Project overview
The project is a newly built comprehensive compound feed factory, including three types: 500kg/h fish food production line, 1.5t/h pig feed production and 2t/h poultry feed production line. According to the actual needs of customers, under the design and guidance of RICHI engineers, the project adopts the newly designed crushing first and then batching (fish feed processing) and the dual process of batching and crushing (pig and poultry feed production).
In June 2017, at the same time as the new feed production line was built, the customer’s feed company was also established. Like many of our other customers, wanting to produce multiple feeds with one production line is a common requirement. Because the variety of products increases, the profit point of the feed mill will increase.
Even if the output is small, for many areas, the total output of 4 tons per hour is completely enough to supply the surrounding farmers. If you don’t have much capital, but you want to use one production line to process multiple feeds, please feel free to consult Richi Machinery, we will provide you with affordable feed production line solutions.
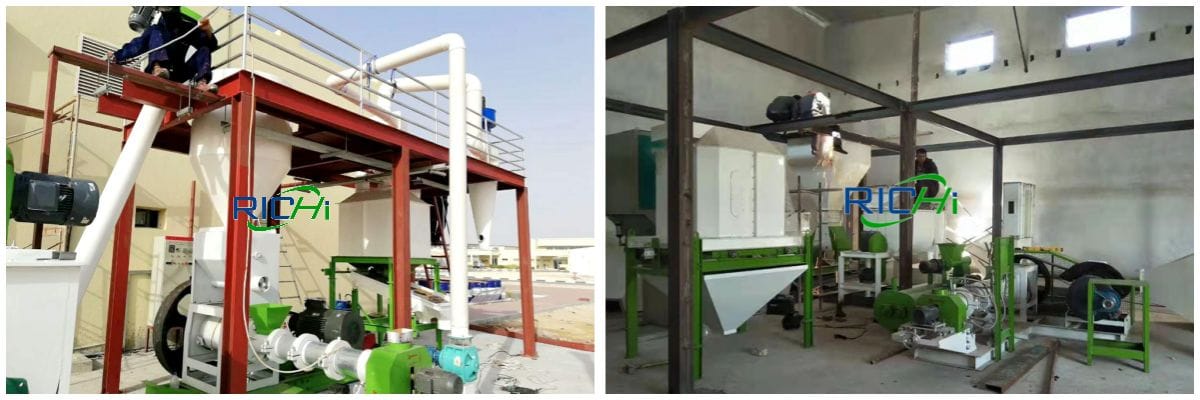
- The production capacity of the project is 10,000 tons/year (4t/h), including 500kg/h of fish feed;
- The total investment of the project is 120,000 US dollars (including all costs of equipment, civil engineering, etc.);
- Working system: 300 working days per year, 1 shift for production positions (production during the day, 3 hours a day for steam boilers, 8 hours for other work);
- Number of employees: 11, the employees are mainly local residents, and there is no dormitory in the factory.
- Project construction content and composition: The leased building area of the project is 2000m², including 160m² for office and living space, 400m² for production workshop, 1000m² for raw material warehouse, 400m² for finished product warehouse, 40m² for boiler room, and 40m² for building feed production line, new production and processing workshop with a construction area of 400m², including crushing process, mixing process, dust collection system, etc., reaching an annual production capacity of 10,000 tons.
