RICHI sinking fish feed processing line is a feed production system suitable for processing all kinds of sinking fish feed pellets with 1.5-12mm.
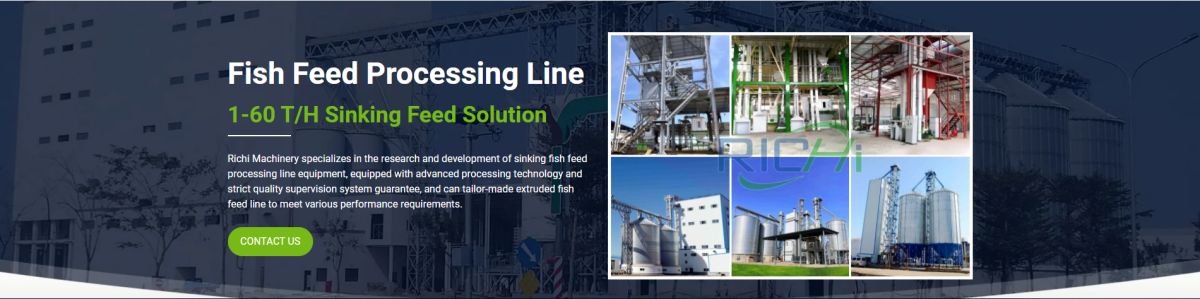
This series of 1-60 t/h fish feed lines has the characteristics of high degree of automation, convenient operation, integrated modularization, compact equipment, reasonable process flow, smooth production, complete product spectrum and wide coverage. It can produce feed pellets for fish sinking that requires the of national standards. It is the ideal choice for ordinary aquatic feed manufacturers.
RICHI MACHINERY has now formed a variety of complete, serialized, standardized, and generalized fish feed processing equipment of various stand-alone and complete sets of fish food processing line equipment.
Due to the level gap, a considerable part of the key equipment can be compared with the imported advanced equipment, and because of the low price and good pre-sales and after-sales service, it gradually occupies the international market, can replace imports and export products in batches.
