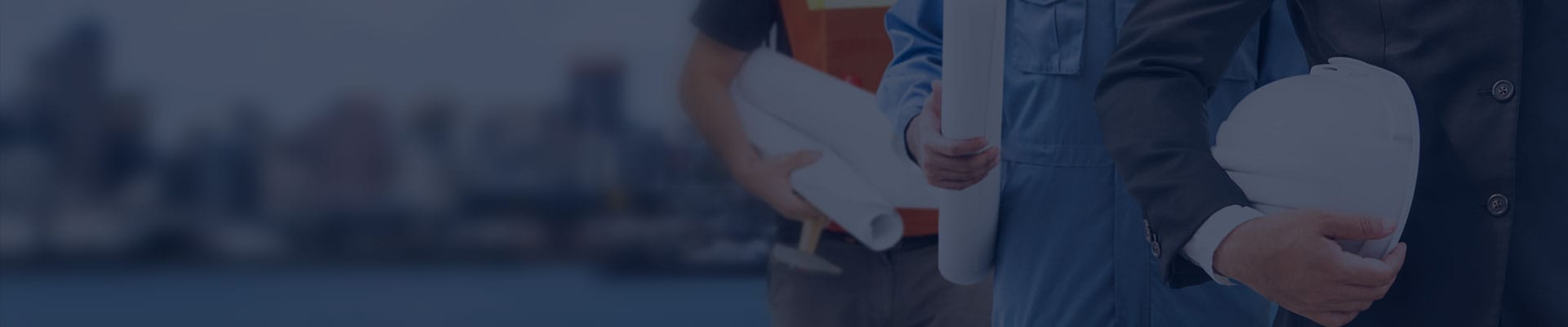
Our Service Philosophy
Richi Machinery always adheres to customer-centric, provides EPC one-stop service, and tailors high-quality aqua feed production line design and feed equipment for customers. Whether it is pre-sales, in-sales or after-sales links, we always actively listen to customer needs, combined with the actual feedback from tens of thousands of users at home and abroad, continue to improve and upgrade, devote themselves to the development of high-precision products, and sincerely provide customers with professional services.
SERVICE GUARANTEE
Our service promise is not a slogan, a concept or an advertisement, our service promise is serious. To this end, we have built a large, systematic and standardized service guarantee system to ensure that each link is implemented in place and finely processed.
30 min
Reply to technical consultation
24 hrs
Reply to technical consultation
24/72 hrs
Reply to technical consultation
12/24 hrs
Reply to technical consultation
TURNKEY SERVICE
From the initial consultation to plan design, site visits, to the subsequent stocking and delivery, after-sales complaints and feedback, etc., Richi Machinery has built a complete system to effectively ensure the timely and quick transmission of information, and ensure that the right people provide it at the right time.
Our company’s more professional service and technical support. Our full-process pellet plant solutions include consulting, design, civil engineering, manufacturing, logistics, installation and commissioning, training and services. At the same time, we also provide equipment and pellet production line transformation and upgrading services.
PROFESSIONAL ANSWERS
Whether you are in China or a corner of the world, you can contact us at any time, because Richi Machinery has built an online consulting service team of more than 20 people to serve you around the clock, 365 days a year.
Global Service
Professional Service Team
365 Days Full Service
TAILOR-MADE
At Richi Machinery, we adhere to the one-to-one targeted design of high-quality solutions, and use the professional knowledge and full-cycle services of our account managers to help customers carry out project operations, and thoroughly solve customers’ equipment procurement, operating cost accounting, operation management and after-sales service. In order to improve the profitability of customers and realize the sustainable development of the business.
One-to-one service
Equipment Purchase
Operating cost
Operation management
After-sales service
At the stage when the customer can only carry out the conception, Richi Machinery engineers can provide design consulting services based on the blueprint drawn by the customer; at the same time, provide consulting services for factors that may affect the construction of the pellet plant project, including existing facilities, structural conditions, fire protection requirements, clear height, capacity of municipal public facilities, environmental assessment application, etc.
ASSIST IN THE FORMULATION/ CONSTRUCTION PLAN
In order to better, safer, and more economical civil construction and other construction projects, Richi Machinery rely on the professional knowledge and rich experience in construction, we can shorten the construction period, optimize the pellet plant design, reduce the pellet plant cost, and improve the overall efficiency of the pellet production line project.
