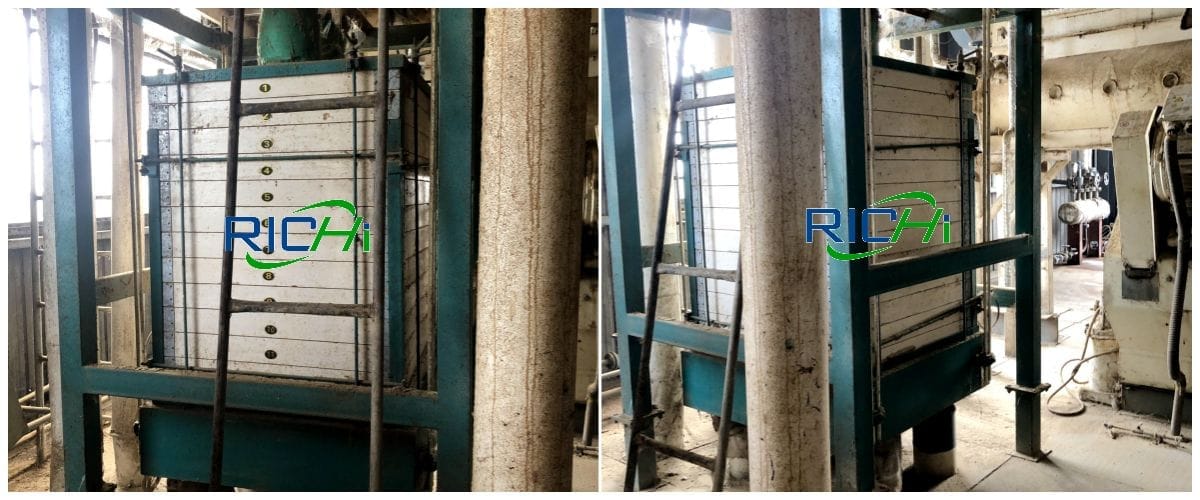
(7) Air transport: After spraying, enter the feed pellet cooler to cool and air dry.
(8) Screening: Elevated by the elevator to the grading screen, and the qualified products enter the packaging process, which will produce unqualified products.
(9) Packing and warehousing: the finished products are automatically stacked by robots and palletizers, and transported to the warehouse for storage. The packaging process generates dust.
6T/H aquatic feed mill layout
Layout of the factory area: This project does not require new land acquisition. On the southeast side of the factory area is a 2F office building and a 3F building (the first floor is a canteen, and the second and third floors are dormitories); the east side is a 5F building with an original 120,000 tons/year feed project workshop, 1F raw material warehouse, 1F finished product warehouse.
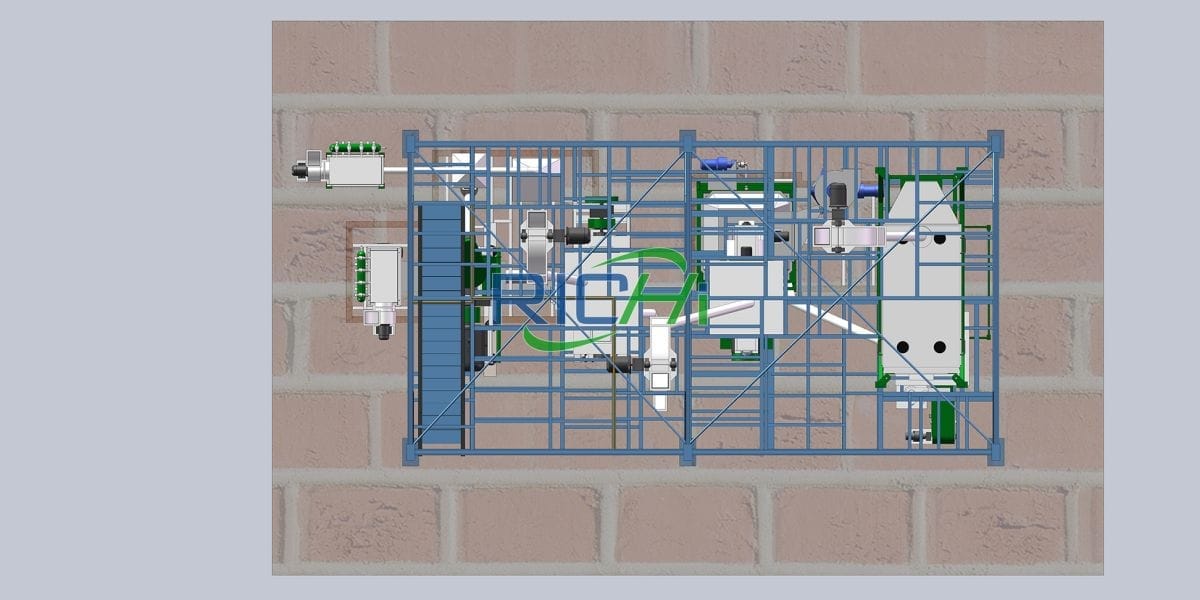
The central and northern part of the factory area is the boiler room (the heating demand of the whole aqua feed plant can be met during the transition period, once the electric pipe network is in place, it will be dismantled immediately); the west side of the factory area is 5F shrimp feed factory building, 1F raw material warehouse, 1F finished product warehouse. This aqua feed plant project adds an extruded feed production line to the reserved position of the original shrimp feed factory building.