sinking fish feed processing line Types
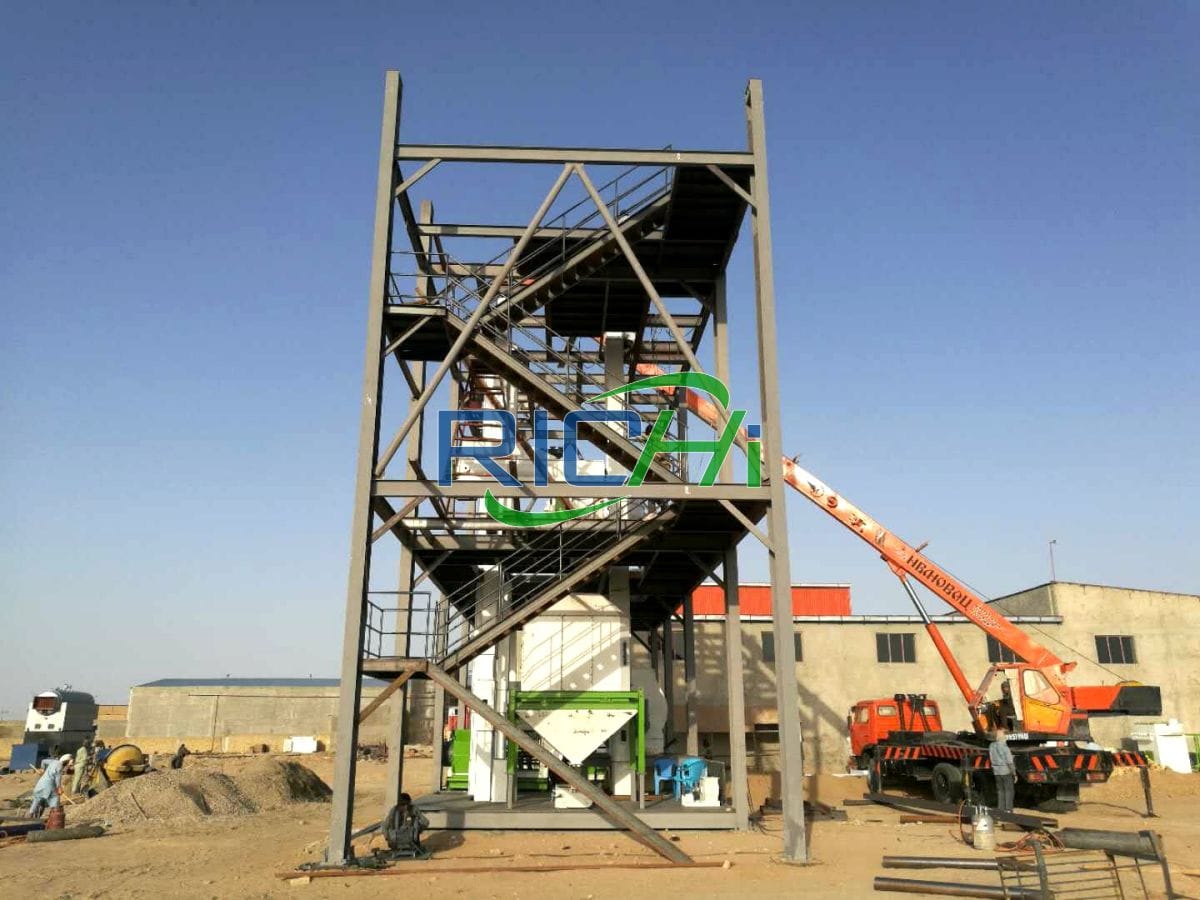
Sinking Fish Feed pellet making Line
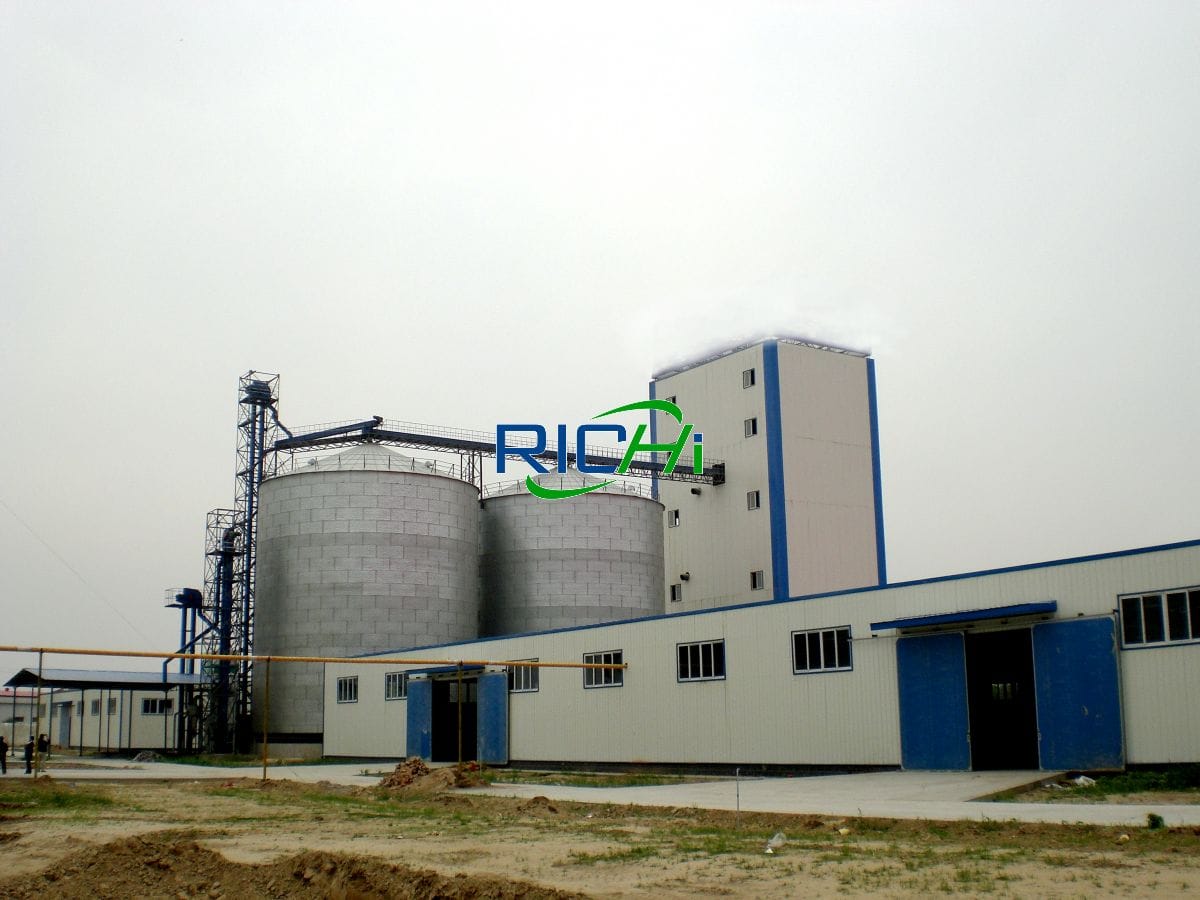
Sinking & Floating Fish Feed production Line
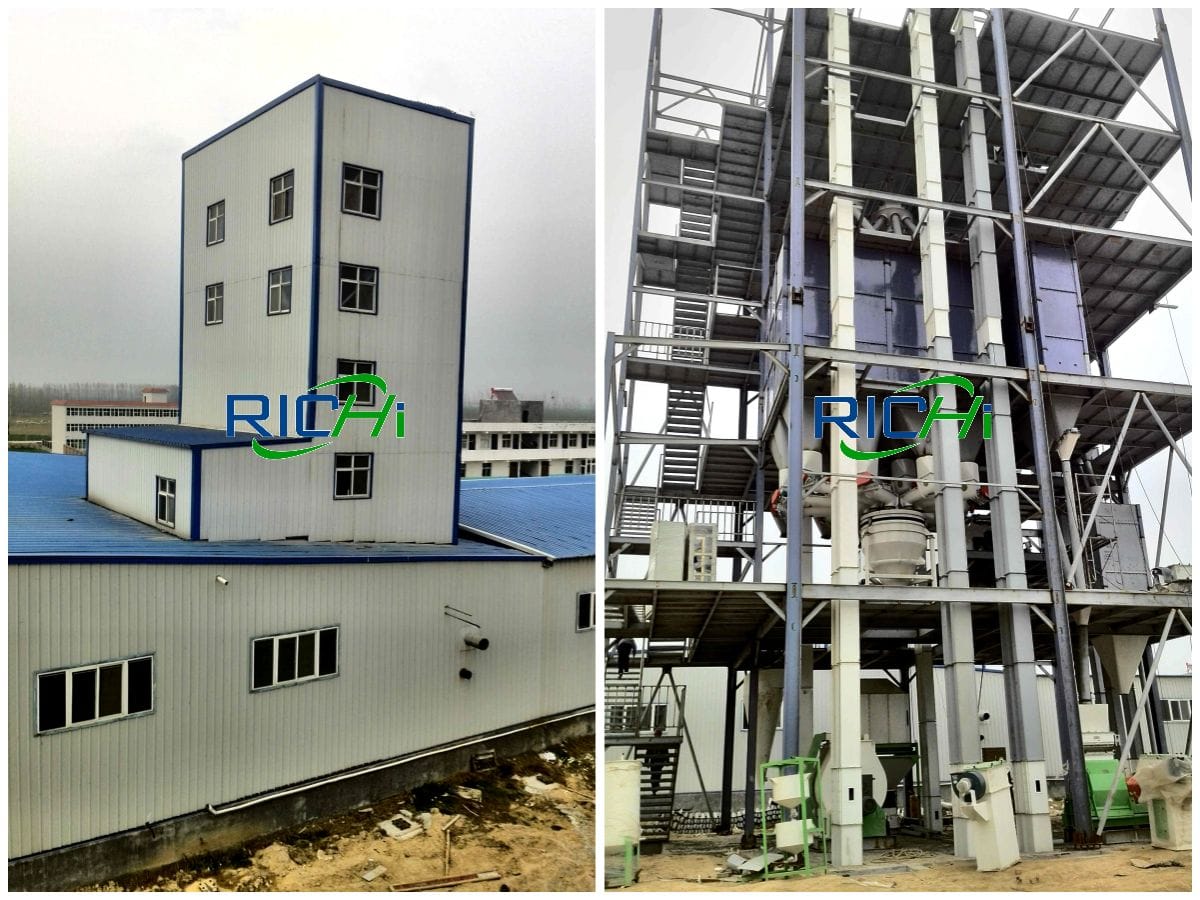
poultry & Sinking Fish Feed pellet Line
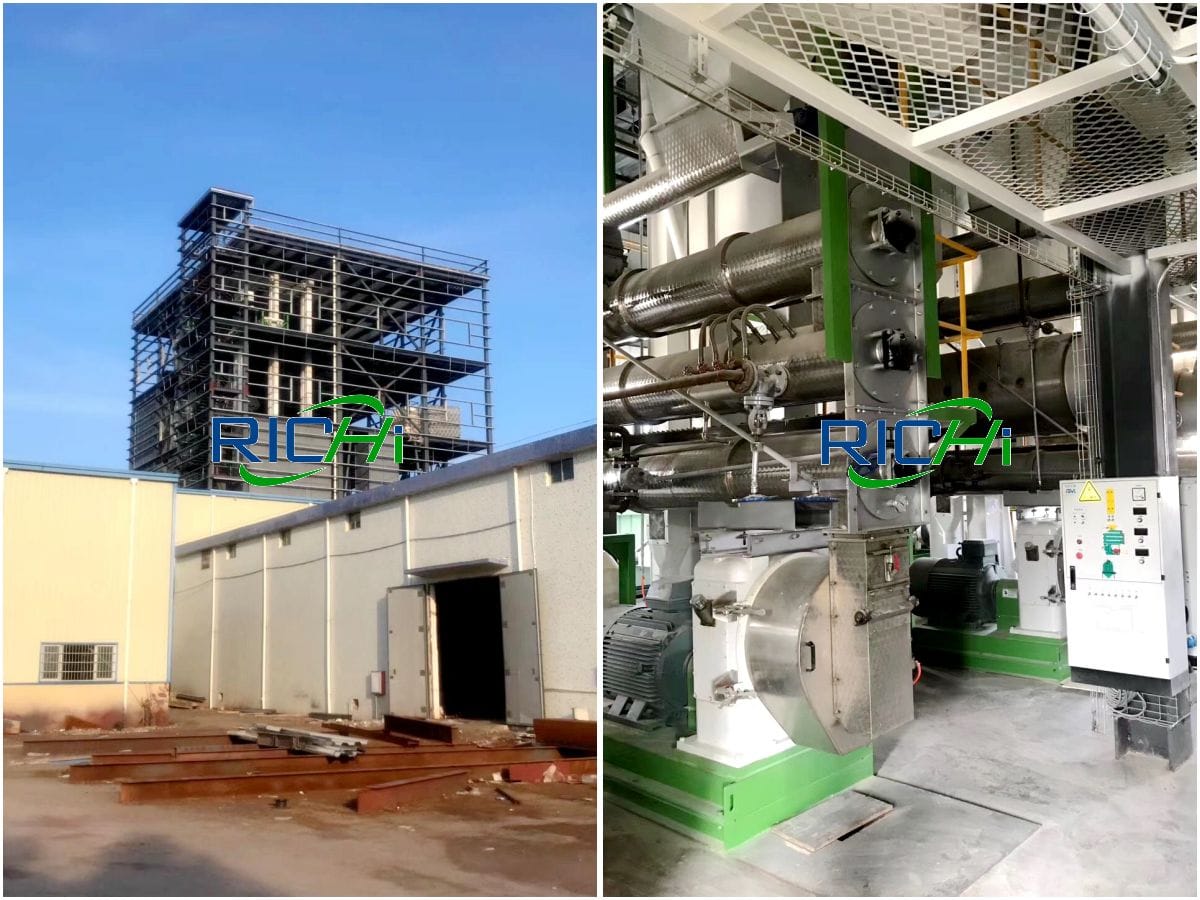
Shrimp feed & Sinking Fish feed pelleting Line
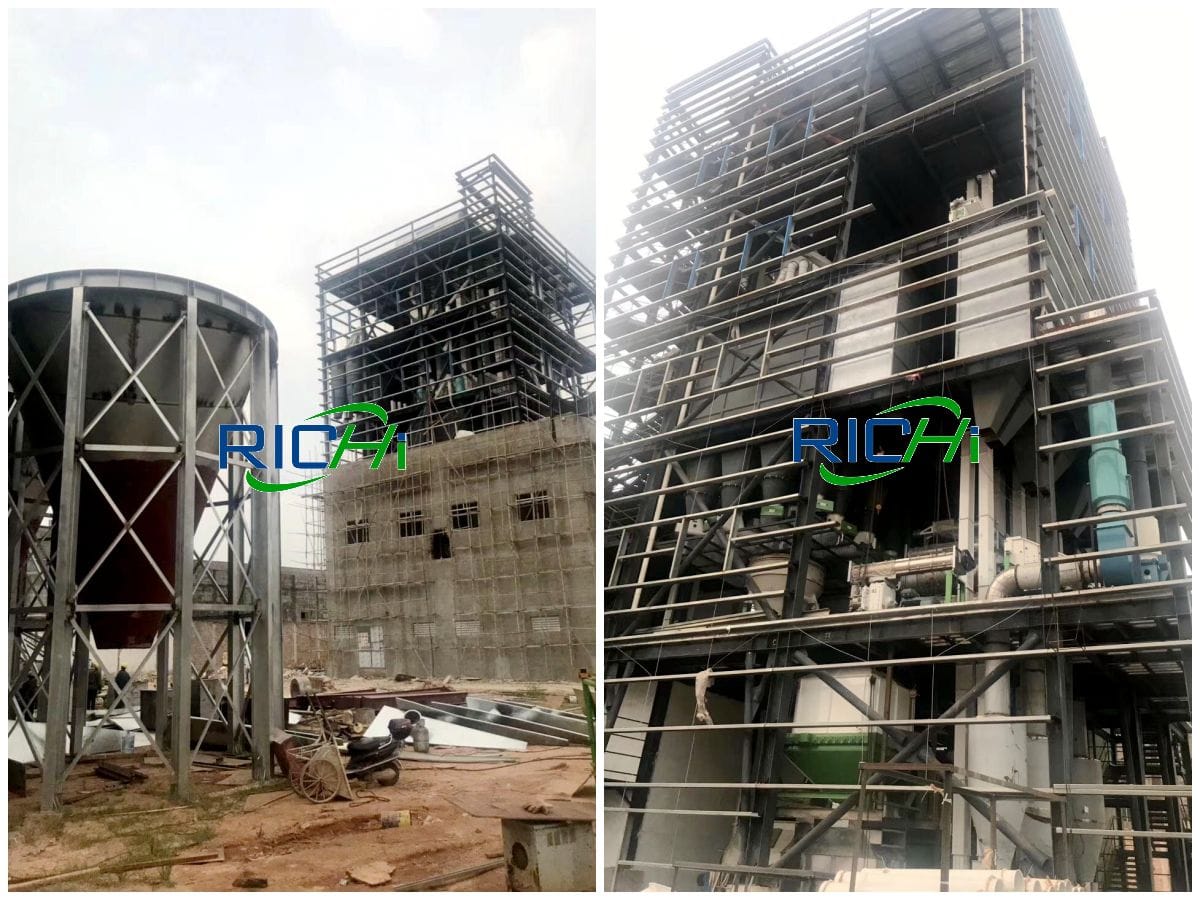
aquatic feed combined line for sinking fish & floating fish & shrimp & crab
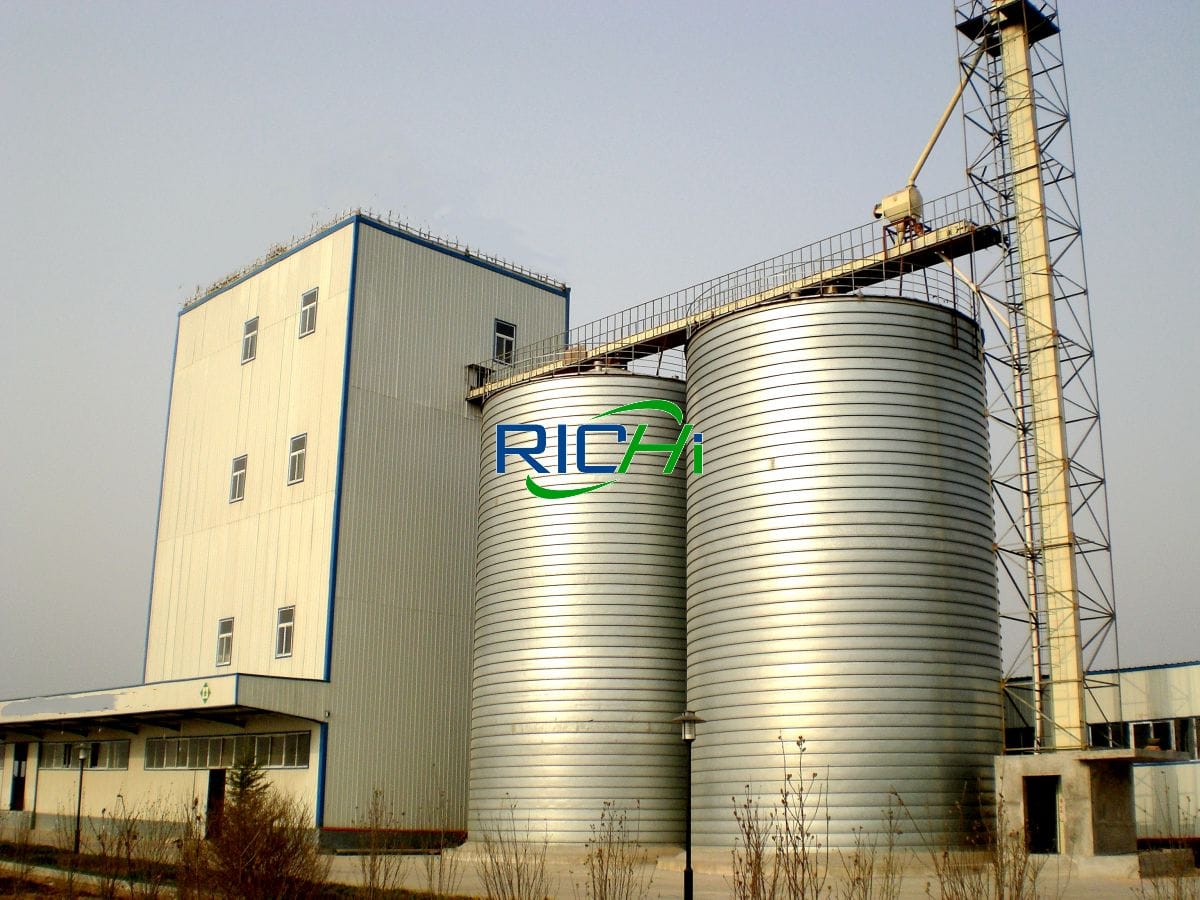
Sinking Fish & aquatic feed & livestock poultry feed combined line
If you want to process extruded sunken fish feed, please refer to the floating fish feed production line process, and welcome to contact us directly online to customize the extruded sunken fish feed production line process and configure reasonable fish feed equipment.