Tips:
The type of feed processing chosen by the client for this 500kg/h fish food production line project is the development trend of the feed industry in the future – diversification of categories, not just one kind of feed. Especially for livestock and poultry feed factories, many of them have started to build new aquatic feed factories in recent years to enrich their product types. (Hot products: sinking fish feed machine)
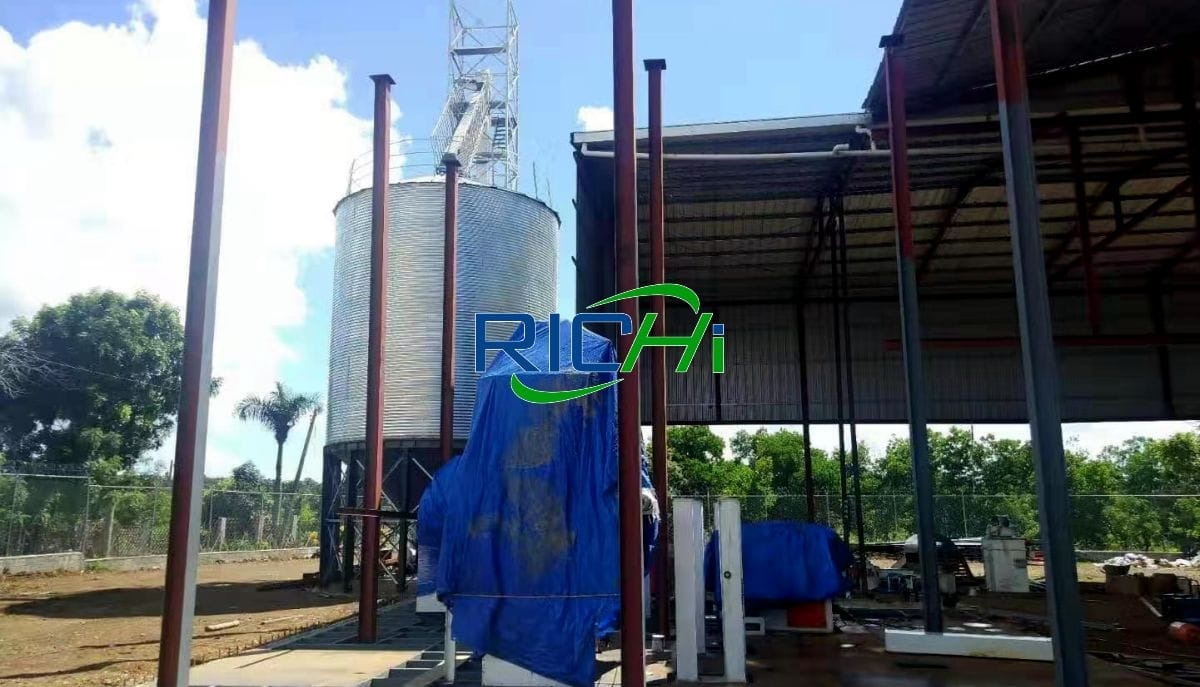
Regarding this point, no matter what kind of feed processing field you want to get involved in, “diversification” should be your long-term plan. (There are indeed some special circumstances, such as special feed processing. This type of feed is currently the type of feed with the best prospects and the best revenue. A small number of manufacturers can achieve high profitability by only operating one type of feed.)
If you also want to invest in a new fish feeds production line with the same output, you can consider the budget, local market conditions, raw materials and formula, etc. For the initial investment, you can invest in a very simple fish feed pellet production line.
If the budget is sufficient, you want to have a long-term vision in the field of feed processing development, or investment in production lines and equipment with greater output, we can customize according to the actual needs of customers. Regardless of the size of your output, regardless of the budget, as long as it is within our technical scope, Richi Machinery will definitely provide you with satisfactory project design, equipment quality and after-sales service.
Process design of 500 kg/h fish food production line
Outsourced raw materials that meet the production requirements, some are stored in the raw material warehouse for standby, and the rest are directly unloaded into the raw material feeding port, sent to the bucket elevator through the conveyor to the upper part of the main workshop for initial cleaning to remove impurities.
And the raw materials sent to the the silo is used for standby, corn and other granular raw materials are crushed by a fish feed pulverizer in the crushing section. After crushing, the corn is subjected to high temperature and high pressure and then decompressed.
Using the expansion characteristics of the corn itself and the instantaneous evaporation of its internal water, the organizational structure and physical and chemical properties of the corn are improved.