We will provide an estimate service for the cost of the proposed pellet plant project based on the basic design parameters, project location and related infrastructure.
Richi Machinery has undertaken the design and construction of thousands of feed mills, biomass wood pellet mill plants and organic fertilizer production plants. We believe that with leading one-stop solutions, global experience and localized services combined with customers’ local expertise, Richi Machinery will increase the growth rate, promote new growth and further promote the development of the global agri-food, biomass and organic fertilizer industry.
EQUIPMENT MANUFACTURING AND TESTING
Advanced technology to produce excellent products. Through cooperation with excellent companies, we have introduced advanced production technology from different industries and global feed factory control technology to RICHI, equipped with advanced processing equipment, and realized high-precision mechanical processing and assembly production processes, to provide you with products that strive for excellence.
After the equipment is processed, in order to allow customers to fully understand the quality and operation of the new equipment, as a provider of professional granular equipment and engineering overall solutions, we can not only provide customers with testing services from a single unit to a complete system (Including all hosts and auxiliary equipment such as granulator, grinder, mixer, etc.).
In addition, in the early stage of equipment procurement, we can obtain the real data of customer raw materials through quality inspection equipment (mainly for biomass raw materials), so as to have a clearer understanding of equipment effects (such as compression ratio, output, pass-through rate, etc.).
The experienced RICHI engineers will reasonably adjust the equipment configuration according to the actual data obtained according to the raw material characteristics, and provide you with a scientific and reasonable equipment plan, so that you can “select the model without worry”.
STANDARDIZE PACKAGING AND DELIVERY
Checking stock order
The merchandiser verifies the model, quantity and accessories of the equipment ordered by the customer in detail in accordance with the sales contract to ensure that the stock is fully matched with the order.
Factory quality inspection of equipment
After the production system completes the equipment production, the quality inspector strictly inspects the records item by item according to the quality inspection details to ensure the quality of each equipment to be installed.
Re-inspection of packing list
Before the equipment is packed and sent, the documentary specialist will check the packing list one by one to avoid the phenomenon of missed delivery.
Scientific packaging and transportation
The merchandiser verifies the model, quantity and accessories of the equipment ordered by the customer in detail in accordance with the sales contract to ensure that the stock is fully matched with the order.
INSTALLATION AND COMMISSIONING
According to customer needs, Richi Machinery installation engineers will guide the construction of site infrastructure, equipment installation and commissioning, and trial operation of the entire pellet production line. When the relevant project indicators meet the design standards, the customer will sign the project and pass the acceptance.
Closely integrated with Richi Machinery’s business operations, we have assembled and specialized a large team of installation engineers, subdivided into feed mill engineering business installation engineers, biomass wood pellets production business installation engineers, and organic fertilizer engineering technology installation engineers. In each field, a mix of old, middle and young people is formed to effectively guarantee the construction of talent echelon and the needs of business employment.
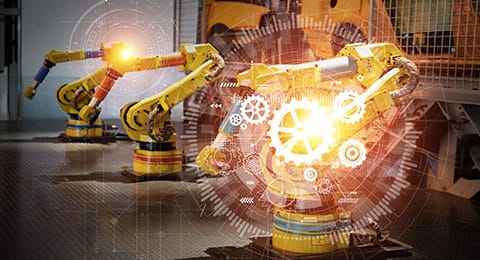
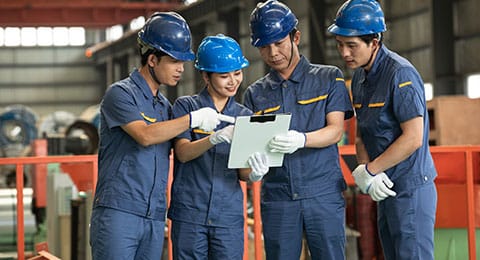
OPERATOR TRAINING
Richi Machinery provides comprehensive and systematic training for the technical staff of each user to better serve the needs of customers’ projects. After the technicians have finished their studies, they will return to the project during the operation period. Richi Machinery will provide follow-up technical support services. The training lecturer will follow up the training effect in the later stage to ensure the stable operation of the customer’s project.