Featured sinking fish feed processing line solution
1.5-3T/H fish feed pellet processing line
Cost: 15000-200,000USD
Fish feed manufacturing process:
- Materials receiving& pre-cleaning system
- Crushing system
- Batching& mixing system
- Pelletizing& cooling& screening system
- Packing& dust collecting system
- Oil adding system
- MCC Control Center ;Mimic Control Panel
- Batching System (Computer controlled)
- Cables & Cable Bridge Tube
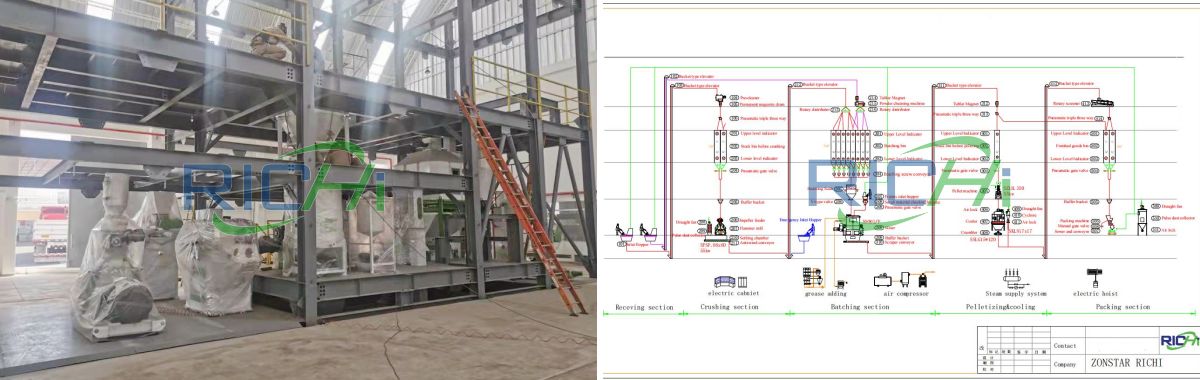
Main equipment:
Fish feed hammer mill | SFSP66*60 | 1 |
Batching scale | PLC0.5A | 1 |
Small material checking balance | PLC0.1B | 1 |
Single-shaft mixer | SLHJ1A | 1 |
2-Layer Conditioner | TZ35*244 | 1 |
Fish pellet machine | SZLH350 | 1 |
Cooling Machine | SKLN17x17 | 1 |
Crumbler | SSLG15*100 | 1 |
Rotary screener | SFJZ100*2C | 1 |
Automatic Packing machine | DCS-50 | 1 |
Heating oil storage tank | SYTZ100 | 1 |
Auxiliary equipment:
Feeding hopper with grids, Bucket elevator*TDTG36/28, Drum type precleaner*SCY63, Permanent magnetic sleeve*TCXT20, Pneumatic triple gate valve*YSTZ22A, Pulse dust collector*TBLMa.24A, Screw conveyor(air-locked), Rotary distributor*TFPX6, Powder precleaner*SCQZ60*50*100, Buffer bin*2.0m³, Scraper conveyor*TGSU20, Sewing machine+conveyor, etc.
1-2T/H sinking fish feed processing line
Cost: 10000-100,000 USD
Fish feed manufacturing process:
- Raw materials receiving and cleaning section
- Crushing section
- Mixing section
- Pelletizing& Cooling Section
- Packing section and centralized dedusting section
- MCC Control Center ;Mimic Control Panel
- Cables & Cable Bridge Tube
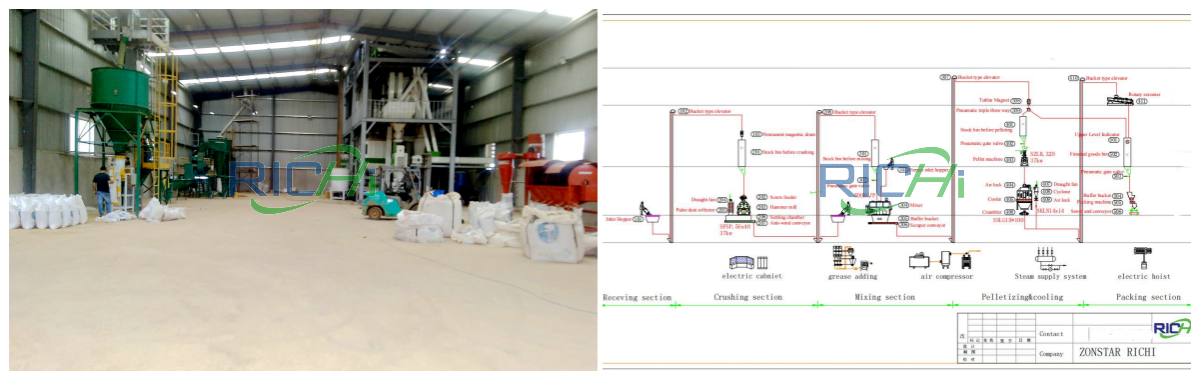
Main equipment
Hammer mill for fish feed | SFSP56*60 | 1 |
Mixing machine(Pneumatic door) | SLHY.1 | 1 |
Fish feed pellet machine | SZLH320 | 1 |
Cooling Machine | SKLN14×14 | 1 |
Crumbler | SSLG15X80 | 1 |
Rotary screener | SFJH800*2C | 1 |
Automatic Packing machine | DSC-50 | 1 |
Oil adding machine | YZTG100a | 1 |
Boiler system | 0.5T,0.7Mpa | 1 |
Air compressor and storage tank | 11KW | 1 |
Auxiliary equipment:
Bucket elevator*TDTG36/18, Permanent magnetic sleeve*TCXT20, Pre-Crushing bin*1m³, Rotary feeder*SWLY20*40, Pulse dust collector*TBLMa.12A, Bucket Elevator*TDTG36/18, Pre-Mixing Bin*1m³, Premix adding hopper, Scraper conveyor*TGSU20, Pneumatic three-way*YSTZ22A, Pre-Pelleting bin*1m³, Cyclone*SK800,
5-6T/H fish feed pellets processing line
Cost: 40000-300,000USD
Fish feed manufacturing process:
- Materials receiving& pre-cleaning system
- Crushing system
- Batching& mixing system
- Pelletizing& cooling& screening system
- Packing& dust collecting system
- Oil adding system
- MCC Control Center ;Mimic Control Panel
- Batching System (Computer controlled)
- Cables & Cable Bridge Tube
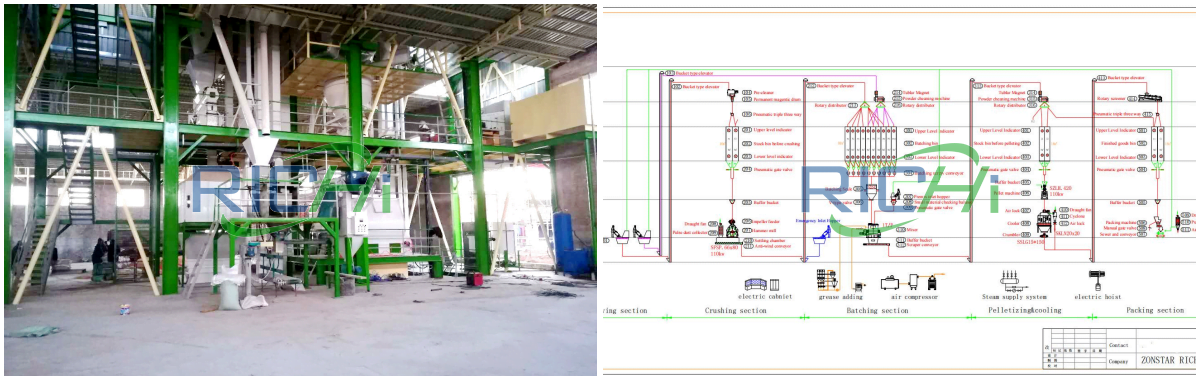
Main equipment:
Fish food hammer mill | SFSP66*80 | 1 |
Single-shaft fish feed mixer | SLHJ2A | 1 |
2-Layer Conditioner | TZ42*300 | 1 |
sinking Fish feed pellet mill | SZLH420 | 1 |
Cooling Machine | SKLN20x20 | 1 |
Crumbler | SSLG15*150 | 1 |
Rotary screener | SFJH125*2C | 1 |
Automatic Packing machine | DCS-50 | 1 |
Auxiliary equipment:
Bucket elevator*TDTG36/28, Feeding hopper with grids, Drum type precleaner*SCY63, Permanent magnetic sleeve*TCXT20, Variable frequency feeder*SWLY20X80, Pulse dust collector*TBLMa.36A, Rotary distributor*TFPX8, Powder precleaner*SCQZ60*50*100, Rotary distributor*TFPX6, Batching scale*PLC1.0A, Premix adding hopper, Small material checking balance*PLC0.1B, Buffer bin*2.5m³, Rotary distributor*TFPX4, Air lock*GF.40, Manual pick up mouth*TZMS25, Heating oil storage tank*SYTZ100, etc.