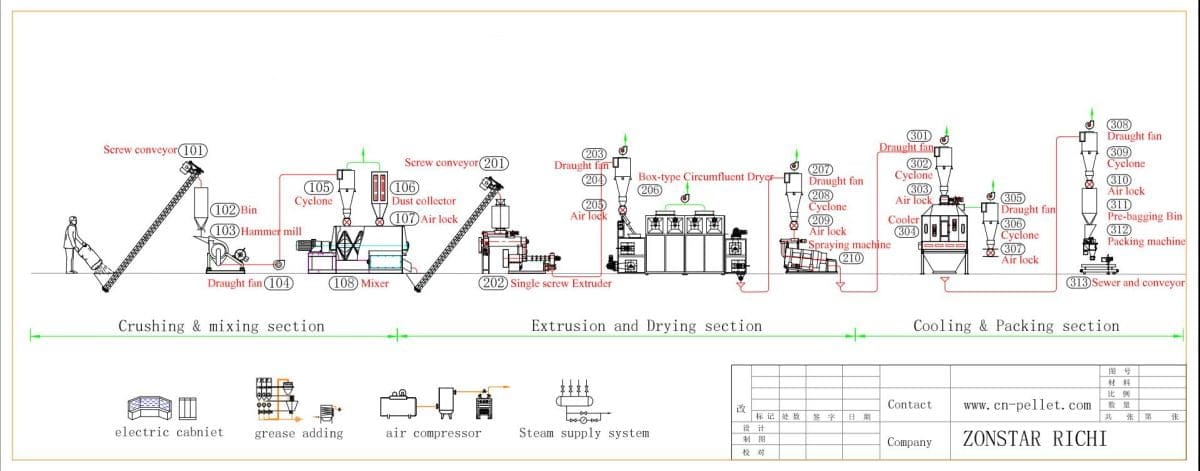
According to the ratio of the feed formula, all powdery raw materials (including feed additives) are electronically metered from their respective intermediate silos and sent to the mixer for full mixing, and the mixed powdery feed enters the silo to be granulated for use.
The powdery material is fed into the fish feed pellet machine and steamed for granulation. After granulation, it is cooled to room temperature by a counter-current cooler, and then crushed into finished products by a fish feed crusher. (May be you are interested in: floating fish feed mill)
Product plan of 500 kg/h fish food production line
Product | Annual production (tons) | Production ratio (%) |
---|---|---|
Pig feed | 3600 | 36 |
Poultry feed | 5200 | 50 |
Fish feed | 1200 | 14 |
Main raw material consumption
① Fish feed raw material consumption (t/a)
- Soybean meal: 720
- Rapeseed Meal: 120
- Fish meal: 240
- Additives: 60
- Other raw materials: 60
② Consumption of pig feed raw materials
- Corn: 2520
- Soybean meal: 900
- Fish meal: 72
- Additives: 108
③Consumption of poultry feed raw materials
- Corn:: 3900
- Soybean meal: 1200
- Rapeseed meal: 60
- Fish meal: 120
- Additives: 120
- Other raw materials: 600
Energy consumption of 500 kg/h fish food production line
Name | Annual consumption |
---|---|
Water | 318m³ |
Gas | 90,000 m³ |
Liquefied petroleum gas | 1500Nm³ |
Electricity | 28000KWh |
Equipment needed in 500 kg/h fish food production line
Device name | Specification model | QTY |
---|---|---|
Cylinder primary cleaning screen | TCQY125 | 2 |
Permanent magnet cylinder | TCXT | 2 |
Bucket elevator | DTG | 3 |
Feed crusher | TSDFS | 2 |
Sinking fish feed pellet mill | SZLH | 1 |
Pellet cooler | TNL | 1 |
Paddle mixer | TYHD | 1 |
Centrifugal fan | 4-72-12N06C | 1 |
Classifying sieve | THFS | 1 |
Screw conveyor | TLSS32 | 3 |
U-shaped scraper conveyor | TGSU32a | 1 |
Boiler | LHC0.95-0.8—AIII, 1t/h | 1 |
Public works
(1) Water supply
The water source of the 500kg/h fish food production line project mainly comes from the municipal tap water pipe network, and the water quality meets the drinking water standard for domestic water. (Aqua Feed Production Projects)
The water used after the project operation period is mainly domestic water; in addition, there are road flushing water and greening water. The total water consumption of this project is 378m³/a.