Training Content:
- System training
- Installation skills training
- Equipment structure and principle training
- Fault judgment and troubleshooting training
- Equipment maintenance training
- Equipment operation training
- Core component introduction training
- Accessory installation training
- Field operation training
- Production process training
- Raw material processing technology training
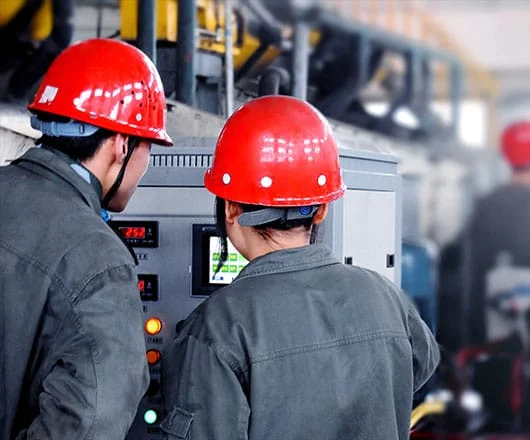
RETURN VISIT TO THE PROJECT SITE
As an enterprise integrating R&D, production, sales and service, Richi Machinery attaches great importance to customer communication. Therefore, we provide regular return visits to help users optimize and maintain equipment, and analyze and solve equipment problems reported by customers in a timely manner.
(Due to the special period of the new crown epidemic, almost all overseas on-site return visits are carried out online. Although the format is changed, we will not fail to do it. Because this is a part and tradition of our service system.)
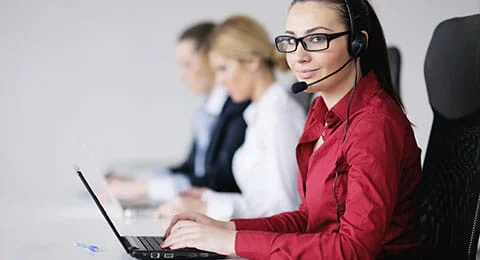
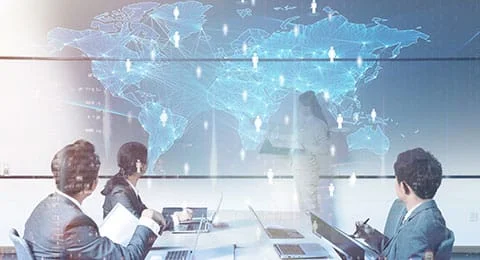
AFTER-SALE WARRANTY
Three Guarantees Service
The product implements three guarantees, the warranty period is half a year, and no wearing parts are included. (Note: The three guarantees of products refer to the repairs, replacements, and returns that need to be carried out due to quality problems), which are the direct expenses within the scope of the three guarantees, such as direct expenses such as freight, accessories, and accommodation and travel expenses for the three guarantees of technicians. Undertake or refund the loan within this contract. Party A shall not bear the above expenses and indirect losses and expenses other than the loan in this contract. Party A sends technicians to guide the installation and commissioning, and Party B is responsible for the board and lodging of the technicians.
One Year Warranty
The warranty period of Richi Machinery’s granulator, grinder, mixer and other series of host equipment is calculated from the date of acceptance of the unit adjustment test. The user can enjoy a free one-year warranty service for the whole machine with the invoice and warranty certificate, that is, the equipment within the warranty period is in normal use Under the circumstances, the maintenance costs incurred by the maintenance caused by the quality problems of the unit itself shall be borne by Richi Machinery.
Spare Parts
Richi Machinery regards product quality as the life of the company. The main components and vulnerable parts are made of high-quality wear-resistant materials and good processing technology to make the equipment durable.