6-10T/H sinking fish feed processing line
Cost:60000-400,000 USD
Fish feed manufacturing process:
- Materials receiving& pre-cleaning system
- Crushing system
- Batching& mixing system
- Pelletizing& cooling& screening system
- Packing& dust collecting system
- Oil adding system
- MCC Control Center ;Mimic Control Panel
- Batching System (Computer controlled)
- Cables & Cable Bridge Tube
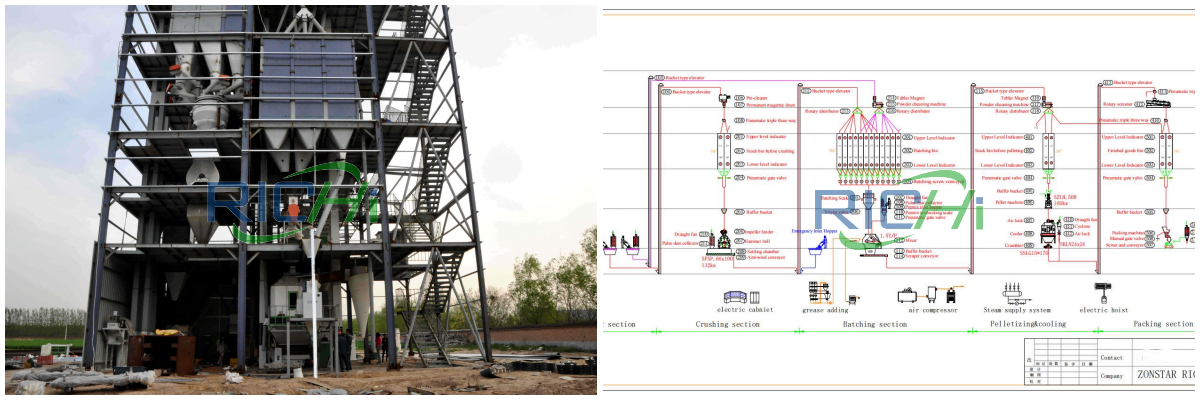
Main equipment:
Hammer mill | SFSP66*100 | 1 |
Single-shaft mixer | SJHS3A | 1 |
2-Layer Conditioner | TZ42*300 | 1 |
Pellet machine | SZLH508 | 1 |
Cooling Machine | Cooling Machine | 1 |
Crumbler | SSLG20*170 | 1 |
Rotary screener | SFJZ150*2C | 1 |
Automatic Packing machine | DCS-50 | 1 |
Auxiliary equipment:
Draft fan*4-72-3.2A, Pulse dust collector*TBLMa.12A, Feeding hopper with grids , Bucket elevator*TDTG36/28, Drum type precleaner*SCY63, Permanent magnetic sleeve*TCXT20, Pneumatic two-way*YSTZ22A, Settling chamber, Screw conveyor (air locked)*TLSS25, Rotary distributor*TFPX8, Powder precleaner*SCQZ60*50*100, Outlet Screw conveyor*PLSS25/20, Batching scale*PLC1.5A, Pneumatic gate valve*TZMQS60*2, etc.
8-16T/H sinking fish feed processing line
Cost:150,000-600,000 USD
Fish feed manufacturing process:
- Materials receiving& pre-cleaning system
- Crushing system
- Batching& mixing system
- Pelletizing& cooling& screening system
- Packing& dust collecting system
- Auxiliary system
- MCC Control Center ;Mimic Control Panel
- CPP Computer System
- Batching System (Computer controlled)
- Cables & Cable Bridge Tube
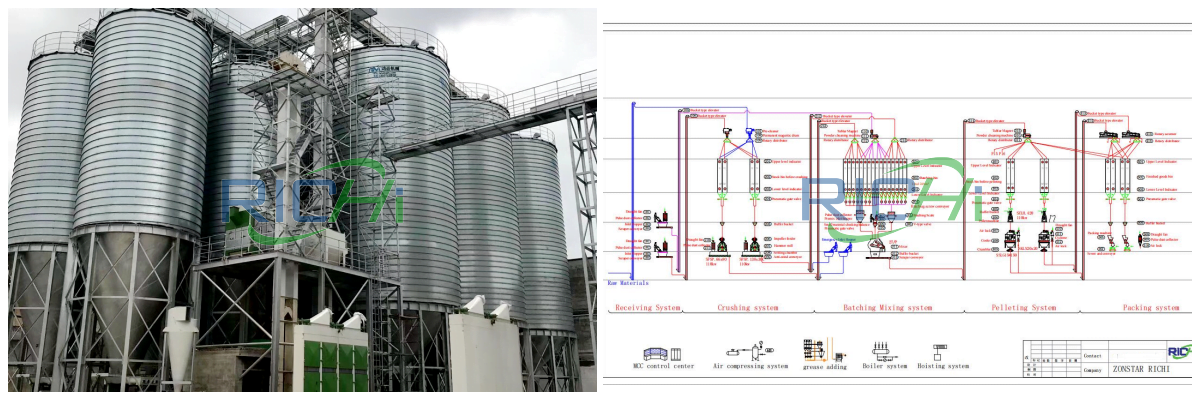
Main equipment:
Hammer mill for fish food | SFSP66*80 | 1 |
Fish feed grinder hammer mill | SFSP138*40E | 1 |
Mixing machine | SLHJ4.0A | 1 |
2-Layer Conditioner | TZ42*3000 | 2 |
Fish feed pellet making machine | SZLH420 | 2 |
Cooling Machine | SKLN20x20 | 2 |
Crumbler | SSLG15*150 | 2 |
Rotary screener | SFJZ125*2C | 2 |
Automatic Packing machine | DCS-50 | 2 |
Auxiliary equipment:
Scraper conveyor*TGSS25, Feeding hopper with grids, Bucket elevator*TDTG40/28, Drum type precleaner*SCY80, Rotary distributor*TFPX4, Powder precleaner*SCQZ60*50*100, Rotary distributor*TFPX8, Cone bucket, Lower level indicator*KF1500, Screw conveyor (air locked)*TLSS25, Outlet Screw conveyor*PLSS32, Outlet Screw conveyor*PLSS25, Outlet Screw conveyor*PLSS16, Batching scale*PLC1.0A, Pneumatic gate valve*TZMQS60*2, Small material checking balance*PLC0.15B, Bucket Elevator*TDTG50/28, Heating oil storage tank*SYTZ100, etc.
15-25T/H sinking fish feed processing line
Cost:200,000-800,000 USD
Fish feed manufacturing process:
- Materials receiving& pre-cleaning system
- Crushing system
- Batching& mixing system
- Pelletizing& cooling& screening system
- Packing& dust collecting system
- Auxiliary system
- MCC Control Center ;Mimic Control Panel
- CPP Computer System
- Batching System (Computer controlled)
- Cables & Cable Bridge Tube
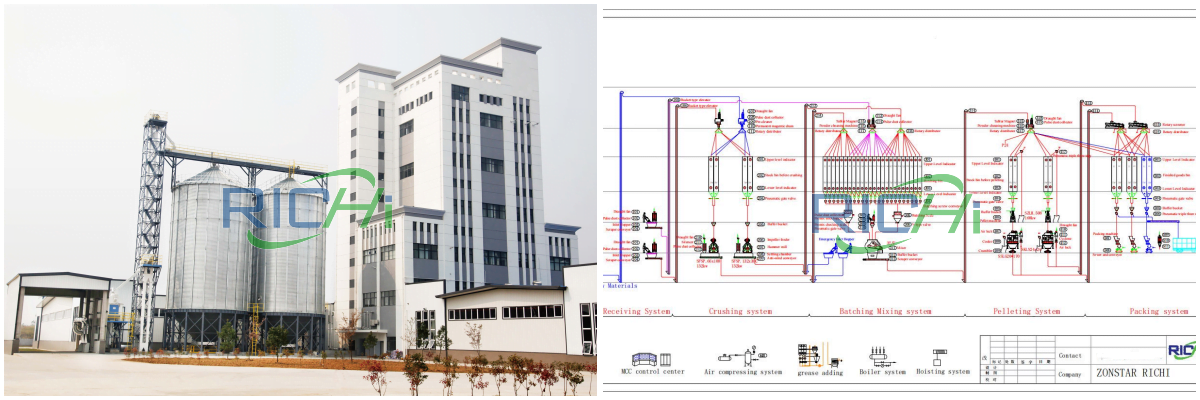
Main equipment:
Hammer mill feed grinder | SFSP66*100 | 1 |
Fish feed grinding machine | SFSP138*50E | 1 |
Single-shaft fish feed mixer machine | SLHJ6.0A | 1 |
SS Conditioner | TZ42*3000 | 2 |
Pellet machine | SZLH508 | 2 |
Variable-frequency Feeder | TWLL32 | 2 |
Cooling Machine | SKLN24x24 | 2 |
Crumbler | SSLG20*170 | 2 |
Rotary distributor | TFPX6 | 2 |
Packing machine | DCS-50 | 2 |
Auxiliary equipment:
Pulse dust collector*TBLMa.12A, Feeding hopper with grids, Bucket elevator*TDTG40/28, Pulse dust collector*TBLMa.4A, Drum type precleaner*SCY80, Permanent magnetic sleeve*TCXT30, Pulse dust collector*TBLMa.4A, Powder cleaning sieve*SCQZ90*80*110, Rotary distributor*TFPX12, Buffer hopper, Variable frequency feeder*TWLY20*100, Settling chamber, Silencer, Pulse dust collector, Rotary distributor*TFPX10,Outlet Screw conveyor, Scale hopper gate*TZMQS60*2, Pulse dust collector*TBLMa.6A, Small material checking balance*PLC0.25B, Scraper conveyor*TGSU32, Sewing machine and conveyor belt, etc.