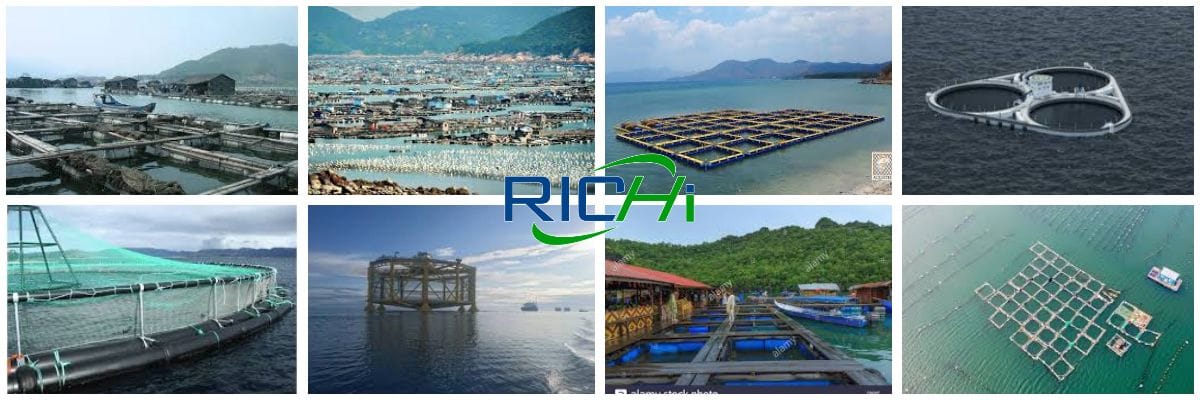
(2) Drainage
- Rainwater system: Rainwater and road flushing water can be discharged from the factory area through drainage ditches and pipes by using natural terrain.
- Sewage system: The sewage discharged from this project is mainly the office and domestic sewage of employees, and the sewage discharge of the project is based on 90% of the water consumption, the sewage production is about 0.77m3 /d.
The domestic sewage of this project will be used to fertilize the surrounding farmland after being treated in the septic tank to reach the “Integrated Wastewater Discharge Standard”, and will not be discharged outside.
(3) Power supply
The power supply of this 500kg/h fish food production plant project is connected to the municipal power grid, and the annual power consumption is about 28,000 kW·h.
500KG/H fish food production line layout
①Layout principle:
- On the premise of satisfying the process layout, strive to achieve compact layout and minimize land occupation;
- Pay attention to wind direction and orientation to reduce environmental pollution;
- Conscientiously do a good job in the fire protection of buildings to prevent fires, reasonably arrange fire protection facilities, and determine the distance between buildings according to the “Code for Fire Protection Design of Buildings”;
- Seriously deal with waste gas and noise pollution, create a good working environment, and ensure the physical and mental health of employees;
- Functional divisions are clearly defined, avoiding the intersection of people and logistics as much as possible.