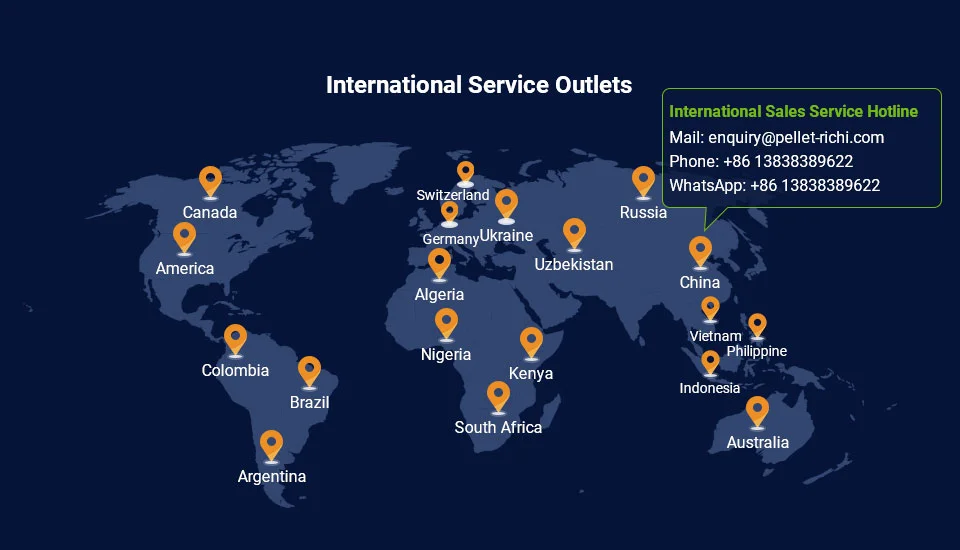
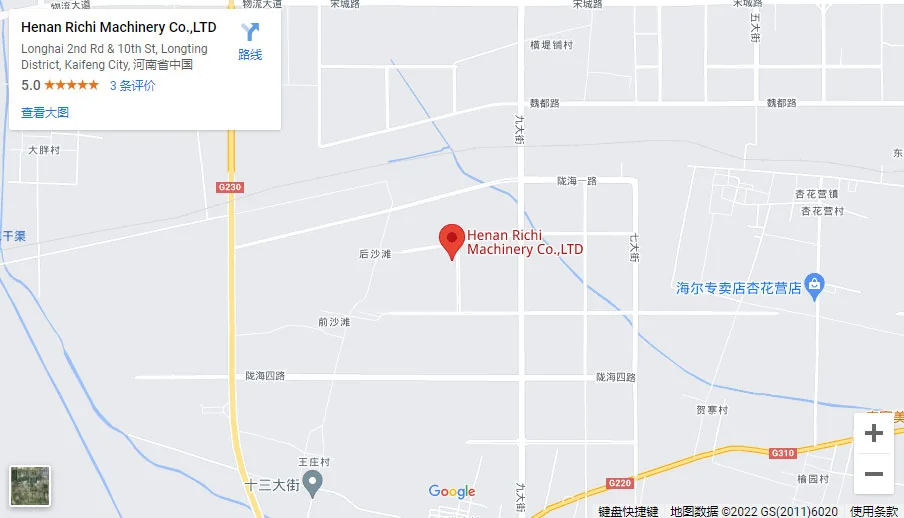
SERVICE GUARANTEE
Strong hardware facilities, solid backing beyond personnel and processes.
EQUIPMENT WORKSHOP
THE WORLD’S TOP PROCESSING AND MANUFACTURING EQUIPMENT ASSISTS THE WHOLE PROCESS
- 180,000 square meters of production base;
- Heavy modern integrated production and assembly workshop;
- Nearly 100 sets of domestic advanced large-scale vertical lathes, planers and other equipment.
TOOLING ABILITY
FOCUS ON EVERY PRECISION PROCESS AND MAINTENANCE
- Adopt aging treatment technology, equipped with high-precision tooling equipment;
- Build a full range of manufacturing processes from R&D to quality inspection based on standard operations and on-site improvements.
EQUIPMENT WORKSHOP
INDEPENDENT SPACE,INDEPENDENT OPERATION,WIN THE TRUST OF CUSTOMERS BY STANDARDIZATION
- Feed mill equipment manufacturing base;
- Biomass pellet plant equipment manufacturing base;
- Large-scale organic fertilizer granulation equipment manufacturing base.
PROCESS QUALIT INSPECTION
USE PRECISION QUALITY INSPECTION INSTRUMENTS TO CAST HIGH-QUALITY EQUIPMENT
- We are committed to the research and development of a complete set of processing equipment for feed, biomass, and organic fertilizer;
- And to provide you with high-quality products and high-quality services.