Design Features of sinking fish feed processing line
When designing the aquatic feed processing technology, we need to understand the customer’s main product types, feed formula, production capacity, degree of automation requirements, and the amount of investment.
We will design a variety of plans according to the feeding requirements and feeding characteristics of the main product feeding objects of customers, and choose the best for use after comprehensive consideration.
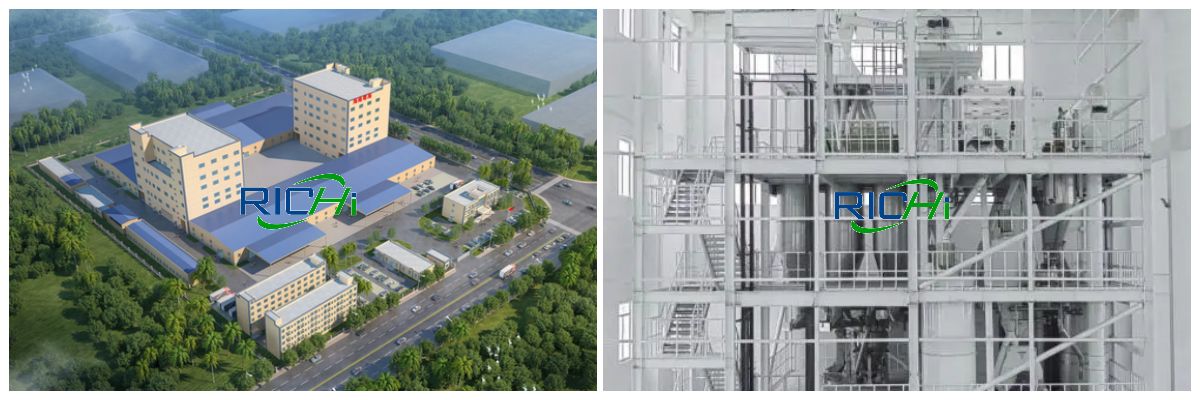
- When conditions permit, we suggest that customers should try their best to adopt advanced and complete fish feed process flow, advanced equipment and highly automated control equipment to ensure product quality, reduce energy consumption as much as possible, and reduce production costs.
- Our methods must be both targeted and flexible, aiming at the production of one or several types of aquatic feed, combined with different formulas, different raw materials and different feed shape requirements, as well as the characteristics of low and high seasons in aquaculture;
- For customers who process aquatic products and livestock and poultry feeds, they mainly produce aquatic feeds during the peak breeding season, and take into account the production of other types of feeds such as livestock and poultry feeds during the off-season, so as to improve the utilization rate of sinking fish feed processing line equipment and avoid equipment due to long-term shutdown.
- When the production capacity is not high, the output is small and the product variety is single, on the premise of ensuring the quality of the feed, it is recommended that the customer adopt a relatively simple fish feed pellet production line process to reduce investment and cost.
- When the production scale is large and there are many product varieties, it is recommended that customers adopt more complete technological processes and more advanced equipment to improve the degree of automation control to ensure product quality and meet various needs of users.
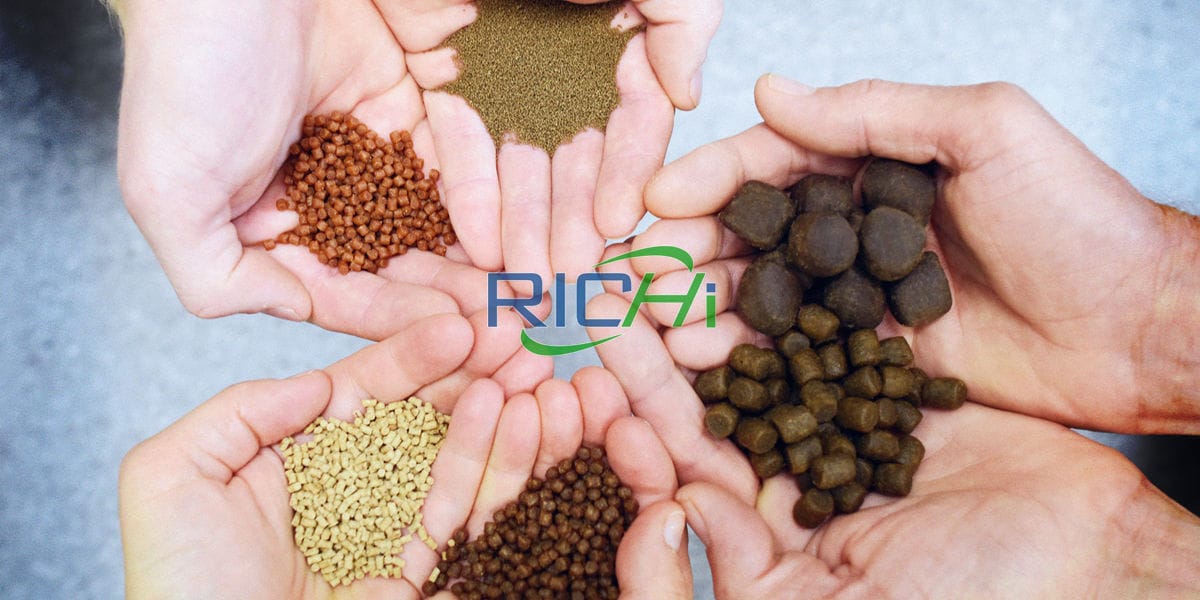
- When selecting sinking fish feed processing line equipment, ensure that the processing capacity of each feed equipment matches;
- It is recommended to use stainless steel for the machine shell that is in contact with steam during processing to improve its corrosion resistance and prolong the service life of the equipment.
- It should be considered that aquatic products are generally smaller than livestock and poultry products, and the food intake per time is small, and the requirements for raw material crushing and mixing are high. Generally, the micro-grinding or ultra-fine pulverization process is considered in the process arrangement, and whether it is equipped with a micro-powder classifier.
- Whether to add more oil or not, use mixing equipment with high mixing precision.
- For aquatic feeds that require water stability, conditioning, aging, and drying processes should be arranged in the process to ensure the stability of the feed in water, reduce water pollution, and improve feed utilization.
sinking fish feed processing line project
RICHI makes products honestly and provides services with heart. Delivering products to customers is only the first step.
Adhering to the concept of “customer satisfaction is our aim”, RICHI highly focuses on customer needs, not only ensuring the timely delivery of various equipment, but also effectively ensuring the operational efficiency of your aqua feed mills, ensuring that every customers started working without worry.
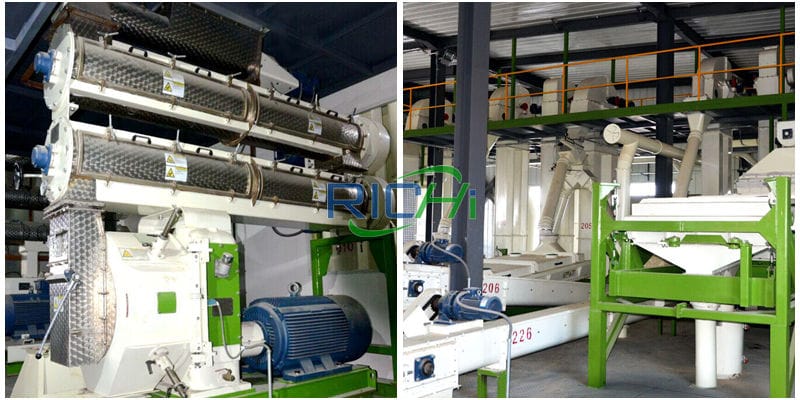
1T/H
1T/H Sinking Fish Feed Pelleting Line In Thailand
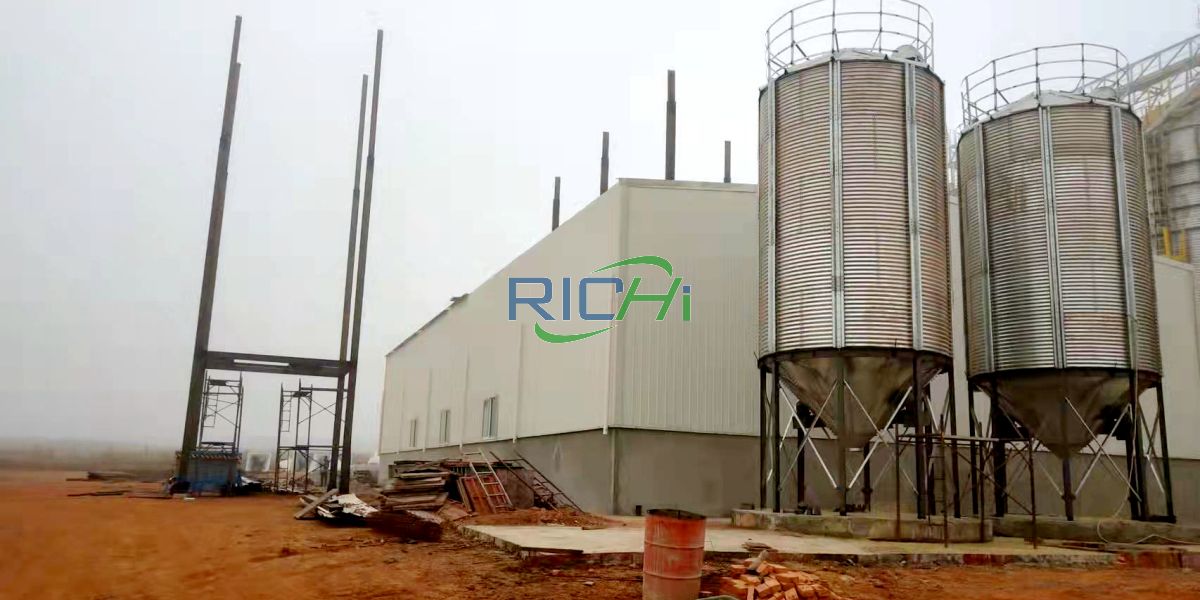
5-7T/H
5-7 T/H Sinking Fish Feed Pelletizing Plant In Angola
Technological process of sinking fish feed processing line
The technological process of RICHI sinking fish feed pellets line mainly includes feed raw material reception, raw material removal of impurities and iron, crushing or micro-grinding, ultra-fine crushing, batching, mixing, conveying, pelleting, aging, cooling, crushing, screening, weighing and packaging, etc.