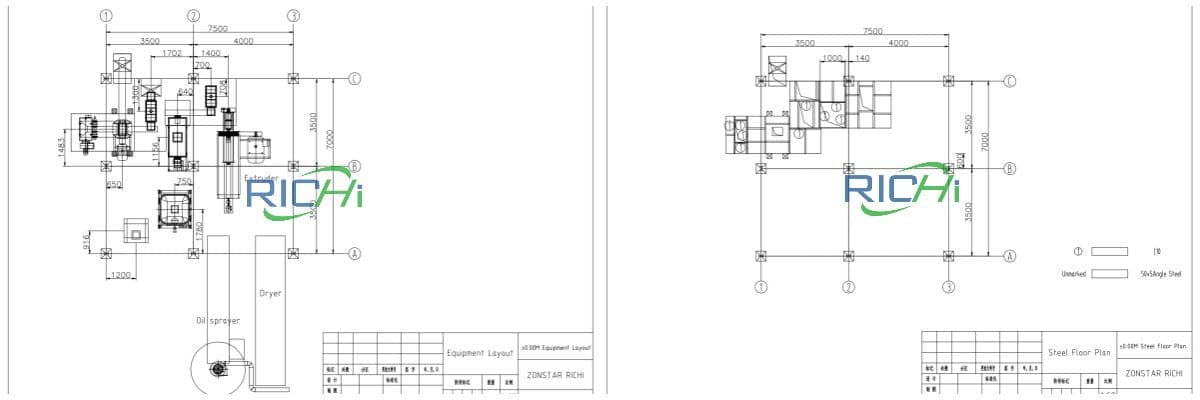
② General layout:
- According to the characteristics of the 500kg/h fish food production line project’s production process and the topography and geology of the site, the whole plant is mainly divided into two parts: production area and living area. Among them, the production area is arranged on the west side of the factory area, close to the side of the road, and the office area is arranged on the northwest side of the factory area.
- In order to avoid the impact of the noise generated by the boiler fan of the project on the farmers in sensitive points, the project arranges the boiler room on the side of the land on the south hillside, and at the same time minimizes the noise by installing noise reduction, sound absorption devices, and building sound insulation. The impact of noise on the external environment. Pipeline layout: The plane layout of pipeline lines strives to be straight, short, and properly concentrated, and is arranged in parallel along the living area and production area to minimize the intersection of turning lines and the intersection of pipelines and traffic lines. And consider the relationship with trees and plants to facilitate construction and save land.
According to the above description, the plant area of this project has the following characteristics:
The layout of the production line of this 500kg/h fish food production line project ensures the reasonable flow of process materials, the smooth connection of roads and pipe networks, and the smooth flow of fire-fighting passages for transportation.
Combined with the production process and the local conditions of the project, the layout and functional divisions are reasonably carried out to save land and ensure the greatest possible external protection. Environmental impact is minimized. (Related solution: 500kg/h fish food processing line)
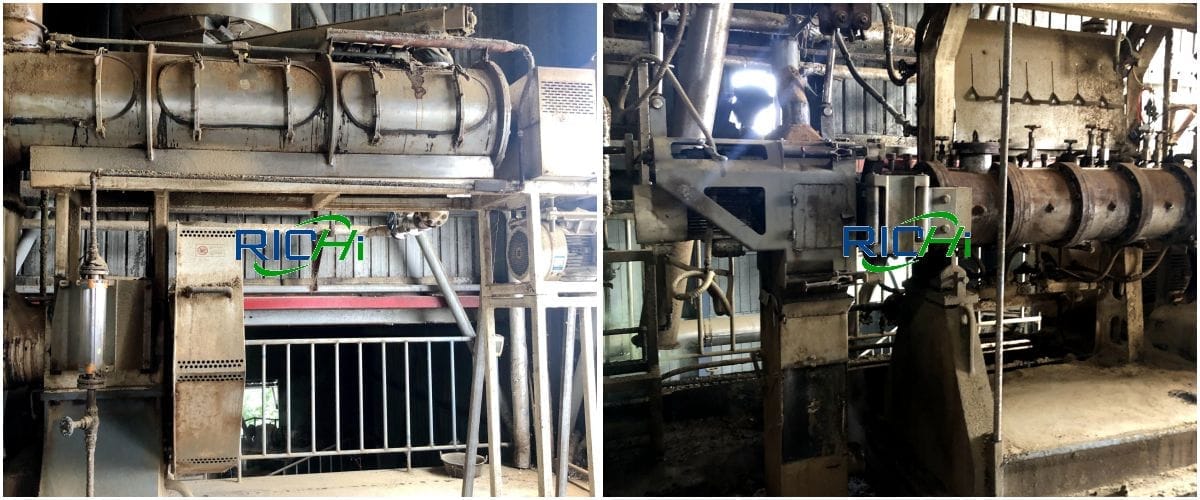
To sum up, the functional zoning of the factory area is reasonable and meets the external line access conditions of public works such as water and electricity. The layout of the general plan, the upper and lower processes are arranged compactly to avoid mutual interference, the economy is reasonable, the logistics is smooth, and it is basically reasonable from the perspective of environmental protection.