Customer characteristics
- The fish feed mill plant has rich reserves of differentiated feed products, some of which have completed preliminary technical research and pilot test verification, and can launch corresponding new products at any time to meet market needs. At the same time, the client company also reserves animal-derived and plant-derived high-efficiency fish and shrimp feed differentiated products based on digestible nutrient balance.
- The essence of feed enterprise marketing is service. For a long time, the 6t/h aquatic feed mill has insisted on “vertical intensive cultivation of the market, in-depth development of marketing network, and the formation of a three-dimensional marketing network system. At present, the feed company has established a marketing team with a professional background in nutrition. The professional quality of marketing personnel can provide Downstream customers provide professional market services.
- Based on the perfect marketing team building, the feed company divides the feed company by area and deploys technical support specialists to realize multi-level technical support for customers.
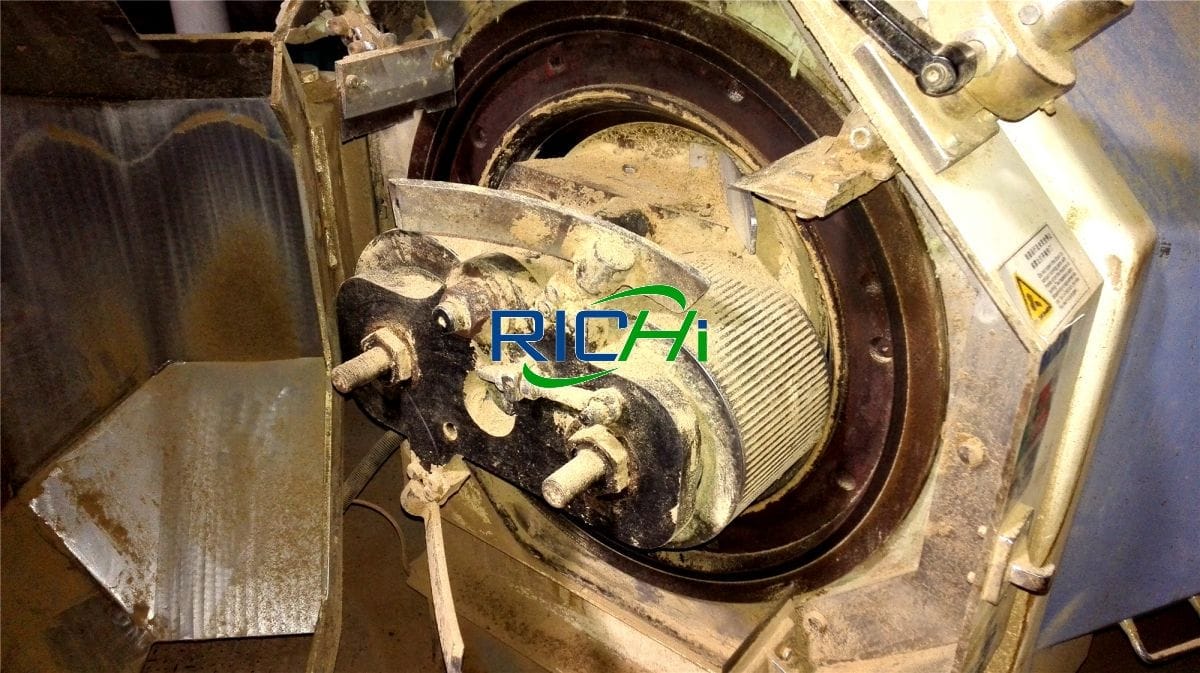
- At the same time, the feed company implements a consultative marketing model. Through professional interaction with breeding customers and technical guidance as the entry point, it conducts high-frequency visits to its customers, promotes products in professional exchanges, and serves its customers provide breeding information exchange and services.
- In addition, the feed company held grass-roots farming technology training sessions to meet the needs of farmers, bring real farming technology to grass-roots first-line farmers, and summarize the farming model through farming technology, and provide customers with a series of technical and drug solutions. supporting services.
Benefiting from a marketing team with a professional background and a customer-oriented marketing model, the feed company can accurately perceive customer needs at the first time, solve customer demands, and provide sales channels for farmers’ product sales to ensure farmers’ benefits. It makes customers understand the superiority of the product and recognizes the brand and service of the aquatic feed mill, which greatly enhances his customer loyalty.