The fish feed line investment is not large, and the product quality is guaranteed. This fish feed making process is a relatively advanced and practical process suitable for the production of sinking fish feed in various countries.
① Feed raw material reception, raw material removal of impurities and iron are the same as the general livestock and poultry feed production process requirements, no special requirements are required.
② Crushing is one of the key processes in aquatic feed processing. If the one-time fine crushing cannot meet the crushing requirements completely, it is necessary to match the fine powder classification or ultrafine powder classification equipment, so that the unqualified coarse particles after crushing are crushed again after passing through the classification equipment. The grading machine can be adjusted to suit different fineness requirements.
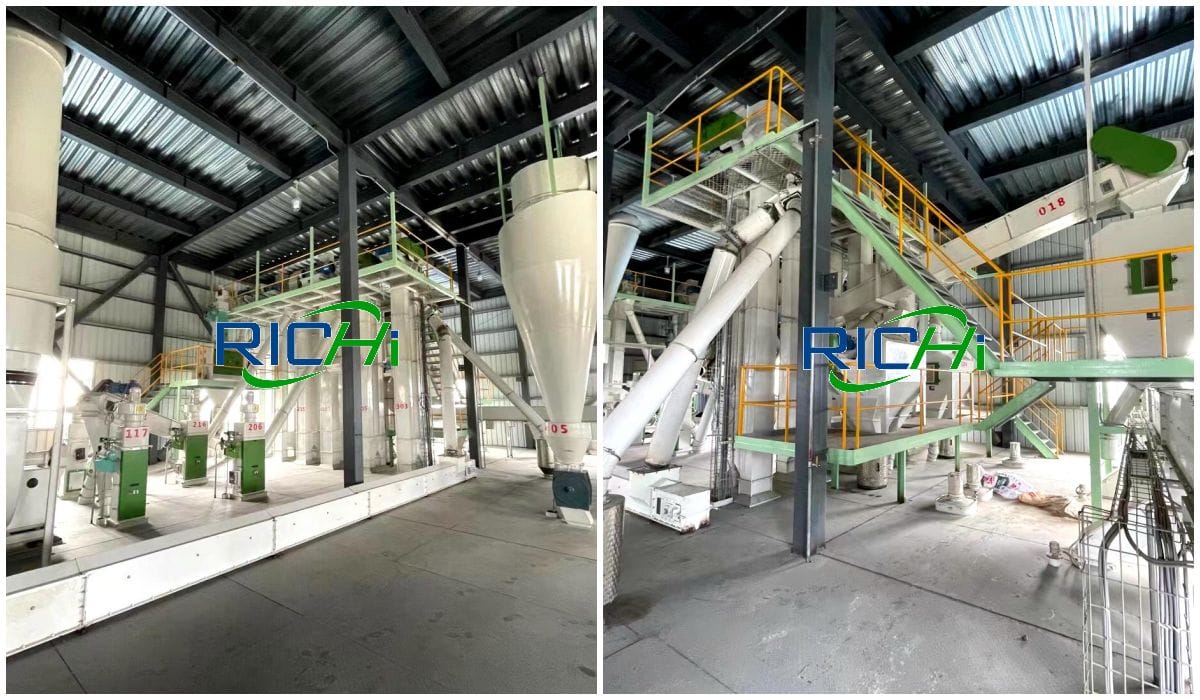
③ Mixing is also one of the key processes in the sinking fish feed processing line. Whether the mixing is uniform directly affects the stability of feed quality. The purpose of mixing is to mix various nutrients evenly, so that the feeding object can obtain all the nutrients needed in each feeding.
Compared with other mixers, the double-shaft horizontal mixer has the advantages of uniform mixing, less mixing residue, easy cleaning, more oil can be added, and short mixing time. Therefore, it gradually replaces the previously commonly used single-shaft mixer in aquatic feed mill processing.
④ If the granulation process is required, an appropriate fish feed pellet machine should be selected. For fish feed that requires high stability in water, a fish feed pellet making machine with a multi-layer conditioning cylinder structure should be selected.
So that the raw materials have more heating and humidifying time before granulation, increase the gelatinization rate of starch, and enhance the adhesion between particles. to improve stability in water. Adding appropriate binders to the raw materials also helps to improve the stability of the feed in water.
⑤ The granulated pellets contain high moisture content and must be cooled (some must be matured, dried, and cooled) to obtain qualified feed. During the conditioning, the feed is heated, kept warm and moisturized, which is conducive to the further gelatinization of starch.
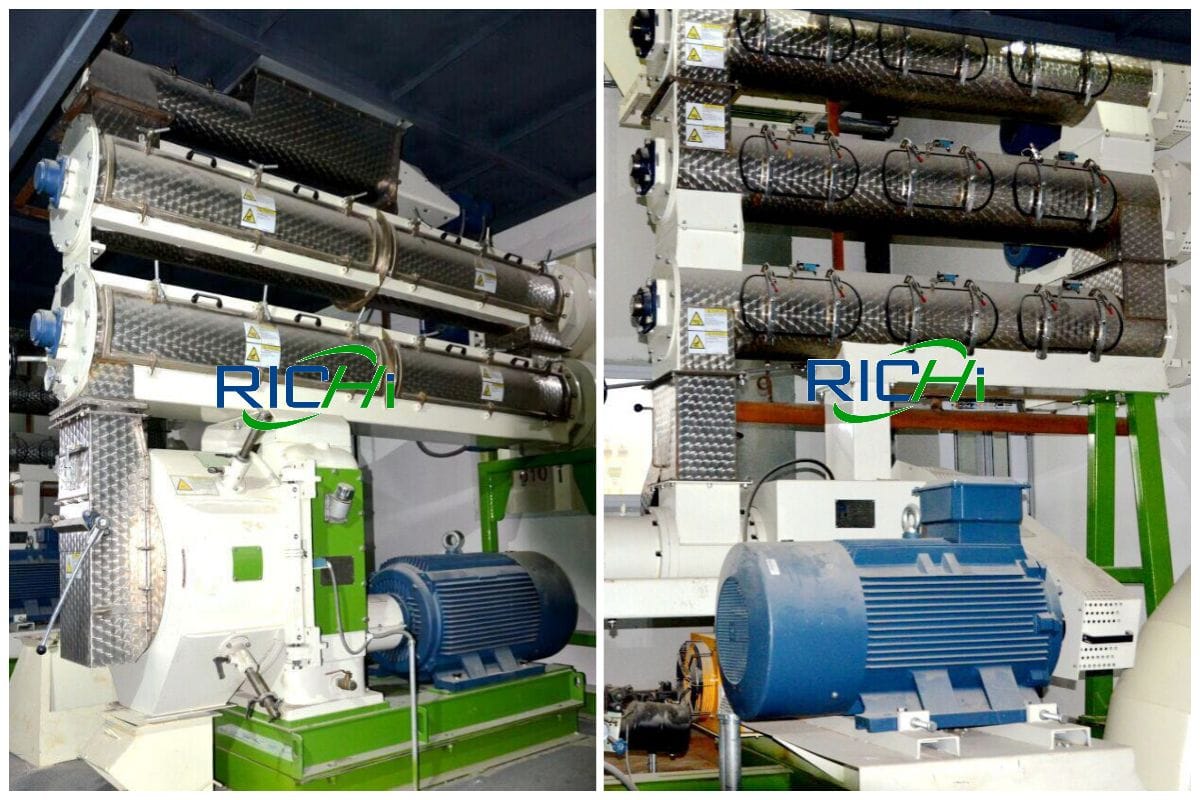
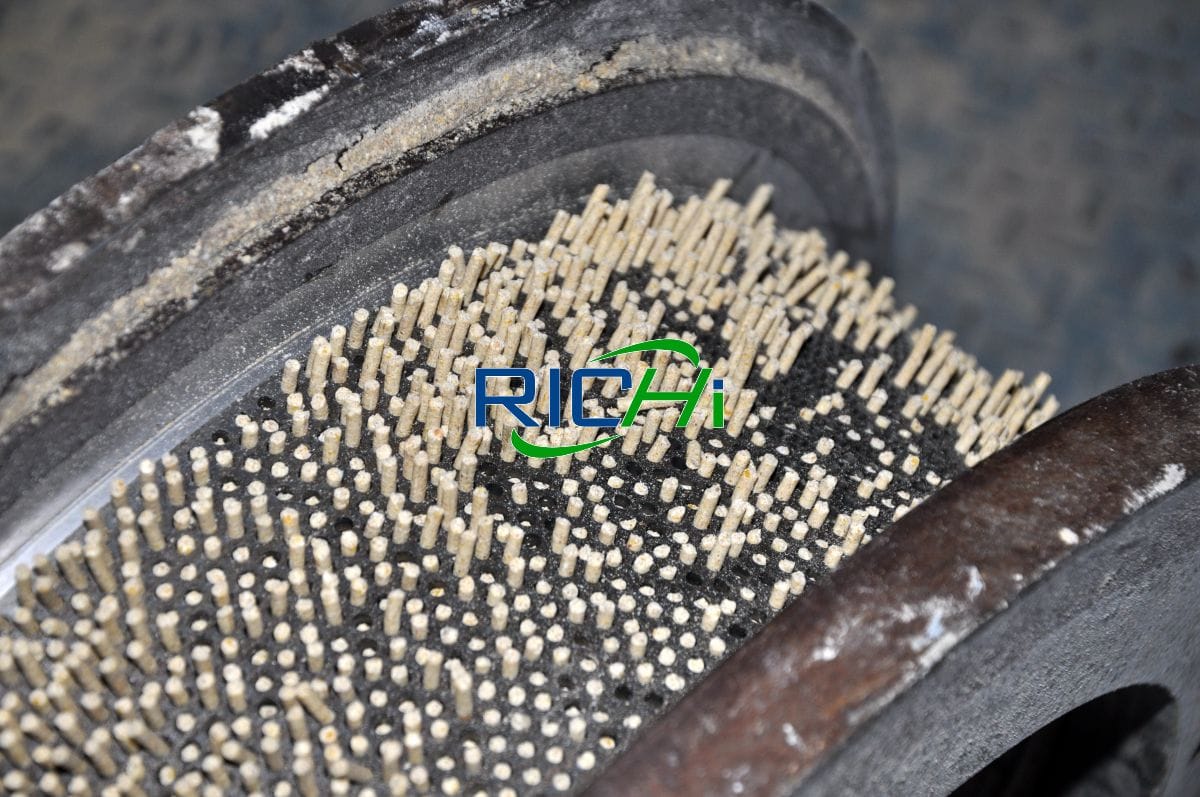
When drying, heating and dehumidifying the feed is also conducive to the gelatinization of starch, reducing the moisture content, and obtaining a firmer feed. After drying, after rapid cooling, the moisture content is reduced to the safe storage requirement and the feed temperature is lowered.