Clean production analysis
Cleaner production is to continuously apply the environmental strategy of comprehensive pollution prevention to the production process and products in order to reduce the environmental risks to human beings. It expresses the pollution prevention and control approach in the whole process from raw materials→production→products→consumption and use.
This 500kg/h fish food production line project belongs to a feed production and processing enterprise, which conforms to the local industrial policy. Its clean production is manifested in the following aspects:
(1) Raw materials and products
This project is feed processing, and the raw materials and products of the project are non-toxic and harmless clean substances, which meet the requirements for clean raw materials and the cleanliness of products. (Related solution: 4t/h aqua feed mill)
(2) Production technology
The RICHI process design and equipment used in the project are mature technologies, and the equipment is stable, reliable, and highly automated, and has been widely used in the feed processing industry.
(3) Pollutant emissions
After the waste water of this project is collected and treated by the septic tank, the agricultural fertilizer will not be discharged outside, and the waste gas can meet the standard discharge after treatment, so the pollutant discharge of this project is very small.
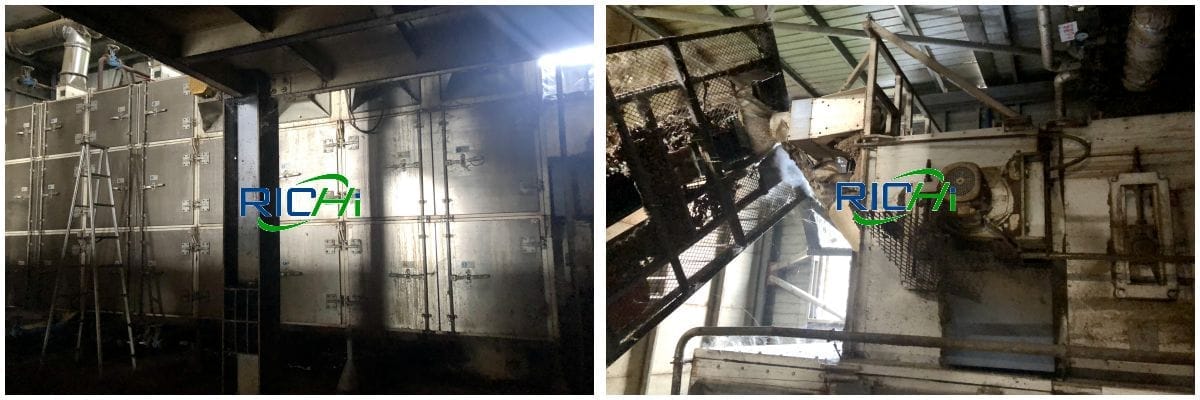
(4) Energy saving measures and environmental management
- The general plan layout of the 500kg/h fish food production line project strives to be compact, arranged according to the flow direction of materials, shortening the distance of material storage and transportation, avoiding the secondary handling of large items as much as possible, and reducing the consumption of manpower and material resources.
- Adopt new energy-saving transformers and power distribution and electronic control equipment, and install capacitance compensation screens in substations to improve power factor, reduce reactive power loss, and realize energy-saving operation.
The client company has established a sound corporate environmental management organization and organization, actively established and operated the ISO-14000 environmental management system, continuously reduced material consumption and energy consumption per unit of product, and continuously improved the company’s clean production level. Based on the above analysis, the clean production level of the 500kg/h fish food production line project is relatively advanced.