⑥ After sieving, the finished fish pellets can be obtained, which can be sold in the factory after weighing and packaging.
In order to obtain high-quality aquatic feed, we usually focus on the feeding characteristics of aquatic products fed by customers’ main products, ensure all the nutrients they need, design reasonable aquatic feed processing technology, and select appropriate aqua feed production line equipment for customers.
Equipment for sinking fish feed processing line
The equipment of sunken fish feed production line is the flagship product of RICHI’s aquatic products series, which can process a variety of pelleted feeds, and can provide customers with integrated comprehensive processing of aquatic feeds integrating crushing, mixing, pelletizing, cooling, crushing, screening, and packaging. solution.
The following are the main equipment for setting up a sunken fish feed factory:
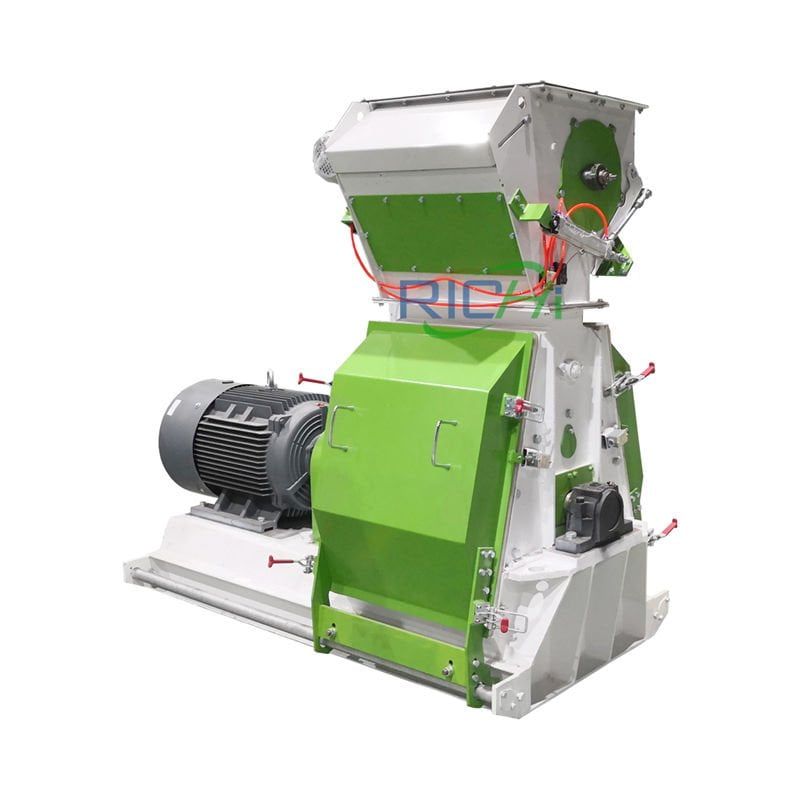
Fish Feed Grinder
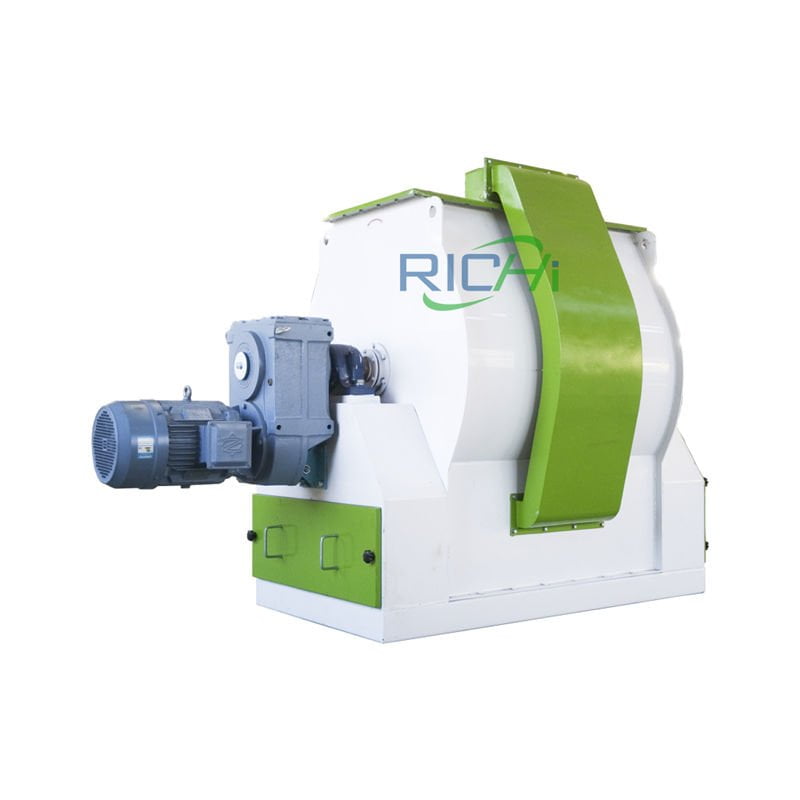
Fish Feed Mixer
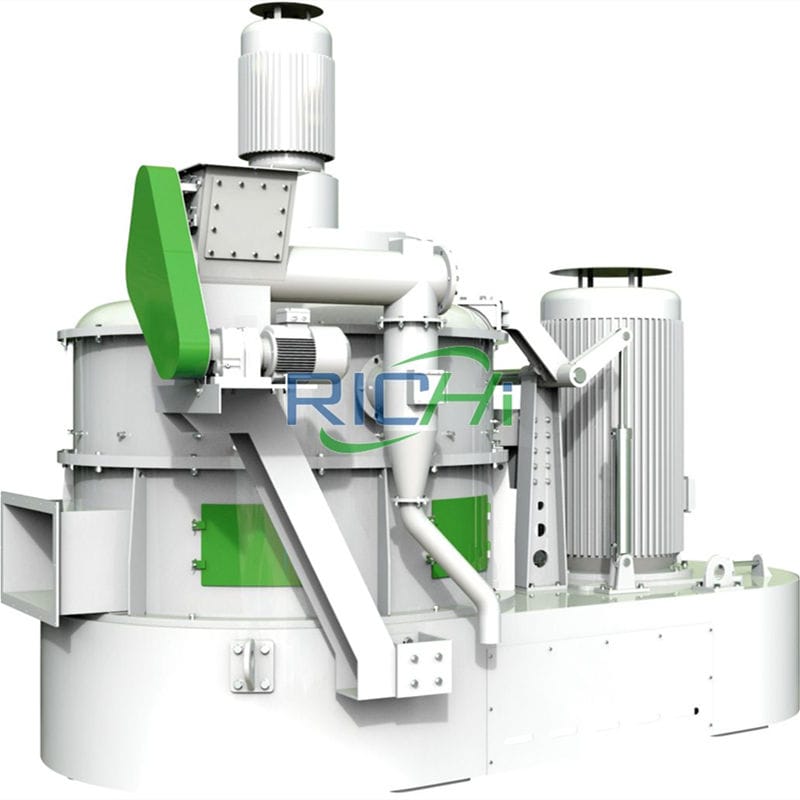
Ultrafine Grinder
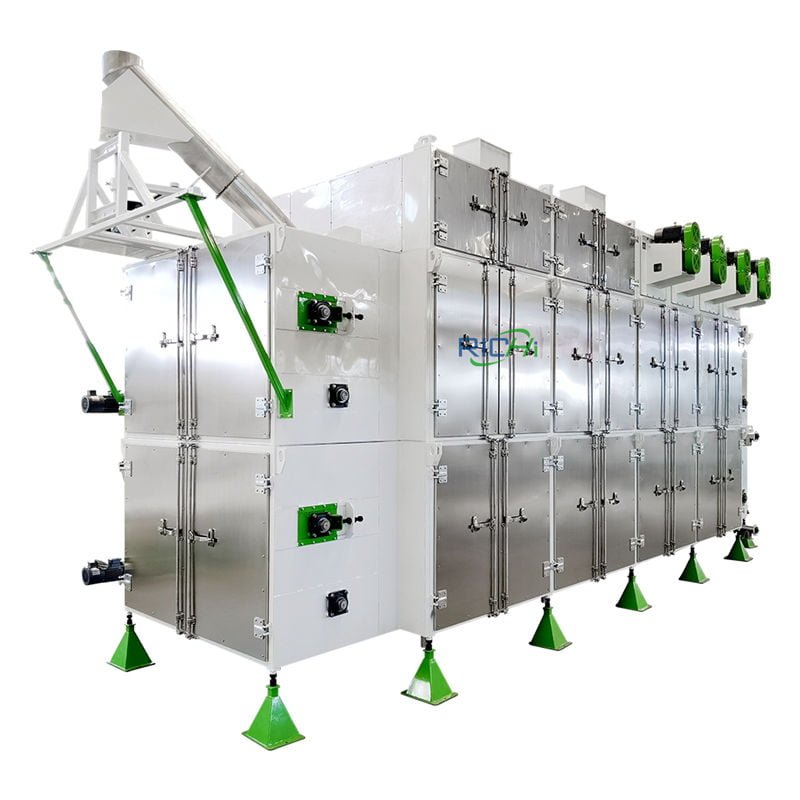
Fish Feed Dryer
Sinking fish feed processing line business plan
Key technical indicators of sinking fish feed processing line
The production process of sinking fish feed is the most important core part in the whole fish feed production plant.
Therefore, it is necessary to conscientiously implement the specific operation process of each post and each step in each link in this process, in order to achieve the goal of product quality and safety.
By decomposing and quantifying the quality indicators of each post and step in the processing process, the comprehensive quality and safety indicators of the final product can be achieved.
1. Raw material removal rate
In the process of sinking fish feed processing line, the first thing is to check and remove foreign matter such as large and small sundries and metals mixed in the raw materials. There are two commonly used methods of grid sieve and magnetic sieve.
Generally, the impurity removal rate is required to reach more than 99.5%, and the removal rate of large debris is required to reach 100%.
2. Raw material crushing size
- The particle size of raw material crushing directly affects the digestion and absorption of fish, crushing cost, subsequent processing procedures and product quality.
- The digestive tract of fish and shrimp is short and the digestion and absorption function is weak. In order to increase the contact area between the feed and the intestine and improve the utilization rate of digestion and absorption. Therefore, it is required to increase the crushing fineness of the material as much as possible.
- The raw material has a small particle size, which can also improve the uniformity of the feed and the water resistance of the pellets.
Different fish species, different breeding specifications, different raw material compositions, different tempering, aging and molding methods, etc., the sinking fish feed processing line have different requirements for the particle size of the feed, so many national feed quality standards specify the size of the particle size of the raw materials.
3. Mixing uniformity
For general fish and prawns, the requirement is ≤10%, while for juvenile flounder, herring, red sea bream, black eel, etc., the requirement is ≤8%, etc.
4. Stability in water
According to the aquatic industry standard:
- The dissolution rate of sinking pellet compound feed is ≤10% within 5 minutes of immersion;
- The dissolution rate of extruded pellet compound feed is ≤10% within 20 minutes of immersion; ≤5%;
- The dissolution rate of prawn compound feed is ≤10% within 120 minutes of soaking.
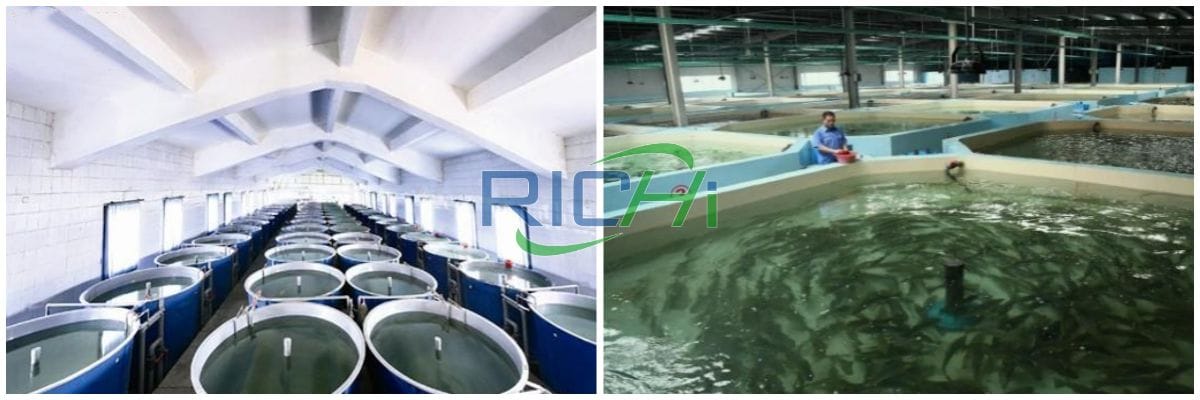
5. Starch gelatinization degree
The gelatinization degree of feed is generally required:
- The gelatinization degree of puffed floating pellet compound feed starch is ≥90%;
- The gelatinization degree of puffed sinking pellet compound feed starch is ≥70%;
- The gelatinization degree of pelletized sinking fish feed pellet starch is about 30%.
6. Floating and sinking
- Feed with a large degree of expansion has a small bulk density, which is a buoyant feed, and its bulk density ranges from 320g/L to 400 g/L;
- Feed with a small expansion degree has a large volume and is a sinking feed, and its volume ranges from 450g/L to 550 g/L;
- The bulk density of slow-sinking feed is between floating feed and sinking feed, and its bulk density ranges from 380g/L to 410 g/L.
In general, the floating rate of extruded floating pellet feed should be ≥95%. The sinking rate refers to the number of sinking within 30 seconds after 100 pellets are randomly selected and placed in 3.5% salt water at 20℃ after being dried. The sinking rate is required to reach more than 98%.
7. Powder content and pulverization rate
The aquatic industry standard only puts forward the requirements for the pulverization rate of hard pellet feed and extruded pellet feed, but does not put forward specific requirements for the powder content rate.
It is stipulated that the pulverization rate of hard pellet feed should be ≤10%; rate should be ≤1%.
8. Pellet diameter
The diameter of the pellet feed must match the size of the caliber of the cultured fish, so that it is beneficial for the fish to eat.
- If the diameter is too large, it is difficult for fish to swallow, and they can only eat it after the feed is soaked soft, which not only increases the loss of water-soluble feed components, but also causes water pollution;
- If the pellets are too small, the fish must feed many times to meet the needs, because the prolonged feeding time will not only increase the waste of feed, but also increase the consumption of energy.
For pellet feed with too small pellet size, it is necessary to consider reducing energy consumption in the sinking fish feed processing line process and also consider the constraints of processing technology, so crushed feed can be used.
It is to crush the large-grained feed and sieve it into many crumbs or coarse chips of different sizes through different standards to meet the different needs of feeding various sizes of young, immature, juvenile and adult fish.
The pellet length is generally 1.5 to 2.0 times the particle diameter. Different cultured species of fish have different requirements for the particle size of pellet feed at different development and growth stages.
9. Moisture content
- The moisture content of general fish compound feed is about 11% to 13%, of which the moisture content is not more than 14% in areas with relatively dry climates, and not more than 12.5% in areas with humid climates.
- Fishing compound feed generally requires that the moisture content should be controlled below 10% to 12%. The method of testing the water content in the feed is to dry the sample in an oven at 105°C±2°C, and dry it under atmospheric pressure until it has a constant weight, and the lost weight is water.
In order to ensure the quality and safety of feed, different feed raw materials and different feed products have different requirements for their moisture content.
10. Nutritional indicators
Feed products from the sinking fish feed processing line, after on-site comprehensive testing before packaging, the actual nutrients contained in the feed products must meet the physiological nutritional needs of the breeding objects and the nutritional indicators required in the feed formula and the label of the ex-factory feed product.
11. Hygienic indicators
After on-site comprehensive inspection before packaging, the quality of feed products must meet the requirements of various indicators in the feed hygiene standards.
12. Weighing accuracy
Accurate weighing is strictly required. The scale must be calibrated frequently, especially for small materials and pharmaceutical additives, the accuracy of weighing directly affects the quality of feed products.
Generally, the weighing error is required to be ±0.2%, and the error requirement for pharmaceutical additives must be within the range of ±0.1%.
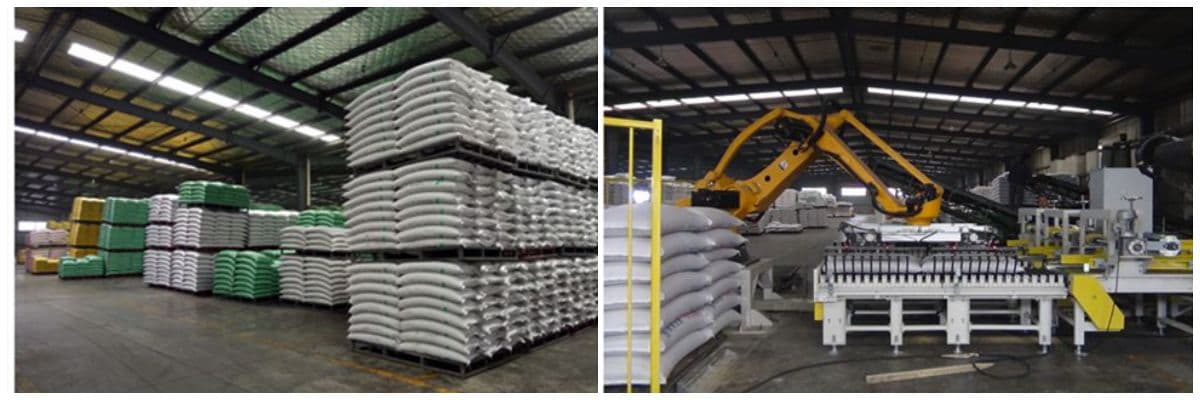
13. Sensory indicators
- Usually requires uniform color;
- It has the inherent smell of normal feed, no rancidity, no oil burning, no mold, no deterioration, no agglomeration, no insect damage, etc.;
- Compact particle structure, smooth surface, no cracks, uniform shape and size.
- For eel and soft-shelled turtle powder feed, it is required to add appropriate amount of water and oil and then stir evenly to form a dough, which has good extensibility and viscoelasticity.
FAQ
Regarding this question, we also need to know what kind of animal feed you want to produce, and what is the output of processed sinking fish feed and animal feed?
According to the output of sinking fish feed and livestock and poultry feed, the process and equipment configuration of the fish feed factory are different, which will eventually affect the price of the complete feed processing line.
In addition, we will provide each customer with free production line customization services, and provide a full set of drawings, including plant layout, equipment layout, process flow diagram, steel frame diagram, etc.
The 6 ton hr fish feed processing line price is generally between 40,000 and 250,000 US dollars. Regarding the freight, please contact the online customer personnel directly to obtain the latest port quotation.
Yes, and we have exported several feed production lines to Kenya. Welcome to contact us for more details!
Please provide us with the capacity of the fish feed line you need, so that we can provide you with an accurate quotation list for the equipment.
SZLH250 and SZLH320 sinking fish feed pellets machine price is generally between 7000-20000 USD. For more details: please visit: SZLH250 Sinking Fish Feed Pellet Mill and SZLH320 Fish Feed Pelleting Machine.
In addition, SZLH250 sinking fish feed processing line cost is about 10000-60000USD, SZLH 320 fish feed mill machine cost is about 18000-100000USD.
You also need to tell us whether you want a single machine or a complete feed production line, and what is the output you need? This will allow us to provide you with an accurate quotation.
– 1000Kg/h fish feed pellet production line.
– 1000kg/h poultry feed feed pellet production line
Best regards.
What we need to know is, do you want to build two production lines or the same production line to produce fish feed and poultry feed? Whether the process you want to use is granulation process or puffing process.
The price of 1 ton of fish feed pellet production line is similar to the price of 1 ton of poultry feed feed pellet production line, both are between 10,000-70,000 US dollars. If you want to build a joint feed line, then we will customize it according to your plant, and you need to determine the process first and then determine the price.
5-8 T/H fish feed processing line in Tanzania generally costs 40,000-300,000 US dollars.